Welding operations pose significant risks, including exposure to ultraviolet rays, fumes, and electric shocks. These hazards can lead to painful injuries or health issues for welders if safety protocols are not strictly followed. Implementing complete safety measures, such as using proper personal protective equipment and keeping a safe work environment, is crucial. By adhering to these practices, we can minimize the dangers associated with welding, protect workers, and ensure smooth and efficient operations. Prioritizing safety in welding is not just a regulatory requirement; it’s a vital aspect of maintaining a healthy and productive workforce.
Common Hazards in Welding
Some common hazards occur during the welding process; it is crucial to take precautionary measures to avoid them.
Ultraviolet and Infrared Rays
Welders are exposed to intense ultraviolet (UV) and infrared (IR) radiation during welding processes. UV rays can cause eye damage, commonly known as “welder’s flash”, “arc eye”, or photokeratitis, leading to painful inflammation of the cornea. Prolonged disclosure can also increase the risk of cataracts. IR radiation, although less hazardous, can still cause thermal burns. Welders need to wear appropriate eye and face protection, such as welding helmets with the correct shade filter, to shield against these harmful rays.
Fumes and Gases
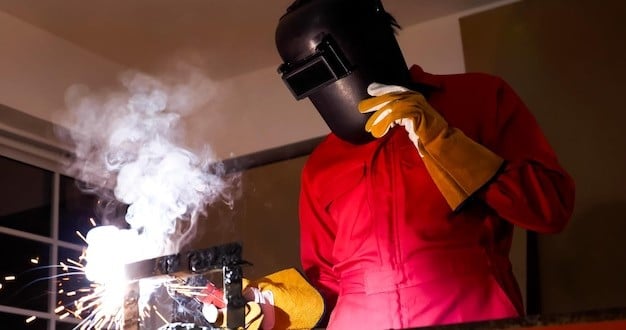
Welding, especially stick welding, generates harmful fumes and gases, including metal oxides, ozone, and nitrogen oxides. Inhaling these gases can cause respiratory issues, metal fume fever, and long-term health conditions like chronic bronchitis. The type and quantity of fumes depend on the welding process and materials used. Adequate ventilation and the use of respiratory protective equipment are vital to minimize exposure to these hazardous emissions.
Electric Shock
Electric shock is a significant risk in welding, especially when working with electrical arc welding equipment. Contact with live electrical parts can result in severe injury or even fatality. Wet conditions, as water conducts electricity, increase the likelihood of electric shock. Proper equipment grounding, regular cable inspection, and adherence to electrical safety protocols are crucial in preventing accidents.
Arc Flash
Arc flash incidents occur when an electrical discharge travels through the air between conductors or from a conductor to the ground. This phenomenon generates extremely high temperatures, capable of causing severe burns, eye injuries, and even fatalities. Welders must use protective clothing, face shields, and other arc-rated PPE to guard against arc flash hazards. Maintaining safe working distances and following proper procedures can also reduce the risk.
Fire and Explosions
Welding operations often produce sparks and molten metal, which can ignite flammable materials nearby. This risk is particularly high in confined or enclosed spaces. Fire safety measures, such as clearing the area of combustible materials, using fire-resistant blankets, and having fire extinguishers readily available, are essential. Additionally, training in emergency response procedures can help mitigate the consequences of any fire incidents.
Other Related Hazards
Welding hazards include noise exposure, which can lead to hearing loss, and repetitive stress injuries from awkward postures or repetitive motions. Proper ergonomics and the use of hearing protection can help manage these risks. Additionally, exposure to bright light from the welding arc can affect the skin, causing burns or increasing the risk of skin cancer. Comprehensive safety training and adherence to best practices are necessary to protect welders from these various hazards.
6 Essential Safety Tips
Gear and PPE
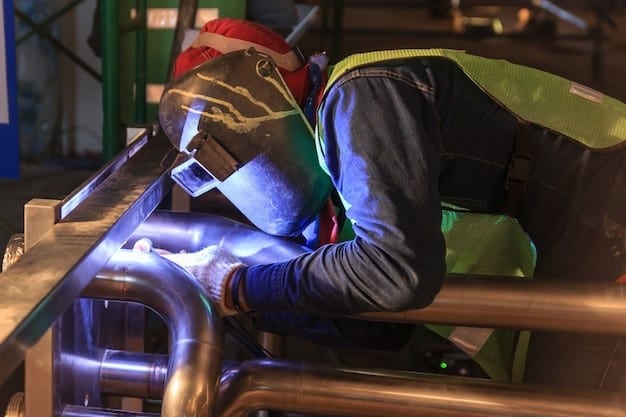
Personal Protective Equipment (PPE): Proper PPE is crucial for safeguarding against injuries in welding. This includes helmets with appropriate shade lenses, fire-resistant clothing, gloves, and safety boots. Helmets protect the face and eyes from harmful rays and flying debris. Fire-resistant clothing prevents burns from sparks and molten metal while welding gloves and boots protect the hands and feet from heat and sharp objects.
Respiratory Protection: Hazardous fumes and gases may be produced depending on the materials being welded. Respirators should be worn when adequate ventilation is not possible. Ensuring that all PPE fits correctly and is well-maintained is essential for maximum protection.
Protect Your Eyes and Skin from Light Exposure
Welding Helmet and Goggles: The intense light produced during welding, including ultraviolet and infrared rays, can damage the eyes. A welding helmet with a good filter shade is necessary to protect against arc flash. Remember to wear safety goggles or glasses under the helmet for extra protection.
Protective Clothing: Welders should wear long sleeves and pants made of flame-resistant materials to prevent skin burns. The skin must be covered completely to avoid exposure to harmful rays and sparks. Neck protectors and earplugs can also be used to protect sensitive areas from burns and noise.
Work Environment
Ventilation: Adequate ventilation is vital to remove hazardous fumes and gases from the welding area. Local exhaust systems can help capture and eliminate contaminants at the source. In confined spaces, special precautions, such as using respirators and ensuring proper airflow, are necessary to prevent asphyxiation.
Workspace Organization: Keeping the workspace clean and organized minimizes tripping hazards and the risk of fire. Flammable materials should be stored away from the welding area, and tools should be kept in designated places. Clear signage and barriers can help keep unauthorized personnel out of danger zones.
Avoid Repetitive Stress Injuries
Ergonomic Tools: Using tools designed to reduce strain can help prevent repetitive stress injuries. Ergonomic handles and adjustable workstations allow welders to maintain a comfortable posture, reducing the risk of long-term injuries.
Proper Technique: Training in proper welding techniques, including positioning and movement, is crucial. Avoiding awkward postures and taking regular breaks can also help reduce the risk of strain injuries. Stretching exercises before and after work can improve flexibility and reduce muscle tension.
Modern Technology
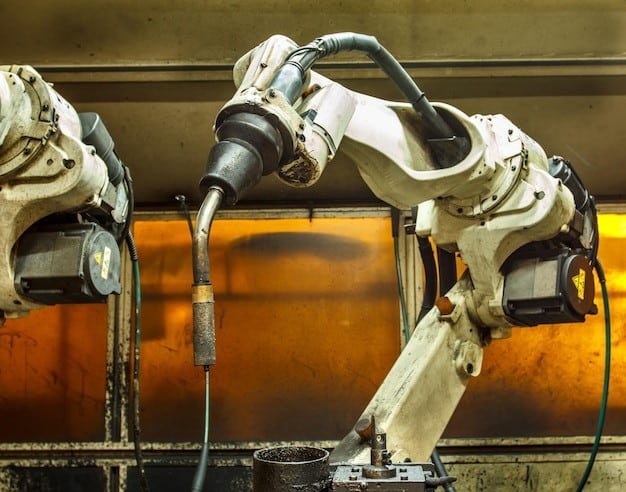
Advanced Welding Equipment: Utilizing modern welding equipment with safety features, such as automatic shut-off and overload protection, can enhance safety. These features help prevent accidents caused by equipment malfunctions or user errors.
CNC and Robotics: Implementing CNC and robotic welding systems can minimize human exposure to hazardous conditions. Automated systems can perform repetitive and dangerous tasks, allowing welders to focus on monitoring and controlling the process from a safe distance.
Safety Inspections
Regular Equipment Checks: Regular inspections and maintenance of welding equipment are essential to ensure they are in good working condition. This includes checking for damaged cables, faulty connections, and worn-out parts. Proper maintenance helps prevent accidents caused by equipment failure.
Workplace Safety Audits: Conducting regular safety audits of the workplace can identify potential hazards and areas for improvement. These audits should include reviewing safety protocols, inspecting the work environment, and assessing the use of PPE. Implementing disciplinary actions based on audit findings can significantly enhance workplace safety.
The Major Benefits of Safety Precautions
Safety Tips | Benefits |
Use Proper PPE | Prevents burns and eye injuries Protects against UV and IR exposure |
Ensure Adequate Ventilation | Reduces inhalation of toxic fumes Maintains a safe breathing environment |
Regular Equipment Inspections | Identifies potential hazards early Ensures equipment functions correctly |
Use Fire-Resistant Materials | Prevents fires from sparks Protects work environment |
Maintain Clean Work Area | Reduces risk of fire and accidents Improves overall safety |
Use Insulated Tools | Prevents electric shocks Reduces risk of injury |
Implement Lockout/Tagout Procedures | Ensures safe equipment maintenance Prevents unauthorized use |
Training and Education | Enhances knowledge of safety practices Promotes safe work culture |
Avoid Clutter in Workspace | Prevents accidents from falling objects Increases efficiency |
Monitor Health for Fume Exposure | Protects respiratory health Prevents long-term health issues |
Use Proper Welding Techniques | Improves welding quality and safety Ensures proper welds |
Plan Emergency Procedures | Prepares for emergency situations Minimizes damage and injuries |
Final Thoughts
Safety in welding is paramount, as it helps prevent injuries and ensures smooth operations. Key safety practices, such as using appropriate personal protective equipment, keeping a clean work environment, and conducting regular safety inspections, are crucial. Equally important is sourcing reliable welding equipment from trusted welding machine suppliers. High-quality equipment with safety features reduces the risk of accidents and enhances efficiency. By prioritizing safety measures and using dependable tools, welders can protect themselves and others, creating a secure workplace. Investing in proper safety protocols and equipment is an investment in the well-being and productivity of all involved.
FAQs
What personal protective equipment (PPE) is essential for welders?
Essential PPE includes welding helmets, gloves, jackets, boots, and respirators. These items protect against burns, electric shock, fumes, and noise. Proper PPE is crucial for maintaining safety and preventing injuries in welding environments.
What are the main hazards associated with welding?
The primary hazards include exposure to ultraviolet and infrared rays, harmful fumes and gases, electric shock, arc flashes, and fire. Each of these risks can cause serious health issues or injuries if proper safety measures are not taken.
What safety standards do welders need to follow?
Welders should adhere to the Occupational Safety and Health Administration (OSHA) standards, particularly 29 CFR 1910.252, which outlines requirements for safe welding practices. This includes providing appropriate PPE, ensuring proper ventilation, and following safety protocols for handling equipment .
How can welders prevent electric shocks?
To prevent electric shocks, welders should always inspect equipment for damage, wear insulated gloves, and avoid touching live electrical parts. Proper grounding and dry insulation between the welder and the ground are also crucial.