Welding positions are critical to achieving high-quality welds that meet industry standards and ensure structural integrity. For welding plates, pipes, or fillet joints, understanding the various positions and their applications is essential for welders at all skill levels. This guide explores the types of welding positions, their techniques, challenges, and real-world uses, aligned with standards like AWS D1.1 and ASME Section IX.
What Is Welding Positions?
Welding positions refer to the standardized orientations of the weld joint and the welder’s approach, as defined by codes such as the American Welding Society (AWS) and the American Society of Mechanical Engineers (ASME).
These positions ensure consistency in weld quality, safety, and compliance with engineering specifications. Welding positions are categorized based on the workpiece (plate, pipe, or fillet) and the orientation (flat, horizontal, vertical, or overhead).
Mastering these positions is key to passing certification tests and performing welds in industries like construction, oil and gas, and aerospace.
Welding Position Classifications
Welding positions are designated using a numbering system (e.g., 1G, 2F) established by AWS and ASME. The number indicates the position, and the letter (G for groove, F for fillet) specifies the weld type. Positions are divided into:
- Plate Welding: Groove welds on flat plates, typically used in structural applications.
- Pipe Welding: Groove welds on cylindrical pipes, common in pipelines and pressure vessels.
- Fillet Welding: Welds on tee, lap, or corner joints, used in fabrication and construction.
Positions are further classified as test positions (e.g., 6G for certifications) or production positions (used in actual projects). Understanding these classifications helps welders select the right techniques and equipment.
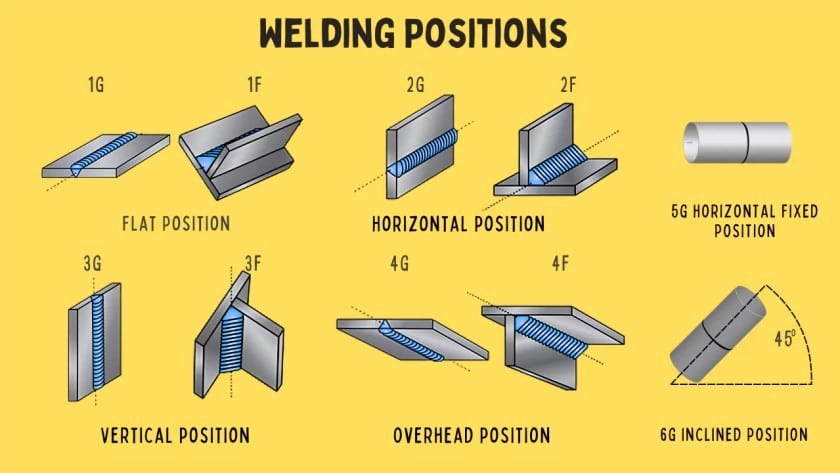
Plate Welding Positions
Plate welding positions are the foundation of structural welding, used in applications like bridges, buildings, and heavy machinery. Below are the four primary plate welding positions.
1G (Flat)
The weld is performed on the top surface of a horizontal plate, with the weld pool flowing naturally due to gravity. It use stringer beads for narrow welds or weave beads for wider coverage. Maintain a 10–15° drag angle for the electrode.
- Equipment: Suitable for MIG (fast), TIG (precise), or stick welding (versatile).
- Challenges: Controlling the weld pool on thick plates to avoid excessive penetration.
- Applications: Structural steel fabrication, shipbuilding, and manufacturing.
2G (Horizontal)
This weld is performed on a vertical plate surface, with the weld bead running horizontally.
- Techniques: Employ a side-to-side weave to fill the joint evenly. Maintain consistent travel speed to avoid sagging.
- Equipment: Stick welders for field applications (learn more about field welding) or MIG for shop environments.
- Challenges: Preventing undercut on the top edge or slag inclusion in the weld.
- Applications: Bridge construction, heavy equipment frames, and storage tanks.
3G (Vertical)
The weld is performed on a vertical plate, with the bead running vertically (up or down).
- Techniques: Use vertical-up weaving for deeper penetration on thick materials or vertical-down for faster welds on thin plates. Keep a tight arc to control the pool.
- Equipment: TIG for precision welds or stick for rugged fieldwork.
- Challenges: Gravity pulls the weld pool downward, increasing the risk of sagging or lack of fusion.
- Applications: High-rise buildings, storage tanks, and pressure vessels.
4G (Overhead)
The weld is performed on the underside of a horizontal plate, with the welder working upward.
- Techniques: Use a short arc length and small weave to prevent molten metal from dripping. Pause briefly to let the pool solidify.
- Equipment: Stick or TIG welding machines for better control in this challenging position.
- Challenges: Molten metal dripping (spatter) and welder fatigue due to awkward positioning.
- Applications: Pipeline repairs, industrial frameworks, and shipbuilding.
Pipe Welding Positions
Pipe welding positions are used in industries like oil and gas, power generation, and petrochemicals, where cylindrical joints require precise welds. These positions are more complex due to the curved surface and fixed pipe orientations.
1G (Rotated Pipe, Flat)
The pipe is rotated horizontally, allowing the welder to weld in the flat position.
- Techniques: Use consistent torch movement synchronized with pipe rotation. Roll welding ensures uniform beads.
- Equipment: MIG for high-speed production or TIG for high-quality welds.
- Challenges: Maintaining bead uniformity during continuous rotation.
- Applications: Pipeline fabrication, oil refineries, and gas distribution systems.
2G (Vertical Pipe, Horizontal Weld)
The pipe is fixed vertically, and the weld is performed horizontally around the pipe’s circumference.
- Techniques: Use weave or stringer beads with a 5–10° drag angle. Adjust torch position to account for the pipe’s curvature.
- Equipment: Stick for field welding or TIG for precision.
- Challenges: Controlling the weld pool on a curved surface to avoid sagging or undercut.
- Applications: Refinery piping, structural supports, and chemical plants.
5G (Horizontal Pipe, Fixed)
The pipe is fixed horizontally, requiring the welder to work in multiple positions (flat, vertical, overhead) around the pipe.
- Techniques: Start with a vertical-up root pass for penetration, followed by multi-pass fill and cap welds. Adjust torch angle for each position.
- Equipment: TIG for the root pass, stick or MIG for fill and cap.
- Challenges: Transitioning between positions while maintaining bead consistency; gravity affects the weld pool.
- Applications: Cross-country pipelines, power plant piping, and offshore platforms.
6G (Pipe at 45° Angle, Fixed)
The pipe is fixed at a 45° angle, requiring the welder to weld in all positions (flat, vertical, overhead).
- Techniques: Use multi-pass welding with precise torch control. Start with a TIG root pass, followed by stick or MIG fill passes.
- Equipment: TIG for the root, stick or MIG for subsequent passes.
- Challenges: High skill required to manage complex positioning and weld pool control across all angles.
- Applications: Offshore oil platforms, high-pressure piping, and boiler systems.
6GR (Restricted 6G)
A 6G position with a restriction ring or obstruction, simulating limited-access conditions.
- Techniques: Use specialized torch manipulation to weld around the restriction. TIG is preferred for precision in tight spaces.
- Equipment: TIG for root and fill passes due to restricted access.
- Challenges: Extreme skill and dexterity needed to navigate obstructions while maintaining weld quality.
- Applications: Nuclear power plant piping, aerospace components, and high-stakes pressure vessels.
Fillet Welding Positions
Fillet welds are used for tee, lap, and corner joints, common in fabrication and structural applications. These positions are designated with an “F” (e.g., 1F).
1F (Flat Fillet)
The fillet weld is performed in the flat position, typically on a tee or lap joint.
- Techniques: Use a drag technique with a 45° electrode angle to ensure equal leg sizes. Maintain steady travel speed.
- Equipment: MIG for high-speed welding or stick for versatility.
- Challenges: Achieving symmetrical fillet legs and avoiding excessive buildup.
- Applications: Automotive frames, furniture fabrication, and light structural work.
2F (Horizontal Fillet)
The fillet weld is performed on a horizontal joint, with one surface vertical.
- Techniques: Use a weave technique for wider beads. Position the torch to prevent undercut on the vertical surface.
- Equipment: MIG for shop welding or stick for field applications.
- Challenges: Avoiding undercut or lack of fusion on the vertical plate.
- Applications: Construction beams, machinery bases, and storage racks.
3F (Vertical Fillet)
The fillet weld is performed on a vertical joint, with the bead running vertically.
- Techniques: Use vertical-up weaving for better penetration. Control travel speed to prevent sagging.
- Equipment: TIG for precision or stick for rugged environments.
- Challenges: Weld pool sagging due to gravity and welder fatigue in prolonged vertical welding.
- Applications: Storage tanks, structural columns, and heavy equipment.
4F (Overhead Fillet)
The fillet weld is performed in the overhead position, with the welder working upward.
- Techniques: Use a short arc and small weave to prevent drips. Pause to let the weld pool solidify.
- Equipment: Stick or TIG for better control in this difficult position.
- Challenges: Molten metal dripping and awkward welder positioning.
- Applications: Shipbuilding, bridge repairs, and industrial maintenance.
Welding Standards and Certifications
Welding positions are governed by industry standards like AWS D1.1 (structural welding) and ASME Section IX (pressure vessels and piping). These standards define position requirements for welder performance qualification tests (WPQTs).
For example:
- 3G and 4G: Common for structural welding certifications.
- 6G: The gold standard for pipe welding, qualifying welders for all positions.
- 6GR: Used for specialized applications requiring restricted-access skills.
There are types of welding certifications. Certifications involve welding test coupons in specific positions, inspected via visual, destructive, or non-destructive testing (e.g., X-ray). Welders must demonstrate proficiency in techniques, joint preparation, and code compliance. Obtaining certifications enhances employability in industries like oil and gas, aerospace, and construction.
Practical Techniques and Equipment
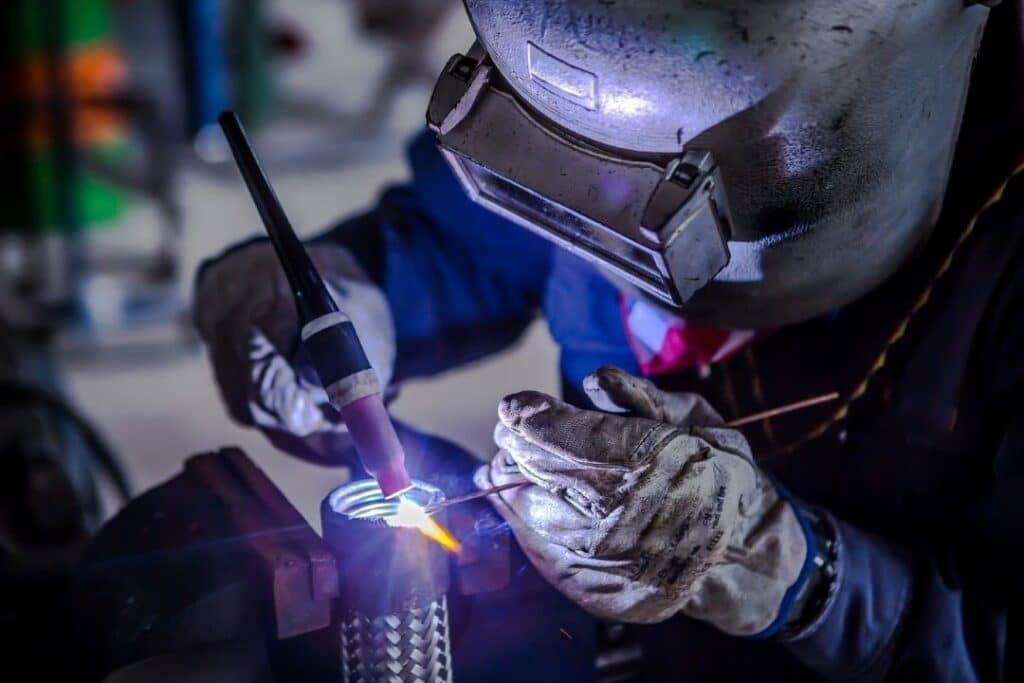
Techniques
- Electrode Angles: Use a 10–15° drag angle for flat and horizontal welds, 5–10° for vertical and overhead to control the pool.
- Travel Speed: Maintain steady speed to avoid defects like porosity or lack of fusion.
- Bead Types: Stringer beads for narrow welds; weave beads for wider joints or vertical welding.
- Multi-Pass Welding: Essential for pipe (e.g., 5G, 6G) and thick plates, with a root pass (TIG) followed by fill and cap passes (stick or MIG).
Equipment
Welding Processes:
- MIG: Ideal for flat and horizontal positions due to speed and ease.
- TIG: Preferred for pipe welding (root passes) and precision work.
- Stick: Versatile for field welding, especially in vertical and overhead positions.
Tools: Use positioners for pipe rotation (1G), clamps for fixed pipes (5G, 6G), and jigs for fillet welds.
Safety Gear: Auto-darkening helmets, flame-resistant gloves, and jackets are critical, especially for overhead and restricted positions.
Real-World Applications
Welding positions are applied across diverse industries:
- Flat (1G, 1F): Automotive assembly lines, furniture manufacturing, and steel fabrication shops.
- Horizontal (2G, 2F): Bridge construction, heavy machinery frames, and refinery piping.
- Vertical (3G, 3F): High-rise building frameworks, storage tank construction, and ship hulls.
- Overhead (4G, 4F): Bridge maintenance, shipbuilding, and industrial plant repairs.
- Pipe (5G, 6G): Cross-country oil pipelines, power plant boilers, and offshore platforms.
- 6GR: Nuclear reactor piping, aerospace fuel systems, and high-pressure vessels.
Case Study: In offshore oil platform construction, 6G welding is used to join high-pressure piping. Welders must navigate fixed pipes at 45° angles, often in confined spaces, requiring TIG for precision and 6G certifications to meet ASME standards.
We’ve collected all these types of welding positions for you.
Position | Type | Orientation | Applications | Difficulty |
---|---|---|---|---|
1G | Plate | Flat | Structural steel, shipbuilding | Low |
2G | Plate | Horizontal | Bridges, heavy machinery | Medium |
3G | Plate | Vertical | High-rise buildings, tanks | High |
4G | Plate | Overhead | Pipeline repairs, frameworks | High |
1G | Pipe | Rotated, Flat | Pipelines, refineries | Low |
2G | Pipe | Vertical, Horizontal | Refinery piping, supports | Medium |
5G | Pipe | Horizontal, Fixed | Pipelines, power plants | High |
6G | Pipe | 45° Fixed | Offshore platforms, boilers | Very High |
6GR | Pipe | 6G with Restriction | Nuclear piping, aerospace | Extreme |
1F | Fillet | Flat | Automotive, fabrication | Low |
2F | Fillet | Horizontal | Construction, machinery bases | Medium |
3F | Fillet | Vertical | Tanks, structural beams | High |
4F | Fillet | Overhead | Shipbuilding, bridge repairs | High |
Final Thoughts
Understanding welding positions is essential for producing high-quality welds that meet industry standards. From flat plate welding (1G) to complex pipe welding (6G, 6GR), each position requires specific techniques, equipment, and skills.
Mastering these positions, welders can tackle diverse projects, from automotive fabrication to nuclear piping. Practice these techniques, pursue certifications (e.g., AWS 3G, 6G), and explore resources like AWS and welding training programs to advance your career.
FAQs
What is the hardest welding position?
The 6G and 6GR positions are the most challenging due to the fixed 45° pipe angle (6G) and restricted access (6GR), requiring all-position welding and advanced skill.
How do I choose the right welding process for a position?
MIG is best for flat and horizontal positions due to speed. TIG is ideal for pipe welding (root passes) and precision. Stick is versatile for vertical, overhead, and field work.
What certifications do I need for pipe welding?
A 6G certification (AWS or ASME) qualifies you for all pipe and plate positions, while 5G is common for pipeline work.
How can I practice overhead welding safely?
Use a short arc, wear flame-resistant gear, and practice on scrap metal in a controlled environment to master pool control and avoid spatter.