In this article, you will learn:
- The technology and history of welding
- Detailed applications across large industries
- Popular welding technique comparison
- Pros and cons of various welding methods
- Real-world case studies
At its heart, welding is about joining things—usually metals, sometimes plastics—by melting their edges and blending them together with heat, pressure, or both.
The result? A bond that’s often tougher than the materials it connects. It’s the glue that holds our engineered world together.
Tensile strength and resilience from welding make it indispensable to the fabrication of complex structures and manufacturing of high-performance products.
Whether constructing skyscrapers, developing airplanes, or manufacturing car parts, welding ensures essential components maintain stability under stress and extreme conditions.
This article is your all-in-one guide. Whether you’re a pro, a student, or just curious, you’ll find insights here that make welding’s role crystal clear.
A Quick Look Back at Welding’s History
The history of welding goes back a long time. Humans in the early days used forge welding—melting and pounding metals together—to create tools and weapons.
But then, with the advent of arc welding in the 20th century, things really took off. Now we could build larger, more powerful, and more complicated things.
Modern welding is characterized by robotics, robots, and innovative processes like laser welding and friction stir welding. These have all brought with them:
- Increased Precision: Automated systems cut the chances of human mistakes, creating even, high-standard welds.
- Efficiency: Robotic welders improve productivity speeds without cutting safety corners in hazardous environments.
- Environmental Benefits: Innovative ecologically friendly shielding gases and consumables reduce emissions and improve work environments.
Sustained advancements in welding technology have been leading forces in shaping sectors. Welding not only forms the backbone for the construction of gigantic-scale infrastructures but is also spearheading innovation in fields like aerospace, where minimizing weight and material requirements are critical issues.
Welding is a highly flexible process applied across a wide variety of industries. Here, we discuss its input to some of the key industries.
Read more in this article: The Fascinating Journey of Welding History.
Welding in Aerospace Industry
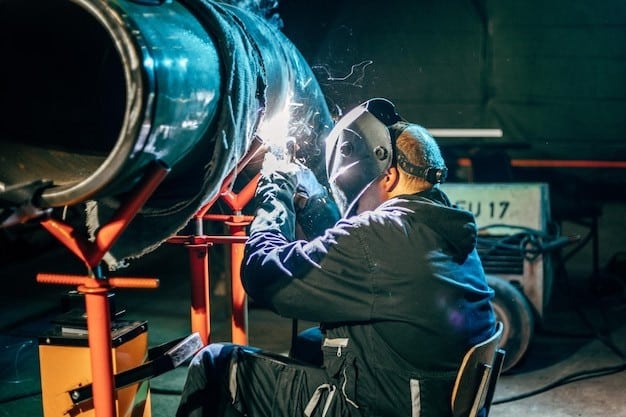
Welding plays a critical role in the production of aircraft components such as fuselages, wings, and engine parts. High-quality welds enable the structure to withstand extreme stresses, temperature fluctuations, and pressure fluctuations during flight.
Advanced Techniques (TIG vs. MIG)
TIG welding offers unparalleled precision to weld thin, high-strength materials such as titanium and aluminum, essential for aircraft frames to be lightweight yet strong.
A MIG welding machine provides higher production rates for heavy materials and large parts, enabling manufacturing to be more productive.
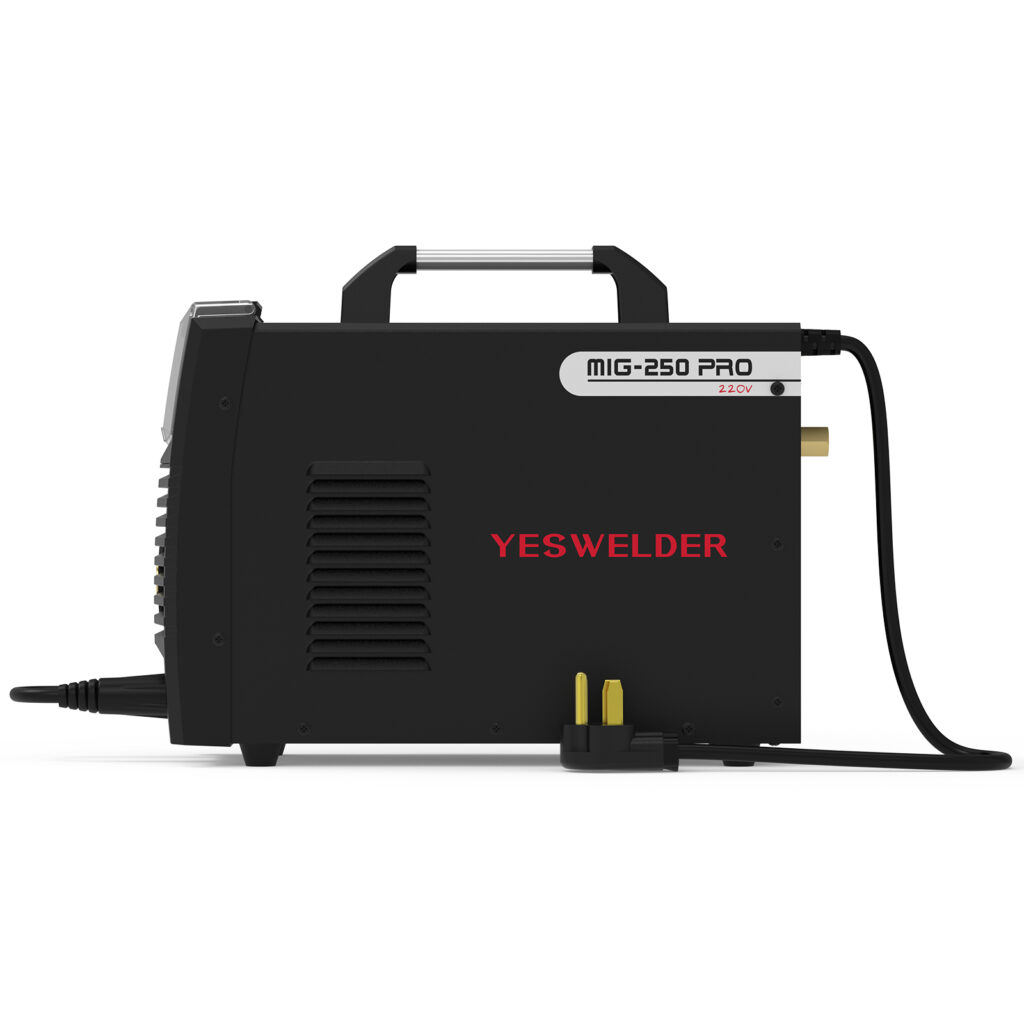
Welding in Construction
Infrastructure Projects
Welding is critical in constructing bridges, tunnels, highways, and pipelines. Steel columns and beams are welded together with solid, reliable welds that support the structures capable of resisting environmental loads and bearing forces.
Building Construction
In skyscrapers, residential buildings, and commercial complexes, welding creates the steel frames that serve as the skeleton of the building. Welding is also utilized in the installation of metal roofing, staircases, and other fundamental architectural elements.
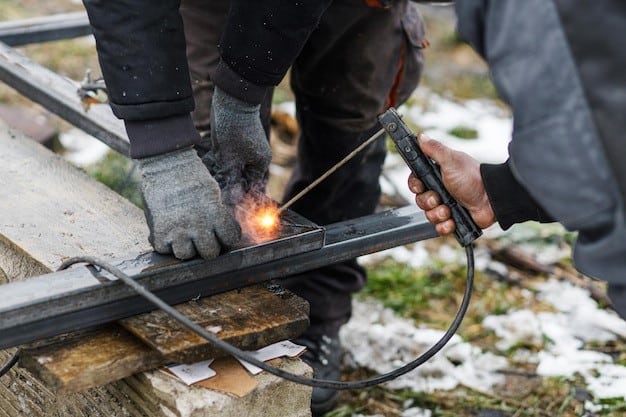
Industrial Facilities
Power plants, factories, and refineries employ heavy-duty metal structures to house heavy machinery and equipment. Welding ensures that pressure vessels, storage tanks, and other industrial equipment meet stringent safety protocols.
Welding in Oil & Gas Industry
Pipeline Welding
Welding is critical to construct pipelines for the conveyance of oil and gas fluids. The operation must form high-integrity, free-from-leakage joints for resistance to high pressure and extreme environmental conditions.
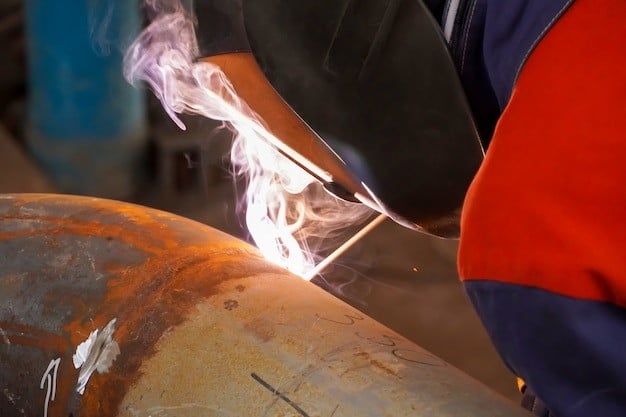
Offshore and Harsh Environment Welding
Stick Welding (SMAW) and Flux-Cored Arc Welding (FCAW) are excellent welding processes for application in offshore platforms and remote pipelines because of their ability to operate in windy, corrosive environments. These processes are reliable and low-cost in harsh environments.
Welding in Automotive Industry
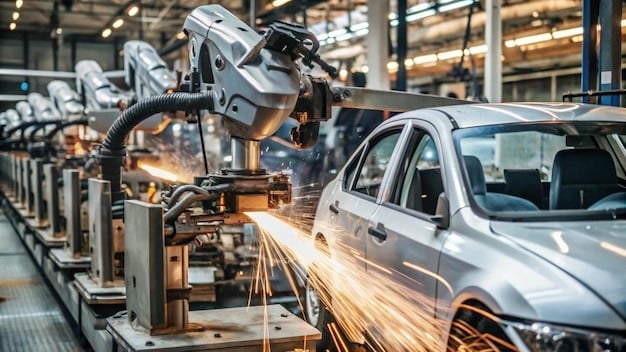
Vehicle Assembly
Welding in vehicle manufacturing unites car bodies, chassis, and exhaust systems. MIG welding offers high rates of production, while a TIG welding machine is used in precision applications of performance parts.
Repair and Fabrication
Specialty repair, modification, and fabrication work relies on welding to restore or enhance the vehicle’s performance. Enhancing a chassis or repairing a broken component, high-strength welds ensure safety and durability.
Welding in Shipbuilding and Maritime Applications
Hull Repair and Fabrication
Ship building demands tough, watertight welds to fabricate and repair the hull. Stick welding machines are common in the business because they’re versatile and have the ability to create durable joints even in open spaces during windy conditions.
Corrosion Control
Seas subject ships to corrosive sea water. Welding processes should be capable of accounting for these environments using corrosion-resistant materials and processes that minimize oxidation.
Welding in Energy and Nuclear Applications
Power Plants and Renewable Energy Infrastructure
Welding is employed in building boilers, turbines, and wind farm structures. Its application in making power production plants long-lasting and safe is most important.
Nuclear Facilities
For nuclear power facilities and their auxiliary structures, welding has to provide high-integrity, corrosion-free joints for the sake of safety under hostile environments and regulatory compliance.
Specialty and Creative Applications
Art and Sculpture
The accuracy of TIG welding renders it very attractive to artists and sculptors. It allows them to create intricate designs and fine details in sculptures and metal artworks without compromising the material’s integrity.
Medical and Food Industry Equipment
Clean welding is a necessity in medical equipment and stainless steel machinery found in the food and beverage industry. Clean, smooth welds allow for the ease of sterilization of surfaces and free them from contaminants.
Welding Techniques and Their Suitability
Welding Techniques | Advantages | Disadvantages |
Stick Welding (SMAW) | Versatile, portable, and cost-effective; for outdoor work and heavy maintenance. | Produces more spatter, frequent tungsten welding electrode needs; slower. |
MIG Welding (GMAW) | Fast, efficient, and suitable for a wide range of metals and thicknesses; minimal cleanup. | Requires shielding gas and careful control; not for high-precision tasks. |
TIG Welding (GTAW) | Produces high-quality, clean welds with excellent precision; for thin materials and complex geometries. | Slower process requiring high skill levels; more expensive. |
Flux-Cored Arc Welding (FCAW) & Submerged Arc Welding (SAW) | Ideal for heavy-duty, large-scale projects; welding thick materials. | Specialized equipment and less suitable for precision work. |
In addition to the welding techniques above, new methods such as laser welding and friction stir welding are revolutionizing the industry, offering benefits like minimal heat distortion and high-speed operation.
Comparative Analysis: Pros and Cons Across Techniques
All welding processes call for strict adherence to safety protocols. However, processes like stick welding, which produce more sparks and fumes, need additional protection and top-notch ventilation systems.
Quality and Accuracy
- TIG Welding: Unparalleled accuracy and absence of spatter make it ideal for aesthetic and structurally critical applications.
- MIG Welding: Provides a good balance between quality and speed, making it ideal for production-level work.
- Stick Welding: While strong and versatile, it can produce rougher welds that may require more finishing.
Cost and Productivity
- MIG Welding: High deposition rates save labor costs, making it ideal for high-level production.
- Stick Welding: Low equipment cost and portability provide a cost-effective alternative for many applications.
- TIG Welding: Higher cost because of equipment and labor skill demands, but often justified by the quality of the weld.
Suitability for Special Environments
- Outdoor Applications: Stick welding and FCAW perform better in windy or unfavorable conditions.
- Indoor/Controlled Environments: MIG and TIG welding are more suitable because very controlled welding conditions are present.
Read more in related articles:
MIG vs TIG Welding: Understanding All the Fundamentals
Stick Welding vs. Other Welding Techniques
Case Studies and Industry Examples
Aerospace Success
Modern aircraft manufacturing relies on a mix of TIG and MIG welding for its most important components. For example, automated TIG systems have been implemented to ensure uniform weld quality on lightweight materials like titanium, thereby enhancing performance and safety.
Landmark Construction Projects
Skyscrapers and bridges, landmark constructions, use advanced welding techniques to keep their steel structures intact. Proper quality MIG and FCAW welding have been directly linked to the safety and longevity of these types of structures, indicating how crucial accuracy is when it comes to welding.
Oil & Gas Pipeline Innovations
Pipelines constructed using intense stick welding and FCAW processes have exhibited long-term durability in harsh, corrosive environments. Regular maintenance combined with stringent quality measures has prevented costly breakdowns and minimized environmental risks to a mere fraction.
Conclusion
Welding is a dynamic and critical process that drives modern industry. From aerospace to construction, automotive, oil & gas, and beyond, each welding process offers unique advantages for specific applications.
Advances in precision, efficiency, and environmental sustainability ensure that welding will continue to play a critical role in meeting the demands of a rapidly evolving technological world.
FAQ
What is welding and why is it important?
Welding is a metal joining process using heat and pressure to form strong, stable joints important to structural integrity and longevity in modern industry.
Which welding process is best for high-precision applications?
TIG welding is usually the most appropriate process for high-precision applications because it can produce clean, accurate welds with minimal spatter.
How do welding techniques differ across industries?
Different industries have appropriate welding processes suitable for them—to illustrate, aerospace requires light and precise welds (TIG welding), while oil & gas prefer robust joints created by Stick Welding or FCAW.
What safety measures should be done while welding?
Proper ventilation, protection gear (welding helmet, gloves, and uniforms), and adherence to safety protocols are essential to avert dangers due to sparks, fumes, and heat.
How to make sure the welding project meet industry standards?
Investment in quality equipment, regular training of your staff, and thorough inspections can ensure conformity with industry standards and enhance weld quality.