Welding is critical in constructing and maintaining pipelines and facilities in the oil and gas industry. However, this industry faces significant challenges, including harsh environmental conditions, strict safety standards, and the need for high-quality welds that can withstand extreme pressures. Advanced welding techniques such as TIG, MIG, and stick welding are employed to address these issues.
These methods ensure strong, reliable connections that meet industry requirements while enhancing safety and efficiency. By adopting innovative welding technologies, the industry can overcome its challenges, ensuring the integrity and longevity of vital infrastructure.
Welding in the Oil and Gas Industry
Welding is fundamental to the oil and gas industry, particularly in the construction and maintenance of pipelines. Pipeline welding is essential because it ensures that the vast network of pipelines used to transport oil and gas is safe and secure. A single failure in a pipeline can lead to significant financial losses, environmental damage, and safety hazards. Therefore, the integrity of these pipelines is crucial, and welding is the key process that ensures their durability and reliability.
Various welding techniques are used in the industry, each serving a specific purpose. Stick welding, also known as Shielded Metal Arc Welding (SMAW), is widely used for its simplicity and effectiveness outdoors. This method is particularly suited for welding thick materials and is often employed in pipeline construction.
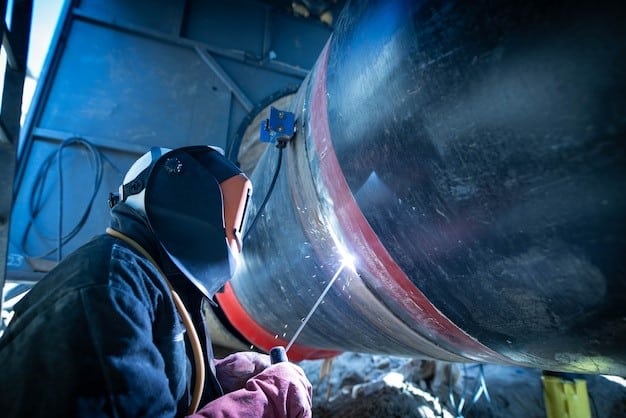
MIG welding is another common technique used in the industry. It is known for its speed and efficiency, making it ideal for long welding tasks on pipelines and in controlled environments. Flux-Cored Arc Welding (FCAW) is similar to MIG welding but uses a flux-filled wire, providing penetration and strength, which is critical for pipelines subjected to high pressures.
TIG welder suppliers often provide machines with precision and quality. TIG welding is ideal for welding thinner materials and for applications where require the high precision of weld quality. Each of these techniques plays a vital role in maintaining the infrastructure of the oil and gas industry, ensuring that pipelines remain safe and functional.
Welding Techniques and Their Benefits for the Oil & Gas Industry
Welding Technique | Overview | Benefits in Oil & Gas Industry |
Stick Welding (SMAW) | Uses a consumable electrode coated in flux. | Reliable for outdoor use, effective on thick materials. |
MIG Welding (GMAW) | Employs a continuous wire feed as an electrode. | Fast and efficient for long welds, suitable for thin materials. |
TIG Welding (GTAW) | Utilizes tungsten welding electrodes and separate filler rods. | Provides high precision and quality welds, ideal for thin materials. |
Flux-Cored Arc Welding (FCAW) | Uses a flux-cored wire that provides protection. | Good penetration, suitable for thick materials and outdoor use. |
Benefits of Welding in the Oil & Gas Industry
These benefits underscore the importance of welding in the oil and gas industry. From enhancing safety and quality to improving efficiency and reducing costs, welding remains a critical process that supports the industry’s growth and sustainability.
Efficiency
- Increased Productivity: Welding in the oil and gas industry allows for the rapid construction and repair of pipelines and facilities. A MIG welding machine provides a high deposition rate, enabling workers to complete tasks quickly, reducing downtime, and maintaining continuous operation of essential infrastructure.
- Minimized Downtime: Efficient welding processes ensure that maintenance and repairs are completed swiftly, minimizing disruption to operations. This is critical in an industry where delays can lead to substantial financial losses.
- Consistent Performance: Welding methods such as TIG welding produce consistent, high-quality welds that require less rework. This consistency reduces the time spent on repairs and inspections, enhancing efficiency.
Versatility
- Adaptable Techniques: The oil and gas industry employs various welding techniques, each adaptable to different materials and environmental conditions. Whether working with thick steel pipelines or thinner components, a welding method is suited for the task.
- Wide Range of Applications: Welding is common in many areas, from pipeline construction to the repair of offshore platforms. The ability to apply welding techniques across diverse settings makes it a versatile tool in the industry.
- Customization for Specific Needs: Adjustments in welding processes are often based on a project’s specific requirements. For example, FCAW can be used in environments with high winds, while MIG welding is suited for indoor settings.
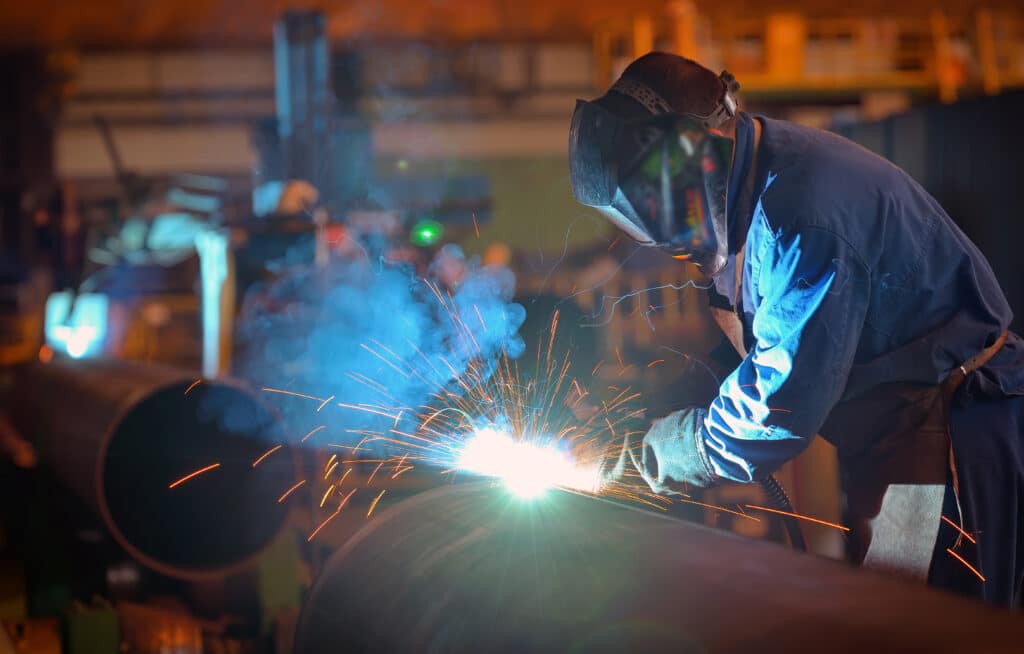
Quality
- High-Integrity Welds: The quality of welds is crucial in the oil and gas industry, where pipelines must withstand extreme pressures and temperatures. Techniques like TIG welding produce clean, precise welds with minimal defects, ensuring the integrity of critical infrastructure.
- Long-Term Durability: Quality welding leads to long-lasting pipelines and facilities. Properly executed welds can prevent leaks, fractures, and other issues that could compromise the safety and efficiency of operations.
- Meeting Industry Standards: Welding in the oil and gas industry adheres to strict quality standards. Compliance with these standards ensures the infrastructure is safe and reliable, reducing the risk of catastrophic failures.
Safety
- Reduced Risk of Accidents: High-quality welding minimizes the risk of pipeline leaks or ruptures, which can lead to accidents, environmental harm, and loss of life. Adhering to safety protocols during welding operations is essential for preventing such incidents.
- Enhanced Worker Safety: Modern welding techniques, including automated and robotic welding, reduce the need for workers to operate in hazardous environments. This shift toward automation in welding processes contributes to a safer work environment.
- Compliance with Safety Regulations: Welding practices in the oil and gas industry have stringent safety regulations. Compliance ensures that all welding operations are conducted safely, protecting both workers and the environment.
Cost-Effectiveness
- Reduced Maintenance Costs: High-quality welding reduces the need for frequent repairs and maintenance, leading to significant cost savings over time. Properly welded pipelines and structures are less likely to develop issues that require costly interventions.
- Lower Operational Costs: Efficient welding processes reduce the time and resources needed to complete projects. This efficiency translates into lower operational costs, making welding an economically viable solution for the industry.
- Preventing Costly Failures: Investing in high-quality welding upfront can prevent costly failures later on. Welding helps avoid the financial repercussions of leaks, spills, and accidents by ensuring the durability and integrity of pipelines and facilities.
Environmental Impact
- Reduced Emissions: High-quality welding helps prevent leaks and spills, reducing the environmental impact of oil and gas operations. By ensuring that pipelines are secure, welding contributes to the protection of surrounding ecosystems.
- Energy Efficiency: Modern welding techniques are often more energy-efficient, reducing the overall carbon footprint of construction and maintenance activities in the oil and gas industry.
- Sustainable Practices: As the industry moves toward more sustainable practices, welding ensures that infrastructure is built and maintained with minimal environmental impact.
Challenges in Welding for Oil and Gas
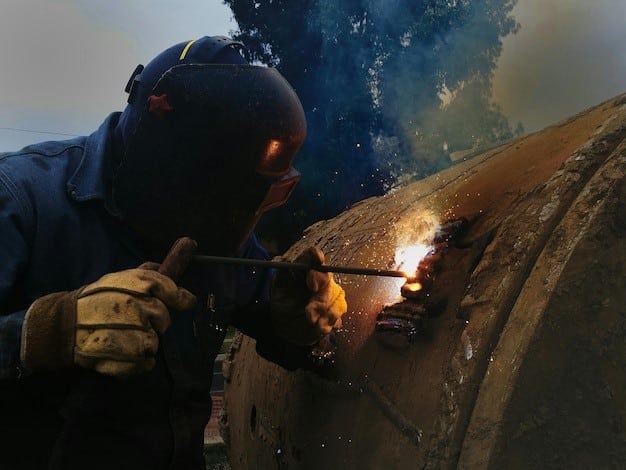
Harsh Environment
- Extreme Weather Conditions: Welding in the oil and gas industry often occurs in harsh environments, such as offshore platforms or remote pipelines exposed to extreme temperatures, high winds, and heavy rain. These conditions make it challenging to achieve consistent, high-quality welds.
- Corrosive Atmospheres: In many cases, welding must be performed in environments where the air is laden with corrosive elements, such as saltwater or chemicals. This can degrade the welding materials and tools, leading to complications in the welding process.
- Limited Accessibility: Welders often work in confined spaces or difficult-to-reach areas, such as deep-sea pipelines or elevated platforms. This limited accessibility makes it hard to maneuver equipment and achieve the necessary precision.
High-Pressure Applications
- Stress on Materials: Welding in high-pressure environments, such as in pipelines carrying natural gas or oil, stresses the welded joints significantly. The welds must be strong enough to withstand these pressures without failing.
- Risk of Failures: The high-pressure conditions in oil and gas applications increase the risk of weld failures, leading to catastrophic consequences, including leaks, explosions, and environmental damage.
- Specialized Techniques Required: Welding in high-pressure situations often requires specialized techniques and materials, such as TIG welding with high-strength alloys, to ensure the integrity of the welds.
Strict Quality Standards
- Compliance with Regulations: The oil and gas industry is governed by stringent quality standards dictating welding processes and materials. Meeting these standards is crucial to ensuring the safety and reliability of the infrastructure.
- Frequent Inspections: Welds must undergo regular inspections to meet the required quality standards. These inspections can be time-consuming and costly but are necessary to maintain the integrity of the pipelines and facilities.
- Documentation and Traceability: Welding operations in the oil and gas industry must be meticulously documented, with each weld traceable to ensure compliance with industry standards and regulations.
Other Common Challenges
- Skilled Labor Shortages: The oil and gas industry has a high demand for skilled welders, and shortages of qualified personnel can lead to project delays and reduced quality of work.
- Technological Limitations: While there are more advancements, technological limitations in welding processes remain that can affect the quality and speed of operations, particularly in challenging environments.
- Cost Constraints: Balancing the need for high-quality welding with budgetary constraints is a constant challenge in the oil and gas industry. Cutting corners to save costs can lead to subpar welds and increased risks.
Innovations and Technologies in Welding
Advanced Materials
Advanced materials, such as corrosion-resistant alloys, have revolutionized welding in the oil and gas industry. These materials are designed to withstand harsh environmental conditions, reducing the likelihood of pipeline failures due to corrosion.
High-strength steels (e.g. duplex stainless steels) are increasingly used in pipeline construction. These materials provide enhanced durability and can handle the extreme pressures found in oil and gas applications, ensuring the long-term reliability of welded joints.
Use of Robotics and Automation
Robotics and automation have become integral to welding operations, especially offshore and onshore projects. Automated welding systems provide consistent, precise welds, reducing the margin for human error.
Robotics play a crucial role in environments where human access is limited or hazardous. They can operate in confined spaces or at great depths, performing complex welds that would be difficult or impossible for human welders.
The adoption of robotics and automation reduces the need for human workers to perform dangerous tasks. This shift increases safety and enhances the overall efficiency and quality of welding operations in the oil and gas industry.
Final Thoughts
Welding remains a cornerstone of the oil and gas industry, vital for building and maintaining critical infrastructure. Advances in welding techniques and materials have significantly improved efficiency, safety, and durability. Despite challenges such as harsh environments and strict standards, ongoing innovations continue to enhance the quality of welds. Embracing these advancements helps ensure the integrity and longevity of pipelines and facilities, supporting the industry’s need for reliable and effective operations.
FAQs
What are the most common welding techniques used in the oil and gas industry?
Stick welding, MIG welding, TIG welding, and Flux-Cored Arc Welding (FCAW) are all common methods, each suited for different materials and conditions.
What are the key challenges in welding pipelines for oil and gas?
Challenges include harsh environmental conditions, high pressure, and strict quality standards.
How do robotics and automation improve welding in the oil and gas industry?
Robotics and automation offer precise, consistent welds, enhance efficiency, and improve safety in difficult or hazardous environments.