The welding industry needs innovative solutions to address productivity, precision, and sustainability challenges. As traditional methods struggle to meet the demands of modern manufacturing, businesses require advanced technologies to stay competitive.
Emerging trends, such as automation, eco-friendly processes, and data-driven systems, provide practical answers to these issues. These advancements improve operational efficiency and mental impact, catering to the evolving needs of industries worldwide.
This article explores the top welding trends shaping 2025, highlighting how these innovations transform welding into a smarter, greener, and more efficient process. By understanding and adopting these trends, businesses can achieve higher performance and long-term growth in the competitive welding market.
Welding Industry Trends to Look for in 2025
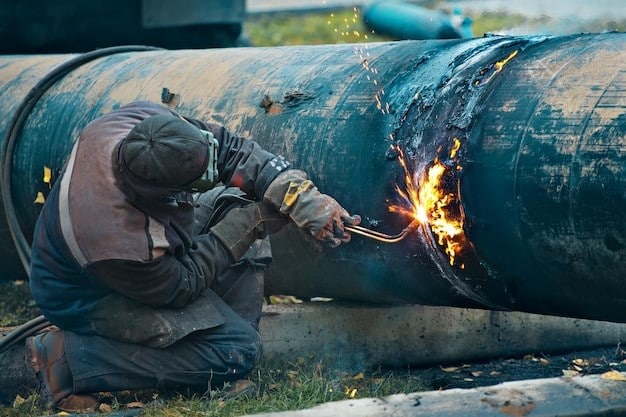
The welding industry is entering a phase of rapid transformation driven by technological advancements and market demands. Manufacturers focus on innovation to enhance the efficiency, accuracy, and sustainability of welding processes.
Emerging trends such as robotics, IoT integration, and eco-friendly methods are reshaping the industry, offering solutions to common challenges. These trends are essential for industries aiming to maintain competitiveness in a dynamic global market.
This article examines key developments expected to dominate the welding sector in 2025. By staying informed about these trends, businesses can align their strategies with future demands, ensuring long-term success and operational excellence.
Advanced Automation and Robotics
AI-Driven Welding Systems
AI-powered welding systems are revolutionizing the industry by improving precision and efficiency. These systems analyze large datasets to optimize weld patterns, reduce errors, and adapt to various materials. Automating critical decision-making processes helps businesses save time and resources while maintaining consistent quality. AI systems are particularly valuable in high-volume production where accuracy is critical.
Collaborative Robots (Cobots)
Cobots are designed to work alongside human operators, enhancing productivity and safety in welding applications. They assist with repetitive tasks, such as material handling and positioning, while ensuring consistent weld quality.
Cobots are cost-effective and easy to program, making them suitable for small and medium-sized enterprises. Their ability to complement human skills allows businesses to maximize workforce efficiency.
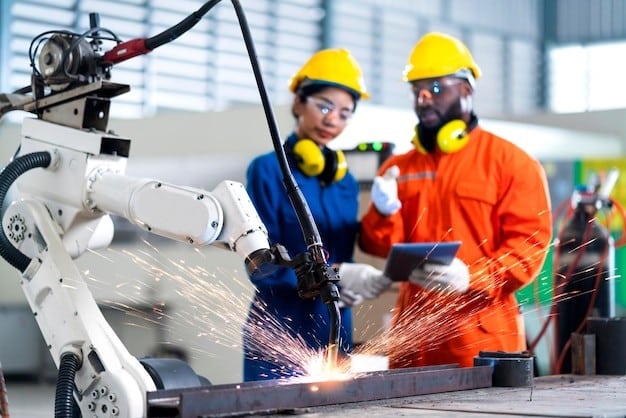
Autonomous Quality Control
Autonomous quality control systems integrate sensors and machine learning to inspect welds in real-time. These systems detect defects, measure accuracy, and provide actionable insights without human intervention. Identifying issues early helps reduce waste and rework, ensuring better use of materials. Automated inspection is particularly beneficial in industries requiring high reliability, such as aerospace and automotive manufacturing.
Sustainable and Eco-Friendly Welding
Low-Emission Welding Techniques
Low-emission welding techniques are becoming essential for reducing environmental impact in industrial processes. Laser welding and cold metal transfer generate less smoke and harmful gases than traditional techniques.
These advancements improve workplace safety and help businesses comply with stricter environmental regulations. Adopting these practices demonstrates a commitment to sustainability, which is increasingly important for long-term success.
Recyclable and Green Materials
The use of recyclable and eco-friendly materials is gaining momentum in welding applications. Manufacturers are focusing on developing consumables that can be reused or recycled without compromising quality.
This shift reduces waste, conserves resources, and lowers overall business costs. Green materials also align with the growing demand for sustainable practices across industries, fostering stronger relationships with environmentally conscious clients.
Energy-Efficient Equipment
Energy-efficient welding equipment from welding machine suppliers helps reduce power consumption while maintaining productivity. Technologies such as inverter-based welding machines and advanced thermal management systems enable businesses to achieve higher output with less energy.
These innovations lower operating costs and minimize carbon footprints, making them ideal for eco-conscious companies. Investing in energy-efficient tools supports both profitability and sustainability goals in industrial operations.
3D Printing and Welding Synergy
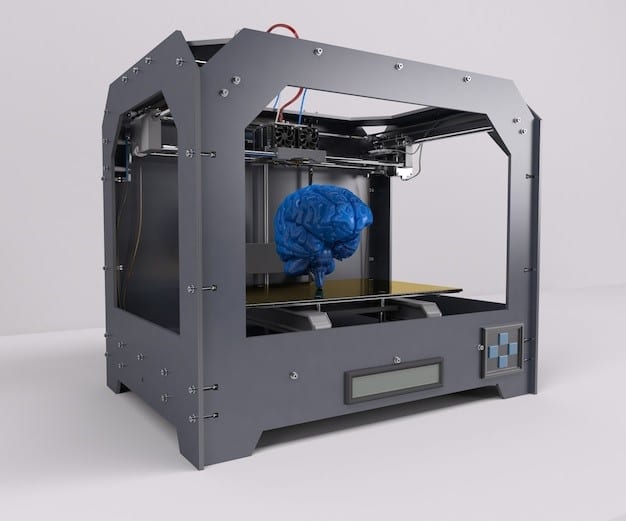
Hybrid Manufacturing Processes
Combining 3D printing with welding has created hybrid manufacturing processes that enhance efficiency and flexibility. This approach integrates additive manufacturing to create base structures and welding to add strength or finishing details.
Hybrid methods are especially useful for producing complex parts with precise geometries while ensuring structural durability. These processes save material and time, making them a valuable solution for industries like aerospace and automotive.
Rapid Prototyping
3D printing and welding enable rapid prototyping, allowing businesses to develop and test product designs faster. Additive manufacturing builds prototypes quickly, while welding ensures they meet functional and structural requirements.
This combination shortens development cycles, reducing the time it takes to bring products to market. Companies benefit from identifying design flaws early, minimizing the costs of redesigns and adjustments.
On-Demand Production
On-demand production supported by 3D printing and welding allows businesses to meet fluctuating demand without excess inventory. Additive manufacturing creates parts as needed, while welding enhances their performance or adapts them for specific applications.
This approach reduces storage costs and ensures resources are utilized efficiently. On-demand production also supports customized manufacturing, meeting unique client needs more precisely.
Integration of IoT and Data Analytics
Real-Time Monitoring
The integration of IoT in welding enables real-time monitoring of processes and equipment performance. Sensors in welding machines collect temperature, pressure, and arc stability data.
This information is transmitted instantly to centralized systems, allowing operators to identify and address issues as they arise. Real-time monitoring reduces downtime and enhances overall efficiency, ensuring consistent quality in production workflows.
Data-Driven Insights
Data analytics transforms the information IoT devices gather into actionable insights for improving welding operations. Businesses can optimize machine settings, predict maintenance needs, and minimize material waste by analyzing trends and patterns.
Data-driven approaches also help identify bottlenecks in production, enabling informed decisions to streamline processes. These insights lead to better resource management and improved cost-efficiency across operations.
IoT and data analytics create smarter welding systems capable of self-adjusting to maintain quality. This integration supports predictive maintenance, reducing the risk of unexpected equipment failures.
Businesses leveraging these technologies can achieve higher productivity while maintaining the precision required in demanding industries. By adopting IoT and data analytics, companies position themselves for long-term competitiveness in a rapidly evolving market.
Emerging Welding Industry Trends in 2025
Trend | Description | Benefit |
Advanced Automation | AI-driven systems, collaborative robots (cobots), and autonomous quality control. | Increases efficiency and precision. |
Sustainability | Low-emission welding, recyclable materials, and energy-efficient equipment. | Reduces environmental impact and costs. |
3D Printing Integration | Hybrid manufacturing processes, rapid prototyping, and on-demand production. | Enables faster production and customization. |
IoT and Data Analytics | Real-time monitoring and actionable insights to optimize operations. | Improves productivity and minimizes downtime. |
Safety Innovations | Advanced PPE, ergonomic tools, and automated safety systems. | Ensures worker safety and compliance. |
Workforce Training with VR/AR | VR and AR-based tools for hands-on, immersive training experiences. | Enhances skill development and learning speed. |
Lightweight Welding Equipment | Development of compact, portable welding tools for various industries. | Boosts mobility and ease of use. |
Modular Welding Systems | Flexible systems allowing customization and scalability for specific applications. | Supports diverse industry needs. |
Enhanced Workforce Training and Development
Personalized Learning
- Tailored Training Programs: Personalized learning approaches customize training modules to meet workers’ needs. Employees gain skills relevant to their roles, improving their efficiency and confidence.
- Adaptive Learning Systems: These systems use data to assess individual progress and adjust training material accordingly. Workers advance at their own pace, ensuring better understanding and retention.
- Focus on Skill Gaps: Training programs identify and address specific skill gaps, helping workers enhance their expertise. This targeted approach minimizes training time and maximizes productivity.
- Continuous Skill Development: Personalized learning encourages ongoing development, keeping workers updated on the latest technologies and practices in welding.
VR and AR Training
- Simulated Training Environments: Virtual reality (VR) creates realistic welding simulations for safe and hands-on training. Workers practice techniques without risking equipment or materials.
- Enhanced Visualization: Augmented reality (AR) overlays digital guides onto physical tools, helping workers easily understand complex tasks. This boosts precision and reduces errors.
- Cost-Effective Training: VR and AR reduce the need for physical materials, cutting training costs while maintaining quality. Companies benefit from scalable and efficient training solutions.
- Real-Time Feedback: AR-enabled devices provide instant feedback on worker performance, allowing immediate corrections and improved skills. This enhances learning outcomes and builds worker confidence.
Safety Innovations
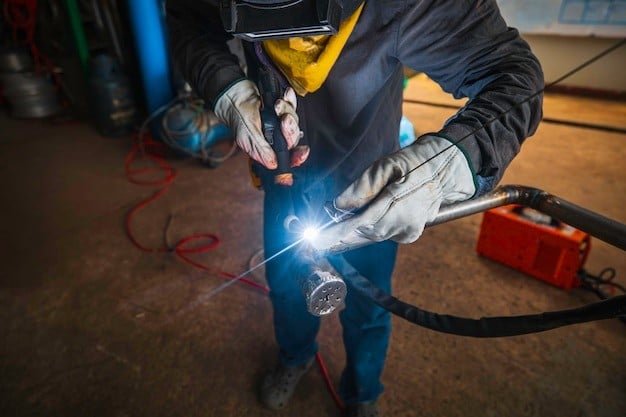
Advanced PPE for Welders
Personal protective equipment (PPE) is evolving to provide better protection and comfort for welders. Modern welding helmets come with auto-darkening filters and lightweight designs, reducing strain during long work hours.
High-performance welding gloves offer enhanced grip and heat resistance, minimizing hand injuries. Fire-resistant clothing with improved breathability ensures safety without compromising comfort. These advancements in PPE help reduce accidents and promote a safer working environment.
Ergonomic Tools
Ergonomic welding tools are designed to minimize physical strain and improve worker efficiency. Adjustable welding torches and lightweight equipment reduce fatigue, enabling welders to maintain precision during extended tasks.
Tools with anti-vibration handles enhance comfort and decrease the risk of repetitive strain injuries. Ergonomics improves worker safety and leads to higher productivity and job satisfaction.
Automated Safety Systems
Automated safety systems are becoming integral to welding operations, reducing the reliance on manual monitoring. Features like arc sensors and thermal cutoff mechanisms detect anomalies and shut down equipment to prevent accidents.
Some systems include real-time alerts that notify operators of potential hazards. These technologies reduce risks and create a safer workspace, especially in high-pressure environments.
Safety Sensors in Workspaces
Safety sensors are a growing trend, actively monitoring work environments for hazards. These sensors detect gas leaks, temperature changes, and harmful emissions, providing real-time alerts to operators.
Systems integrated with IoT ensure immediate responses to potential risks, reducing accidents in complex welding setups. This proactive approach enhances workplace safety significantly.
Fire Suppression Systems
Welding environments often involve flammable materials, making fire suppression systems critical. Innovations such as automated fire extinguishing systems detect and extinguish sparks instantly, preventing larger incidents.
Portable suppression units are also gaining popularity for their efficiency in handling localized hazards. These systems ensure a safer workspace while minimizing downtime.
YesWelder: Your Professional Welding Machine Partner
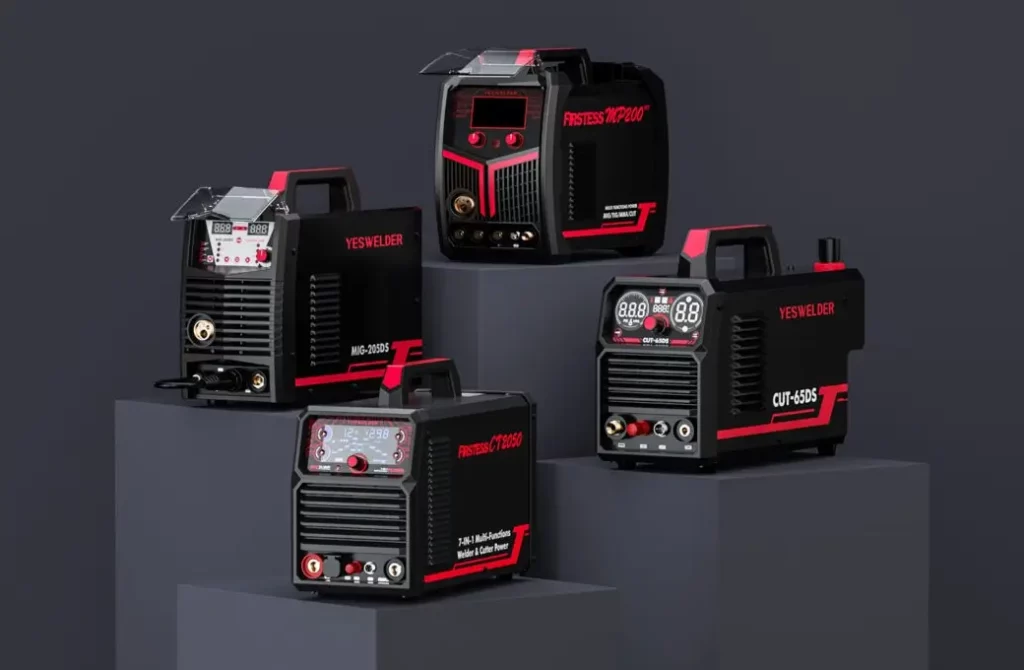
The welding industry rapidly adopts trends like automation, eco-friendly methods, and advanced safety systems. These developments highlight the growing demand for reliable, innovative equipment to meet evolving industry needs. Businesses seek partners who can provide high-quality solutions that align with these trends.
YesWelder stands out as a trusted supplier for wholesale buyers and distributors. Known for producing durable and efficient welding machines, the company offers many products, including multi-function welders, helmets, and accessories. YesWelder’s commitment to cost-effectiveness and quality ensures its equipment meets the standards of modern industrial applications.
With dedicated support, flexible wholesale options, and a focus on customer satisfaction, YesWelder is an ideal partner for businesses aiming to enhance their welding capabilities.
Features and Benefits of YesWelder Equipment
Feature | Benefit |
Durable Welding Machines | Long-lasting equipment suitable for industrial applications. |
Multi-Function Capabilities | Supports diverse welding needs, including MIG, TIG, and plasma cutting. |
Advanced Safety Features | Ensures user protection with reliable tools and systems. |
Cost-Effective Wholesale Options | Affordable solutions for bulk buyers and distributors. |
Dedicated Customer Support | Ensures smooth purchasing and after-sales service. |
FAQs
What are the top welding industry trends in 2025?
Key trends include automation and robotics, eco-friendly welding methods, 3D printing integration, IoT and data analytics, and advanced safety innovations.
How is automation impacting the welding industry?
Automation improves efficiency and precision through AI-driven systems, collaborative robots (cobots), and autonomous quality control.
What role does IoT play in welding?
IoT enables real-time monitoring and data-driven insights, enhancing process optimization, predictive maintenance, and productivity.
How can businesses benefit from safety innovations in welding?
Advanced PPE, ergonomic tools, and automated safety systems reduce workplace hazards, improve worker efficiency, and ensure compliance with safety standards.