The construction industry often faces challenges with structural integrity and durability, where weak joints and frameworks can lead to catastrophic failures. Welding presents a robust solution by providing strong, reliable metal connections essential for supporting and bearing loads in various structures. Its application in infrastructure, building, and industrial projects ensures stability and longevity.
By employing advanced welding techniques, the construction sector can achieve enhanced safety, efficiency, and cost-effectiveness. This article explores the critical role of welding in modern construction, exploring its applications, techniques, and benefits.
Importance of Welding in Construction
Strong, reliable metal frameworks are essential in construction to ensure the potency and safety of structures. Welding plays a vital role in creating these frameworks by joining metal components securely. Without proper welding, structures like buildings, bridges, and industrial facilities would be prone to weaknesses, compromising their integrity.
Quality welding ensures that metal parts are fused correctly, providing the necessary strength to support loads and resist environmental stresses. This process not only enhances the durability of constructions but also ensures their long-term safety and functionality. In essence, welding is fundamental to the structural soundness of construction projects.
Applications of Welding in Construction
Welding has a range of applications in the construction industry, each crucial for ensuring structural integrity and safety. Also, it is used in retrofitting and upgrading existing structures to extend the life of aging infrastructure.
Infrastructure Construction
Welding is essential for building robust and long-lasting bridges, highways, and tunnels in infrastructure construction. These structures must withstand heavy loads and adverse environmental conditions.
Welding ensures that the metal components in these infrastructures are securely joined, providing the necessary strength and stability. For instance, the welding of steel beams and columns in bridge construction guarantees that these elements can sustain the weight of vehicles and resist vibrations from traffic.
Building Construction
Building construction relies heavily on welding to create strong frameworks. Skyscrapers, residential buildings, and commercial complexes all require welding to join steel beams and columns. This process provides the skeletal structure that supports the entire building.
Without welding, these structures would lack the necessary durability to stand against wind loads, seismic activities, and other stresses. Additionally, welding appears in installing metal roofing, staircases, and various other architectural elements that contribute to a building’s overall strength and functionality.
Industrial Construction
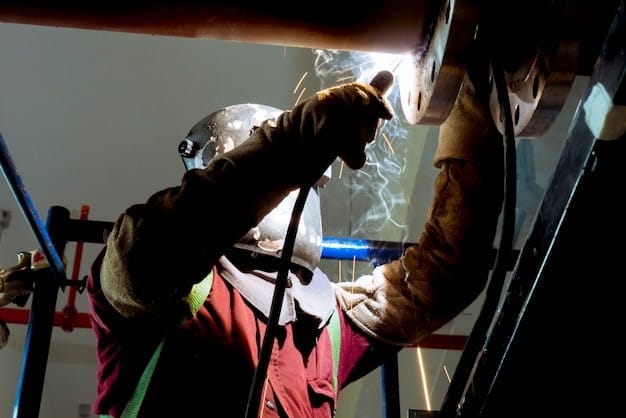
Welding is vital in industrial construction, especially for assembling factories, power plants, and refineries. These facilities require robust structures to house heavy machinery and equipment. Welding ensures that the metal frameworks can support substantial weights and endure harsh operating conditions.
For example, welding can construct pressure vessels, storage tanks, and pipelines, which are integral to the functioning of industrial plants. The precision and reliability of welding in these applications are crucial for maintaining safety standards and operational efficiency.
Maintenance and Repair
Welding is essential in maintaining and repairing existing structures. Welders often reinforce aging bridges, buildings, and industrial facilities, extending their lifespan and ensuring safety. This process involves fixing cracks, adding reinforcements, and replacing worn-out metal parts, thereby maintaining structural integrity and preventing potential failures.
Specialized Construction Projects
Welding is also useful in constructing specialized structures like sports stadiums, airports, and large-scale public monuments. In these projects, welding provides the flexibility to create complex and unique designs while ensuring structural integrity. For instance, the intricate metal frameworks of stadium roofs and the expansive steel structures of airport terminals rely heavily on welding for both stability and aesthetic appeal.
Welding Techniques in Construction
Welding is a fundamental process in construction involving various techniques to join metal parts securely. Each welding method has unique advantages and suits specific industry applications. Here, we will discuss some common welding techniques used in construction.
Stick Welding/SMAW
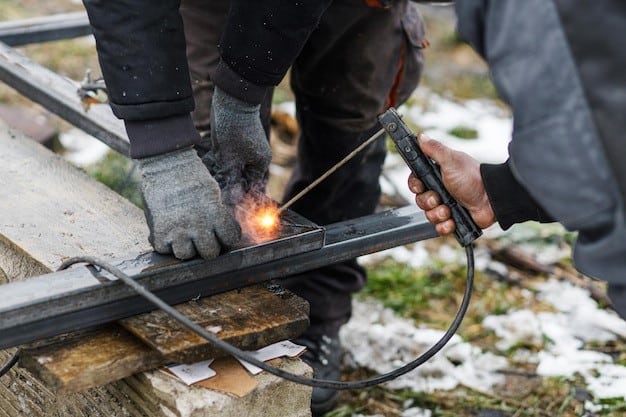
Stick welding (SMAW) is one of the most widely used welding methods in construction. It involves utilizing a consumable electrode coated in flux to lay the weld. An electric current passes through the electrode, creating an arc between it and the metal workpiece. The heat made by the arc melts the electrode and the workpiece, forming a weld pool that solidifies to join the metals. Stick welder is favored for its versatility and capability to be used in various positions and environments, including outdoor and windy conditions.
TIG Welding
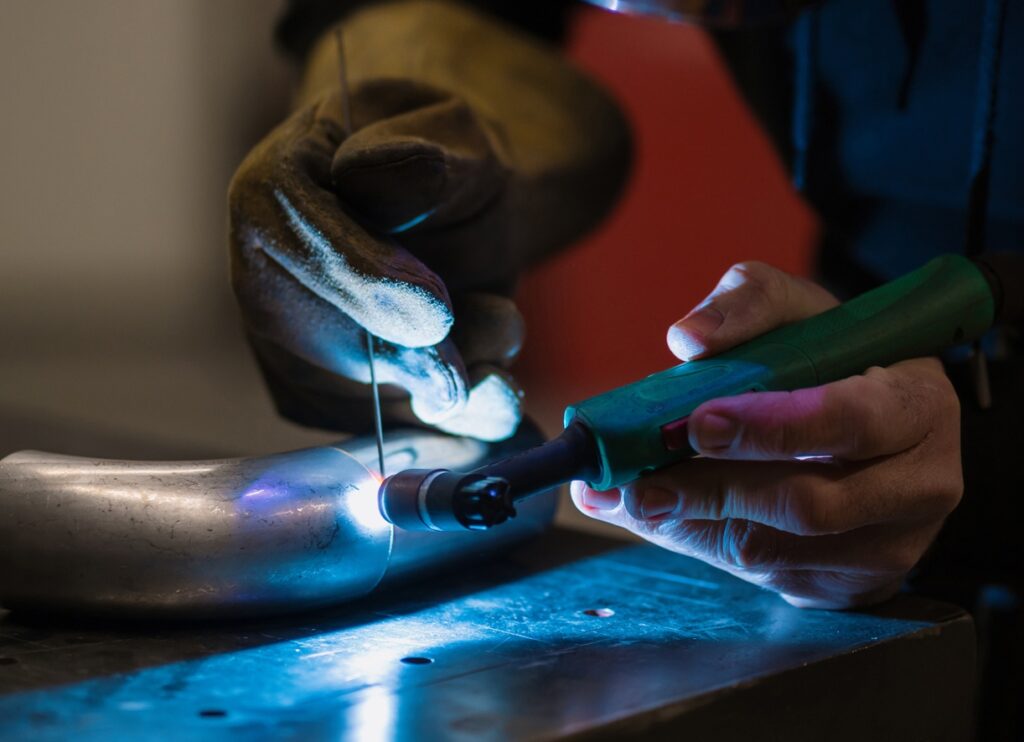
Tungsten Inert Gas (TIG) welding is a technique that uses a non-consumable tungsten electrode to complete the weld. Using argon or helium (inert shielding gases) covers the weld area from atmospheric contamination.
TIG welding owns the name of making high-quality, precise welds, making it ideal for applications requiring strong, clean welds on thin materials. It is commonly used in industries where aesthetics and strength are critical, such as aerospace and automotive sectors. However, TIG welding needs a high level of skill and is often slower than MIG welding and FCAW. Reliable TIG welder suppliers play an important role in the process of keeping quality welds.
MIG Welding
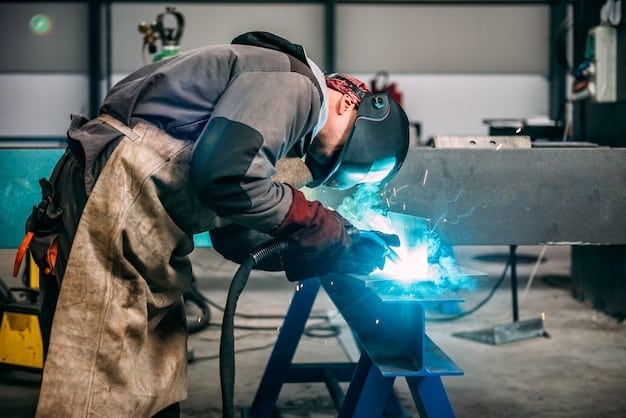
Metal Inert Gas (MIG), or Gas Metal Arc Welding, applies a consumable wire electrode and a shielding gas to weld. The wire is fed continuously through a welding gun, melting and fusing with the workpiece to form the weld. MIG welding is famous for its speed and ease of use, making it popular for both industrial and DIY applications. It is particularly effective for welding non-ferrous metals and thin-gauge steel. The process is more sensitive to contaminants than some other welding methods, allowing for quicker preparation and cleanup times.
Flux-Cored Arc Welding (FCAW)
Flux-Cored Arc Welding (FCAW) is identical to MIG welding, but it utilizes a special tubular wire filled with flux. There are gas-shielded FCAW and self-shielded FCAW. The second one generates a protective gas shield during welding, which can eliminate the need for an external shielding gas. This makes it suitable for outdoor and windy conditions. The process is highly efficient, allowing for high-speed welding with deep penetration. FCAW is common in construction projects requiring heavy-duty welds, such as shipbuilding, pipelines, and structural steelwork.
Submerged Arc Welding (SAW)
This method involves forming an arc beneath a blanket of granular flux, protecting the weld from contamination and allowing for deep penetration and high deposition rates. It is typically used for large, flat surfaces and long seams.
Plasma Arc Welding (PAW)
Similar to TIG welding, this technique uses a plasma torch to produce a more concentrated arc, resulting in higher precision and control. It is often employed in industries requiring detailed and intricate welds.
Resistance Welding
This method, which includes spot welding and seam welding, joins thin sheets of metal by applying pressure and passing an electric current through them. This is common in the automotive and manufacturing industries.
Laser Welding
This technique uses a high-powered laser beam to melt and fuse materials. It offers precision and control for delicate or high-volume applications. It is helpful for industries where high accuracy and minimal distortion are essential.
Important Benefits of Welding in Construction
Welding Type | Infrastructure Construction | Building Construction | Industrial Construction |
Stick Welding (SMAW) | Suitable for outdoor work and rough environments Good for welding thick materials Portable and versatile | Good for general construction tasks Can be used for various metals Cost-effective for small projects | Ideal for heavy-duty welding Reliable in harsh environments Good for repair and maintenance work |
TIG Welding | Provides high precision and clean welds Ideal for thin materials and detailed work Excellent for stainless steel and aluminum | Produces high-quality, clean welds for visible areas Ideal for intricate or high-precision work | Suitable for applications requiring high-quality welds Good for welding thin materials and precise components |
MIG Welding | Fast and efficient for large-scale infrastructure projects Good for various materials and thicknesses Less clean-up required | Efficient for large and small-scale construction Good for fast production and less welding spatter | Excellent for mass production and automation Fast and efficient for large structures and components |
Flux-Cored Arc Welding (FCAW) | Suitable for outdoor and windy conditions Good for thick materials High deposition rate | Effective for various construction tasks Can handle dirty or rusty surfaces Good for heavy-duty applications | Ideal for heavy industrial applications High deposition rate for thick materials Good for structural components |
Submerged Arc Welding (SAW) | Highly efficient for large-scale infrastructure projects Produces high-quality welds with minimal spatter High deposition rate | Good for large, structural components High productivity and quality in repetitive tasks | Excellent for thick materials and large sections High-speed welding with minimal post-weld cleanup |
Plasma Arc Welding (PAW) | Ideal for precision work and thin materials Can be used for welding in confined spaces Produces clean welds | Effective for detailed work and thin sections Suitable for materials requiring precision and quality | Good for high-precision applications Suitable for thin materials and intricate parts |
Resistance Welding | Suitable for high-volume production and repetitive tasks Fast and efficient Good for sheet metal and thin materials | Effective for welding thin materials and components Fast production for repetitive tasks | Ideal for high-volume manufacturing Good for joining thin materials and components efficiently |
Laser Welding | Provides very high precision and clean welds Ideal for complex and high-quality applications Minimal thermal distortion | Excellent for fine and detailed work Suitable for high-end construction with aesthetic requirements | Ideal for precision applications and high-tech industries Provides strong and clean welds for complex components |
Benefits of Welding in the Construction Industry
Welding offers numerous benefits in the construction industry, contributing to the strength, efficiency, and cost-effectiveness of construction projects.
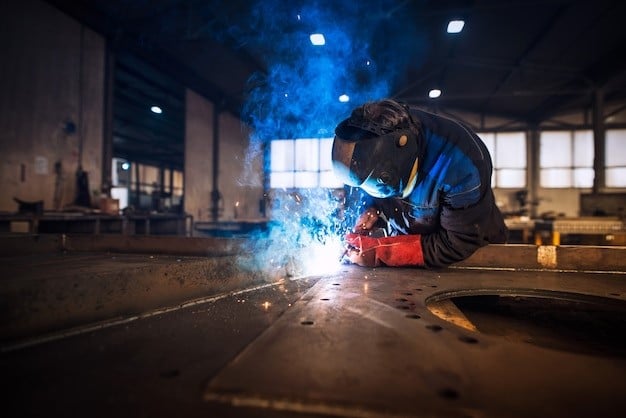
Durability
- Welding creates strong, permanent joints that enhance the durability of structures.
- Properly welded connections can withstand significant loads and stresses.
- This durability is crucial for the safety and longevity of buildings, bridges, and other structures.
Efficiency
- Welding processes can be completed quickly, speeding up construction timelines.
- Techniques like MIG and FCAW offer high deposition rates, allowing for faster project completion.
- Efficient welding methods reduce labor costs and improve overall productivity.
Flexibility
- Welding can be used in a range of materials, including steel, aluminum, and other alloys.
- It is suitable for various construction applications, from small-scale repairs to large infrastructure projects.
- Welders can work in diverse environments, including tight spaces and outdoor settings.
Cost-Effectiveness
- Welding reduces the need for additional materials like bolts and rivets, lowering material costs.
- Efficient welding techniques minimize labor expenses by reducing the time required for assembly.
- The long-term durability of welded structures reduces maintenance and repair costs over time.
Versatility
- Welding is adaptable to different construction needs, from joining pipes to fabricating large steel frameworks.
- Various welding techniques cater to specific project requirements, ensuring optimal results.
Precision
- Advanced welding methods like TIG and laser welding provide high precision and control.
- This precision is essential for projects that demand detailed and intricate work.
Environmental Benefits
- Modern welding techniques produce less waste and emissions compared to traditional methods.
- This contributes to more sustainable construction practices.
Final Thoughts
Welding plays an essential role in construction, providing the strength and reliability needed for safe structures. To get the best outcome in construction, finding the right welding supplies is important. It ensures the durability of buildings, bridges, and industrial facilities.
Recent trends in welding include automation, which increases efficiency and precision, and sustainable practices, which reduce environmental impact. Automated welding systems and eco-friendly techniques are transforming the industry, making construction projects faster, safer, and more sustainable. These advancements highlight the ongoing evolution and significance of welding in modern construction.
FAQs
What are the most common welding techniques used in construction?
The most common welding techniques in construction are Stick Welding (SMAW), TIG Welding (GTAW), MIG Welding (GMAW), and Flux-Cored Arc Welding (FCAW).
Why is welding important in the construction industry?
Welding is crucial in construction for creating strong, durable, and reliable metal frameworks that support the structural integrity of buildings, bridges, and industrial facilities.
How does automation impact welding in construction?
Automation in welding increases efficiency, precision, and safety, allowing for faster project completion and consistent weld quality.
What are the environmental benefits of modern welding techniques?
Modern welding techniques produce less waste and emissions, contributing to more endurable construction practices and reducing the environmental impact.