Have you ever been asked to perform welding work inside a tank, vessel, or other enclosed space? Are you unsure about the complex safety requirements for confined space welding operations?
Or maybe you’re responsible for ensuring compliance but feel overwhelmed by the intricate regulations and life-safety procedures involved? Confined space welding represents one of the most hazardous activities in the welding industry, requiring strict adherence to safety protocols that can literally mean the difference between life and death.
Welding in confined spaces requires comprehensive safety procedures including atmospheric testing, ventilation systems, entry permits, emergency rescue plans, and continuous monitoring throughout the operation.
OSHA’s Confined Space Standard (29 CFR 1910.146) mandates specific requirements for permit-required confined spaces, while additional welding-specific safety measures address fire hazards, toxic fume exposure, and emergency evacuation procedures.
Understanding and implementing these critical safety requirements isn’t just about regulatory compliance—it’s about protecting lives and preventing the serious injuries and fatalities that occur when proper procedures aren’t followed.
Understanding Confined Spaces in Welding
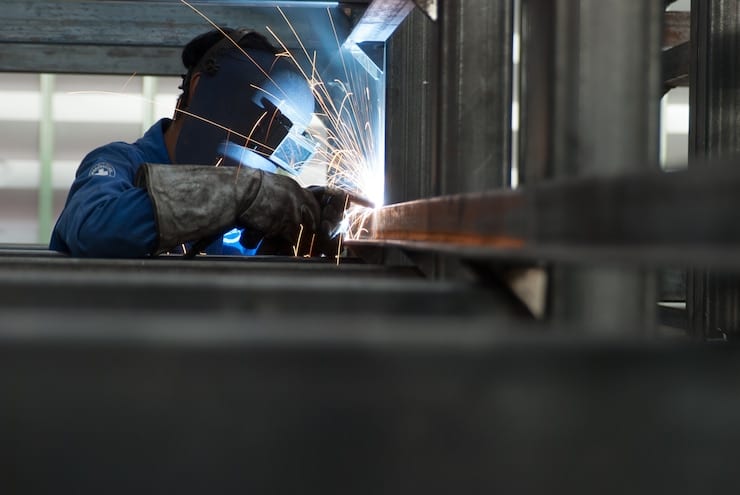
OSHA Definition and Classification
OSHA defines a confined space as an area that meets three criteria:
- Large enough for worker entry: A person can bodily enter and perform assigned work.
- Limited entry/exit means: Has limited or restricted means of entry or exit.
- Not designed for continuous occupancy: Not designed for continuous human occupancy.
Permit-Required Confined Spaces have additional hazards and require formal entry procedures when they contain or have potential for:
- Hazardous atmosphere: Toxic gases, oxygen deficiency, or flammable vapors.
- Engulfment potential: Materials that could engulf an entrant.
- Configuration hazards: Inwardly converging walls or sloped floors leading to entrapment.
- Other recognized serious hazards: Any condition that poses serious physical harm.
OSHA Regulatory Framework
29 CFR 1910.146 – Permit-Required Confined Spaces
Entry Permit System: OSHA requires a comprehensive permit system for confined space entry:
- Written entry permits: Documenting all safety measures and authorizations.
- Atmospheric testing: Continuous monitoring of air quality and hazardous gases.
- Rescue procedures: Pre-planned emergency evacuation and rescue operations.
- Communication systems: Maintaining contact between entrants and attendants.
Key Permit Requirements:
- Purpose and location: Specific identification of work to be performed.
- Authorized entrants: Names of workers approved for entry.
- Attendant designation: Person responsible for monitoring outside the space.
- Entry supervisor: Individual responsible for overall operation safety.
- Duration validity: Time limits for permit effectiveness.
Pre-Entry Safety Procedures
Atmospheric Testing and Monitoring
Initial Atmospheric Assessment: Before any entry, comprehensive atmospheric testing must evaluate:
- Oxygen levels: Must be between 19.5% and 23.5% by volume.
- Flammable gases: Must be below 10% of Lower Explosive Limit (LEL).
- Toxic substances: Must be below permissible exposure limits (PEL)
- Carbon monoxide: Particularly critical in spaces with previous combustion.
Continuous Monitoring
- Real-time detection: Continuous monitoring throughout the operation.
- Multi-gas detectors: Devices capable of simultaneous monitoring of multiple hazards.
- Alarm systems: Audible and visual warnings for dangerous conditions.
- Calibration verification: Regular calibration of monitoring equipment.
Ventilation Systems
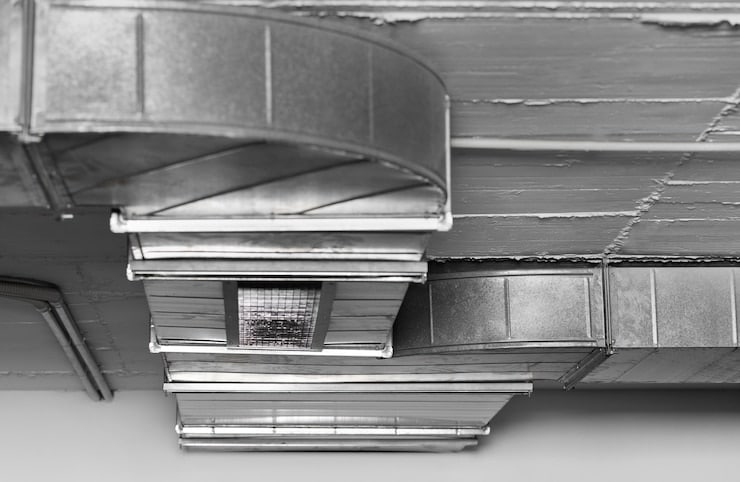
Mechanical Ventilation Requirements: Proper ventilation is critical for confined space welding safety:
- Air exchange rates: Minimum requirements vary by space size and welding process.
- Fresh air supply: Clean, breathable air from outside the confined space.
- Exhaust systems: Removing contaminated air and welding fumes.
- Air flow patterns: Ensuring proper circulation without creating dead air zones.
Ventilation Design Considerations
- Supply air location: Positioning to provide fresh air to worker breathing zone.
- Exhaust placement: Located to capture welding fumes at their source.
- Air velocity: Sufficient to remove contaminants without interfering with welding.
- Backup systems: Redundant ventilation in case of primary system failure.
Entry Procedures and Permits
Permit Documentation Requirements
Comprehensive Entry Permits Must Include
- Space identification: Specific location and description of confined space.
- Purpose of entry: Detailed description of work to be performed.
- Date and duration: Specific timeframe for permitted entry.
- Authorized personnel: Names and roles of all individuals involved.
- Testing results: Atmospheric monitoring data and acceptability.
- Safety equipment: Required PPE (like welding gloves) and safety equipment checklist.
- Emergency procedures: Specific rescue and evacuation protocols.
Entry Team Roles and Responsibilities
Entry Supervisor
- Overall safety responsibility: Ensuring all safety measures are in place.
- Permit authorization: Reviewing and signing entry permits.
- Condition monitoring: Verifying safe conditions throughout operation.
- Emergency authority: Power to suspend operations if conditions become unsafe.
Attendant Responsibilities
- Continuous monitoring: Maintaining visual or voice contact with entrants.
- Atmospheric surveillance: Monitoring air quality and safety conditions.
- Emergency response: Initiating rescue procedures when necessary.
- Communication coordination: Relaying information between entrants and emergency services.
Entrant Duties
- Safety compliance: Following all prescribed safety procedures.
- Hazard recognition: Identifying and reporting dangerous conditions.
- Communication maintenance: Regular contact with attendant.
- Emergency evacuation: Immediate exit when directed or when sensing danger.
Welding-Specific Safety Measures
Fire Prevention and Protection
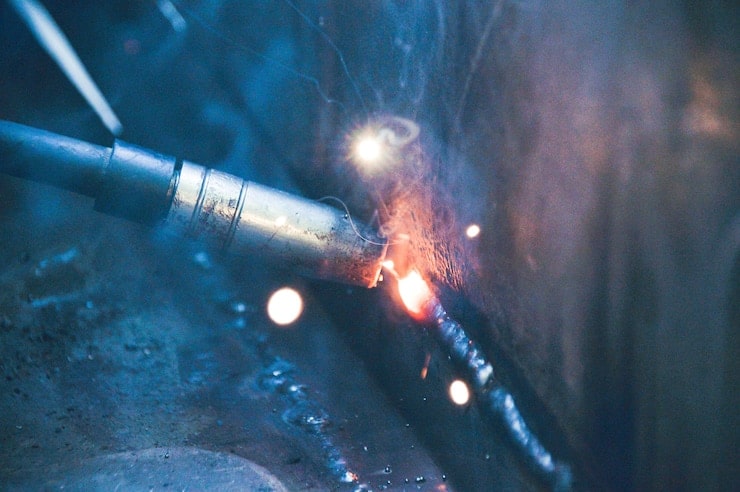
Combustible Material Management
- Material removal: Eliminating flammable materials from welding area.
- Protective barriers: Fire-resistant shields for materials that cannot be removed.
- Hot work permits: Additional authorization for welding in fire-prone areas.
- Fire watch procedures: Dedicated personnel monitoring for fire hazards.
Fire Suppression Systems
- Portable extinguishers: Appropriate for metal fires and electrical hazards.
- Fixed suppression systems: Automated fire suppression in high-risk spaces.
- Water spray systems: Cooling and suppression for large confined spaces.
- Emergency shutdown: Rapid cessation of welding operations during fire emergencies.
Fume and Gas Control
Welding Fume Management: Different welding processes create specific hazards requiring targeted controls:
- Stainless steel welding: Hexavalent chromium exposure requiring enhanced protection.
- Galvanized material welding: Zinc oxide fume prevention and medical monitoring.
- Aluminum welding: Ozone generation requiring specialized ventilation.
- Flux-cored welding: Increased fume generation requiring enhanced extraction.
Gas Hazard Mitigation
- Shielding gas accumulation: Preventing argon or CO2 buildup in low areas.
- Nitrogen displacement: Preventing oxygen displacement by inert gases.
- Carbon monoxide generation: Monitoring CO levels from incomplete combustion.
- Hydrogen generation: Managing hydrogen gas from certain welding processes.
Personal Protective Equipment (PPE)
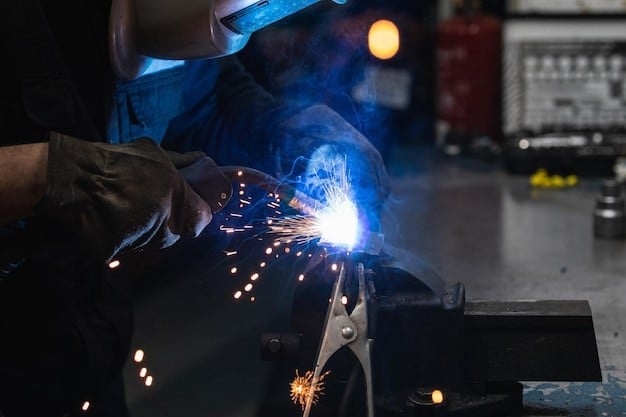
Respiratory Protection Systems
Supplied Air Respirators: For confined space welding, supplied air systems often provide optimal protection:
- Continuous flow systems: Constant supply of clean, breathable air.
- Pressure demand systems: Positive pressure preventing contaminant entry.
- Emergency escape breathing apparatus: Backup air supply for emergency evacuation.
- Air quality testing: Regular testing of supplied air for contaminants.
Self-Contained Breathing Apparatus (SCBA)
- Emergency escape: Short-duration protection for emergency evacuation.
- Entry team backup: Emergency breathing apparatus for rescue personnel.
- Duration limitations: Typically 30-60 minutes of air supply.
- Training requirements: Specialized training for SCBA operation and maintenance.
Enhanced Protective Equipment
Welding-Specific PPE for Confined Spaces
- Flame-resistant clothing: Enhanced protection in confined environments.
- Fall protection: Harnesses and lifelines for vertical confined spaces.
- Communication equipment: Hands-free communication systems.
- Emergency signaling devices: Personal alarms and location beacons.
Environmental Protection
- Cooling vests: Managing heat stress in enclosed environments.
- Insulated clothing: Protection from extreme temperatures.
- Chemical-resistant gear: Protection from corrosive atmospheres.
- Anti-static equipment: Preventing static discharge in flammable atmospheres.
Emergency Procedures and Rescue Operations
Rescue Team Requirements
OSHA Rescue Standards
- Trained rescue personnel: Specialized training in confined space rescue.
- Rescue equipment: Appropriate equipment for specific space configurations.
- Response time requirements: Immediate availability for emergency response.
- Practice and drills: Regular training exercises to maintain readiness.
External Rescue Services
- Local fire department coordination: Pre-arranged emergency response agreements.
- Industrial rescue teams: Specialized confined space rescue contractors.
- Medical support: Emergency medical services familiar with welding hazards.
- Equipment compatibility: Ensuring rescue equipment works with specific confined spaces.
Emergency Communication Systems
Communication Requirements
- Continuous contact: Maintaining communication between entrants and attendants.
- Emergency signals: Pre-arranged signals for immediate evacuation.
- External communication: Direct contact with emergency services.
- Backup systems: Redundant communication methods in case of primary failure.
Technology Solutions
- Two-way radio systems: Clear communication in noisy environments.
- Emergency beacons: Automatic distress signals during emergencies.
- Video monitoring: Visual contact maintenance for complex operations.
- Atmospheric monitoring alarms: Automatic warnings for dangerous conditions.
Training and Competency Requirements
Worker Training Programs
Comprehensive Training Must Cover
- Hazard recognition: Identifying confined space and welding-specific dangers.
- Safety procedures: Proper entry, working, and exit procedures.
- Equipment operation: Correct use of safety and monitoring equipment.
- Emergency response: Immediate actions during emergency situations.
Specialized Welding Training
- Process-specific hazards: Understanding dangers of different welding methods.
- Material-specific risks: Recognizing hazards from different base materials.
- Equipment limitations: Understanding when additional protection is needed.
- Quality vs. safety balance: Maintaining weld quality while prioritizing safety.
Certification and Documentation
Training Documentation Requirements
- Initial training records: Comprehensive records of all safety training.
- Refresher training: Regular updates on procedures and regulations.
- Competency verification: Testing to ensure understanding and skill retention.
- Medical fitness: Health evaluations for confined space and respiratory protection work.
Industry-Specific Applications
Petrochemical and Refining
Unique Challenges
- Hydrocarbon residues: Persistent flammable and toxic substances.
- High-temperature operations: Extreme heat adding to environmental dangers.
- Catalyst dusts: Toxic particulates requiring specialized protection.
- Process isolation: Ensuring complete isolation from active process systems.
Marine and Shipbuilding
Maritime-Specific Considerations
- Ballast tanks: Large spaces with complex configurations.
- Fuel system work: High fire and explosion risks.
- Ventilation challenges: Limited natural air circulation.
- Access difficulties: Complex entry and exit routes.
Power Generation
Utility Industry Applications
- Boiler work: High-temperature environments with complex geometries.
- Cooling tower maintenance: Confined spaces with water and chemical hazards.
- Nuclear applications: Radiation safety combined with confined space protocols.
- Turbine maintenance: Precision work in restricted spaces.
Closing Thoughts
Welding in confined spaces demands unwavering commitment to safety procedures that protect lives and prevent serious injuries. The complexity of OSHA requirements reflects the serious nature of these hazards, atmospheric dangers, fire risks, and emergency evacuation challenges that require comprehensive planning and execution.
Success in confined space welding requires more than technical welding skills, it demands comprehensive understanding of safety systems, emergency procedures, and regulatory compliance. Organizations that invest in proper training, equipment, and procedures not only protect their workers but also avoid the devastating consequences of confined space accidents.
Whether you’re a welder, supervisor, or safety professional, remember that no welding job is worth compromising safety. The procedures and requirements outlined here represent minimum standards developed from tragic lessons learned in the industry. By following these guidelines and maintaining constant vigilance, we can ensure that every worker returns home safely at the end of each shift.
Related Articles
The Complete Welding PPE Checklist