Ensuring an aircraft’s structural integrity and performance is a significant challenge in the aerospace industry. One critical aspect of this is the use of effective welding techniques. Welding in aerospace is essential for constructing and maintaining aircraft components, from the fuselage to the engine parts.
With advancements in welding technology, the industry can now achieve stronger, more reliable joints that withstand extreme conditions. This article explains the importance of welding in aerospace, exploring various techniques, applications, and the advantages and challenges faced. Understanding these aspects is vital for anyone interested in the aerospace sector.
Importance of Welding in Aerospace
Welding is crucial in aerospace because it creates strong, durable joints for aircraft safety and functionality. The aerospace sector demands high precision and reliability, and welding provides the means to achieve these standards. Properly executed welds ensure that aircraft components can withstand the stresses of flight, including extreme temperatures, pressure changes, and mechanical forces.
One significant application of welding in aerospace is constructing aircraft frames and structures. These parts must be lightweight yet strong, and welding allows for the precise joining of materials like aluminum and titanium, commonly used in aerospace manufacturing. With reliable welding techniques, the structural integrity of these components would be protected.
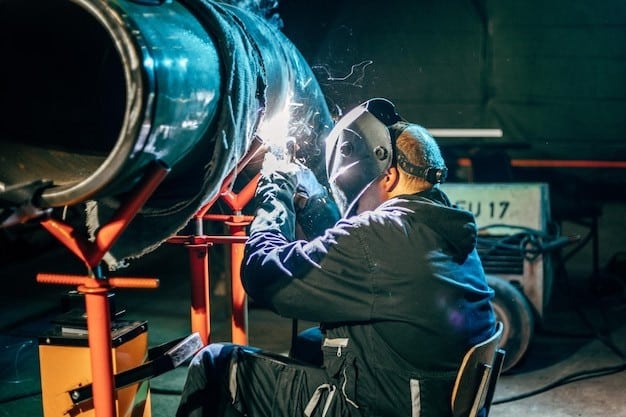
Welding also plays a vital role in fabricating engine components. These parts operate under intense heat and pressure, requiring joints to maintain strength and integrity. Advanced welding techniques ensure engine parts are robust and reliable, contributing to overall aircraft safety.
It is essential for aircraft repair and maintenance. Over time, aircraft components may develop cracks or other forms of damage. Welding allows for effective repairs, extending the lifespan of these components and ensuring that the aircraft remains safe and operational.
MIG vs. TIG Welding in Aerospace Industry
Welding is an indispensable process in the aerospace industry. It produces strong, reliable joints necessary for various aircraft components. Two primary welding techniques used in aerospace are TIG (Tungsten Inert Gas) welding and MIG (Metal Inert Gas) welding. Each method has its advantages, applications, and challenges.
TIG vs MIG Welding in the Aerospace Industry
Aspect | TIG Welding | MIG Welding |
Welding Process | Non-consumable tungsten electrode | Consumable wire electrode |
Electrode Type | Tungsten | Consumable wire |
Shielding Gas | Argon or Helium | Argon or Argon-CO2 mixture |
Material Suitability | Thin materials | Thicker materials |
Precision and Control | High precision and control | Less precision |
Weld Quality | High-quality, clean welds with minimal spatter | Good quality but more spatter |
Speed | Slower process | Faster process |
Ease of Use | Requires high skill level | Easier to learn and use |
Skill Requirement | High | Moderate |
Common Applications | Thin materials, complex geometries, high-performance alloys | Structural components, thicker materials, production efficiency |
TIG Welding in the Aerospace Industry
TIG welding is highly often in the aerospace industry for its precision and high-quality welds. This technique uses a non-consumable tungsten electrode to produce the weld. An inert gas, typically argon or helium, protects the welding area from atmospheric contamination.
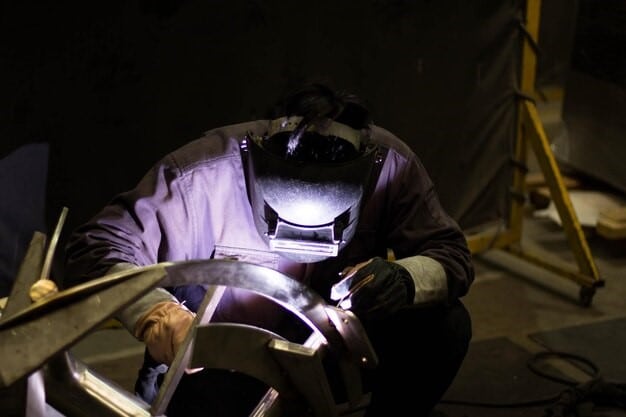
Advantages of TIG Welding
- Precision and Control: TIG welding offers excellent control over the welding process, making it ideal for welding thin materials and complex shapes. This precision is crucial in aerospace applications where exact specifications must be met.
- High-Quality Welds: The process produces clean, high-quality welds with minimal spatter. This is important for aerospace components that require smooth surfaces and strong joints.
- No Filler Material Required: In some cases, TIG welding machines can perform without adding filler material, relying instead on the fusion of the base metals. This can be beneficial for creating joints without altering the material properties.
Disadvantages of TIG Welding
- Slow Process: TIG welding is relatively slow compared to other welding methods. This can increase production time and costs, a significant consideration in the aerospace industry, where efficiency is crucial.
- Equipment Costs: The equipment for TIG welding, including the TIG welding machine, inert gas supply, and tungsten electrodes, can be expensive. This initial investment can be substantial.
TIG Welding Applications
- Complex Geometries: TIG welding suits components with complex shapes and geometries, such as turbine blades and engine parts. The ability to control the weld precisely ensures that these intricate parts meet strict aerospace standards.
- High-Performance Alloys: Aerospace components made from high-performance alloys like titanium and nickel-based alloys benefit from the clean and precise welds produced by TIG welding.
MIG Welding in the Aerospace Industry
MIG welding is another common welding technique in the aerospace industry. It uses a consumable wire electrode fed through the welding gun, and an inert gas, usually argon or a mixture of argon and carbon dioxide, shields the welding area from contamination.
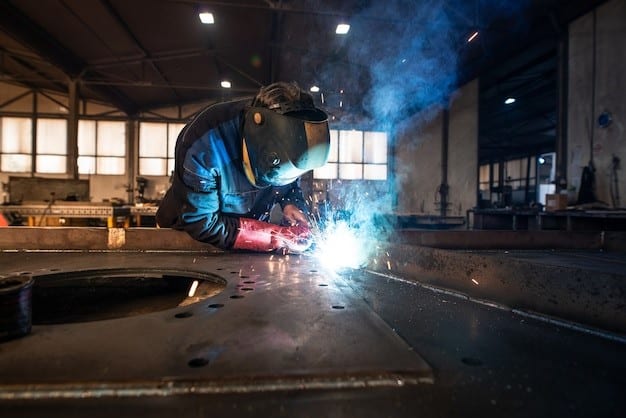
Advantages of MIG Welding
- Speed: MIG welding is faster than TIG welding, making it suitable for projects that require quick turnaround times. This speed can enhance productivity in aerospace manufacturing.
- Ease of Use: MIG welding is generally easier to learn and perform than TIG welding. This can reduce training costs and increase the availability of skilled welders.
- Versatility: A MIG welder can be used on various metals. It is particularly effective for welding thicker materials and is often used in aircraft structural components.
Disadvantages of MIG Welding
- Spatter: MIG welding tends to produce more spatter compared to TIG welding. This can result in additional cleaning and finishing work, increasing labor costs.
- Equipment Complexity: The equipment for MIG welding, including the wire feed mechanism and gas supply, can be complex and requires regular maintenance to ensure optimal performance.
MIG Welding Applications
- Structural Components: MIG welding is often used for larger structural components of aircraft, such as frames and support beams. The speed of the process makes it ideal for these extensive welds.
- Production Efficiency: For aerospace manufacturers focusing on production efficiency, MIG welding balances speed and quality, making it a preferred method for many applications.
Applications of Welding in Aerospace
Welding is crucial in aerospace manufacturing and maintenance, ensuring the structural integrity and reliability of aircraft components. Applications in aerospace include aircraft frames and structures, engine components, fuel and hydraulic systems, and repair and maintenance.
Aircraft Frames and Structures
Welding is essential in constructing aircraft frames and structures. These components must be lightweight yet strong to support the aircraft’s overall structure and withstand the stresses of flight. Techniques like TIG and MIG welding join materials such as aluminum and titanium, ensuring high strength-to-weight ratios. Proper welding ensures the aircraft can handle the dynamic forces encountered during operation without compromising safety.
Engine Components
Engine components are another critical area where welding is extensively used. These parts operate under extreme conditions, including high temperatures and pressures. Welding techniques create strong, reliable joints in components like turbine blades, combustion chambers, and exhaust systems. The precision and quality of the welds are paramount to ensuring the engine’s efficiency and longevity. Advanced welding methods help achieve the necessary durability and performance standards.
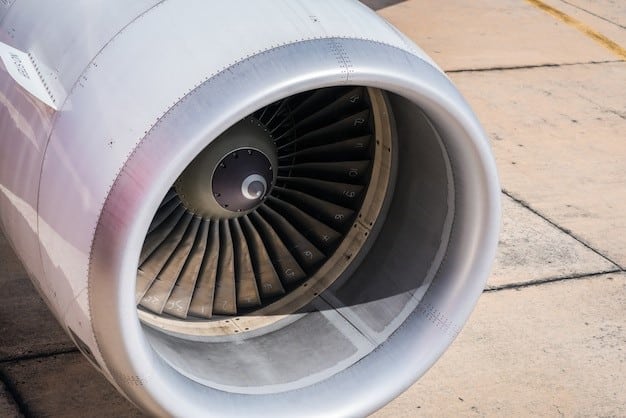
Fuel and Hydraulic Systems
Fuel and hydraulic systems are integral to an aircraft’s operation and require leak-proof and robust connections. Welding fabricates and assembles these systems, ensuring they can withstand the operational pressures and stresses. High-quality welds prevent leaks and failures, which is critical for maintaining the aircraft’s safety and efficiency. Materials used in these systems, such as stainless steel and aluminum, benefit from welding techniques that provide strong, corrosion-resistant joints.
Repair and Maintenance
Welding is also vital in aircraft repair and maintenance. Over time, components may develop cracks, wear, or other forms of damage. Welding allows for effective repairs, restoring the integrity of the affected parts. Techniques like TIG and MIG welding are employed to fix these issues, extending the service life of the components and ensuring the aircraft remains airworthy. Regular maintenance using welding helps prevent failures and maintains the safety and performance of the aircraft.
Advantages and Challenges of Welding in Aerospace
Welding in the aerospace industry offers numerous advantages but presents several challenges. Understanding these aspects is crucial for optimizing welding processes and ensuring the safety and reliability of aircraft components.
Advantages of Welding in Aerospace
1. Strong and Durable Joints: Welding creates strong and durable joints essential for aircraft structural integrity. These joints can withstand the high stresses and dynamic forces experienced during flight, ensuring safety and performance.
2. Weight Reduction: Advanced welding techniques allow for the use of lightweight materials like aluminum and titanium. By joining these materials efficiently, welding helps reduce the aircraft’s overall weight, improving fuel efficiency and performance.
3. Versatility: Welding is a versatile process used on various materials and components. This versatility is critical in aerospace, where different aircraft parts may require different materials and joining methods.
4. Precision: Modern welding techniques, such as TIG welding, offer high precision and control. This precision is necessary for manufacturing complex components and ensuring they meet stringent aerospace standards.
Challenges of Welding in Aerospace
1. High Skill Requirement: Welding in aerospace requires highly skilled welders. The precision and quality demanded by aerospace applications mean extensive training and experience are necessary, increasing labor costs.
2. Expensive Equipment: The equipment used for aerospace welding, including advanced welding machines and inert gas supplies, can be costly. This investment is necessary to achieve the high-quality welds required but adds to the overall manufacturing expenses.
3. Quality Control: Ensuring consistent quality in welding is challenging. Aerospace components must meet strict quality standards, and defects can have severe consequences. Rigorous inspection and testing are essential, adding to the complexity of the process.
4. Material Challenges: Aerospace materials like titanium and advanced composites can be difficult to weld. These materials require specific welding techniques and conditions, adding to the challenge of producing reliable joints.
5. Heat Management: Managing heat input during welding is crucial to prevent distortion or damage to thin sections and sensitive materials. Controlling heat is challenging but necessary to maintain the integrity of the components.
Final Words
Welding is integral to the aerospace industry, ensuring the durability and safety of aircraft. Advanced welding techniques produce reliable components essential for commercial and defense applications. As technology evolves, the role of welding in aerospace will continue to grow, addressing new challenges and opportunities. Understanding these processes is vital for anyone involved in aerospace manufacturing and maintenance.
FAQs
What types of welding are most commonly used in the aerospace industry?
The most commonly used welding techniques in the aerospace industry are TIG (Tungsten Inert Gas) and MIG (Metal Inert Gas) welding.
Why is welding important in aerospace manufacturing?
Welding is crucial in aerospace manufacturing because it creates strong, reliable joints for an aircraft’s structural integrity and performance.
How does welding contribute to the maintenance of aircraft?
Welding is vital for aircraft repair and maintenance. It effectively repairs cracks and other damages, extending the service life of components.
What are the challenges of welding aerospace materials?
Challenges of welding aerospace materials include managing high-skill requirements, ensuring consistent quality, dealing with expensive equipment, and addressing material-specific issues such as welding titanium and composites.