Welding transforms raw metal into structures that define our modern world—think towering bridges, sleek aircraft, or even intricate medical devices. Success hinges on understanding the welding metals you’re working with. This guide is your resource for mastering welding metals, offering insights into their characteristics, advanced welding methods, and essential practices for flawless results.
What Makes a Metal Weldable?
Weldability is the property of a metal to be welded into a strong, homogeneous joint free from any defect such as cracks or porosity. It’s controlled by three fundamental properties:
- Melting Point: Steel has a melting point of about 2,500°F (1,371°C), while aluminum has a melting point of only 1,221°F (660°C), having influence on heat input requirements. Related article: The Impact of Material Melting Points on Welding.
- Thermal Conductivity: Copper conducts heat 10 times more quickly than steel (401 W/m·K vs. 43 W/m·K), needing intense, concentrated energy.
- Alloy Composition: Carbon added to iron yields steel, strengthening but increasing propensity for cracking; zinc in brass volatilizes, decreasing weld strength.
Melting Points of Common Welding Metals
Material | Melting Point (°C) |
Aluminum | 660 |
Steel | 1370 |
Copper | 1085 |
Gold | 1064 |
Iron | 1538 |
Lead | 327 |
Tungsten | 3422 |
Any metal may be welded skillfully, but exceptions like lead or mercury do not melt or fuse because they have low melting points or liquid phases.
Common Welding Metals: Properties and Challenges
Here is an in-depth look at eight heavy metals, illustrated with precise information and welding nuances.
Steel (Carbon and Low-Alloy)
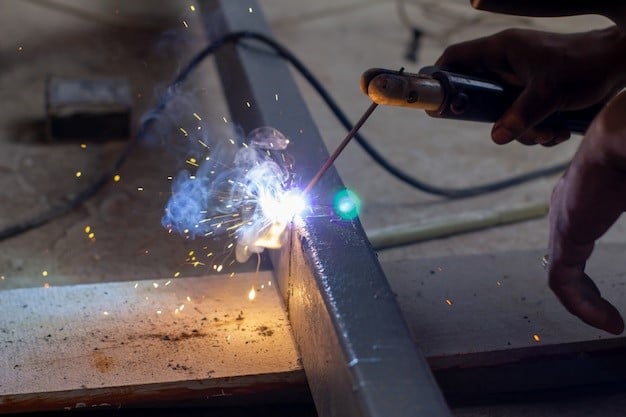
- Properties: Density of 7.85 g/cm³, tensile strength up to 60,000 psi, melting point ~2,500°F (1,371°C).
- Uses: Bridges (e.g., 1.5 million tons in the Golden Gate Bridge), car chassis.
- Challenges: Increased carbon content (greater than 0.3%) may produce hardening and cracking; rusts when left unprotected.
- Best Technique: MIG using 75% argon/25% CO2 shielding gas for penetration, stick welding using 6010 electrodes for deep joints.
Stainless Steel
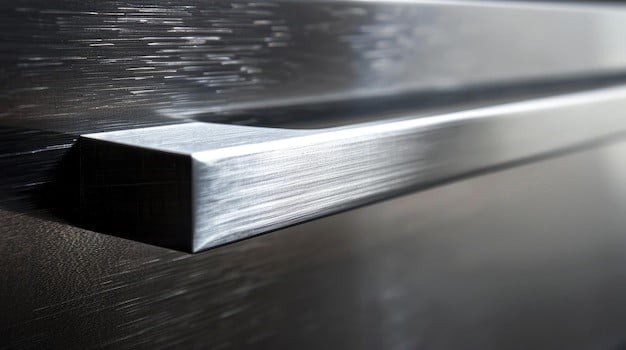
- Properties: Chromium (10-20%) prevents rust, melting point ~2,750°F (1,510°C), density 7.9 g/cm³.
- Uses: Surgical tools, exhaust systems (resists 1,200°F heat).
- Challenges: Thermal expansion (17.3 µm/m·K) warps; precipitation of chromium carbide degrades corrosion resistance if overheated.
- Best Technique: TIG using pure argon, 2% thoriated tungsten electrode for precision on 0.5-3 mm thicknesses.
Related article: How to Weld 316 Stainless Steel
Aluminum
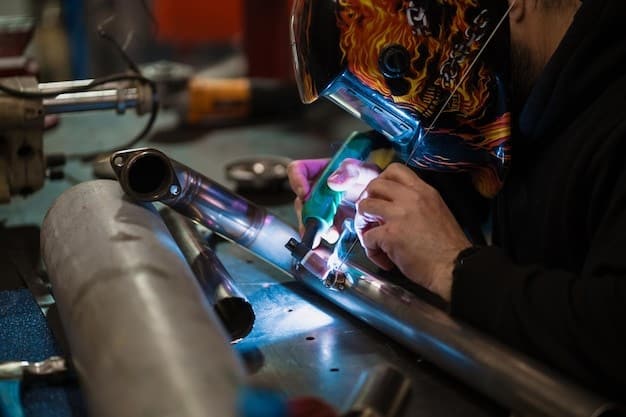
- Properties: Light (2.7 g/cm³), conducts heat at 237 W/m·K, melts at 1,221°F (660°C).
- Uses: Aircraft fuselages (saves 20% of steel’s weight), boat hulls.
- Challenges: Oxide layer (melts at 3,700°F) inhibits fusion; rapid loss of heat causes thin sheets to warp.
- Best Technique: MIG using pulsed current for 3-6 mm stock; TIG using AC polarity to fracture oxide on 1-2 mm sheets.
Copper
- Properties: Conductivity of 401 W/m·K, density 8.96 g/cm³, melting point 1,984°F (1,085°C).
- Uses: Power cables (transfers 97% of pure copper’s conductivity), heat exchangers.
- Challenges: Oxidizes at temperatures above 400°F, requires 100% argon shield; overheated heat input produces burn-through.
- Best Technique: TIG using DCEN polarity, copper filler rod for 2-5 mm joints.
Titanium
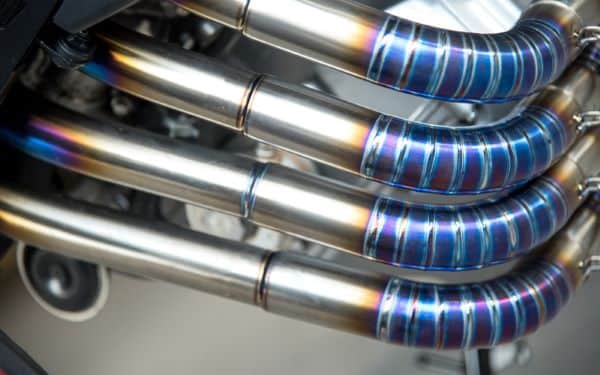
- Properties: Strength-to-weight ratio of 450 MPa at 4.5 g/cm³, melts at 3,034°F (1,668°C).
- Uses: Jet engine blades (resists 1,000°F), bone screws (biocompatible).
- Challenges: Picks up oxygen at temperatures higher than 600°F, becomes brittle; needs complete inert gas coverage.
- Best Technique: TIG with 99.99% argon, trailing shield for 1-3 mm welds.
Magnesium
- Properties: Lightest structural metal (1.74 g/cm³), melts at 1,202°F (650°C), tensile strength ~30,000 psi.
- Uses: Racecar wheels (33% lighter than aluminum), drone frames.
- Challenges: Ignites at 883°F (473°C), producing bright white flames; porosity from hydrogen absorption.
- Best Technique: TIG with AC, helium-argon mix (70/30) for better penetration on 2-4 mm.
Nickel Alloys
- Properties: Melting range 2,550-2,650°F (1,399-1,454°C), density ~8.9 g/cm³, resists 1,800°F corrosion.
- Uses: Turbine blades, chemical reactors (capable of withstanding sulfuric acid).
- Challenges: Hot cracking in high-nickel alloys (e.g., Inconel 718); low welding speeds necessary.
- Best Technique: TIG with DCEN, nickel filler for 3-6 mm; plasma arc for precision in automated processes.
Brass
- Properties: 60% copper/40% zinc, melts at 1,650°F (899°C), density 8.4 g/cm³.
- Uses: Ornamental railings, musical instruments.
- Challenges: Zinc boils off at 1,665°F, leaving porous welds; fumes irritate lungs.
- Best Technique: Low amp TIG (50-80A) with silicon bronze filler; brazing as alternative.
Unweldable Metals: Why Some Materials Don’t Work
Some metals won’t weld due to physics or safety issues:
- Lead: Melt point 787°F (419°C), vapor point 1,665°F (907°C), forms brittle, hole-ridden joints.
- Zinc: Liquefies at 787°F (419°C), vaporizes at 1,665°F (907°C), leaving brittle, hole-riddled joints.
- Mercury: Liquid at -38°F (-39°C), evaporates at 674°F (357°C)—impossible to weld.
For these, brazing (e.g., lead at 600°F with flux) or mechanical fastening is best.
Safety Alert: Welding galvanized steel releases zinc oxide fumes, leading to “metal fume fever” (flu-like symptoms for 24-48 hours).
Welding Techniques for Different Welding Metals
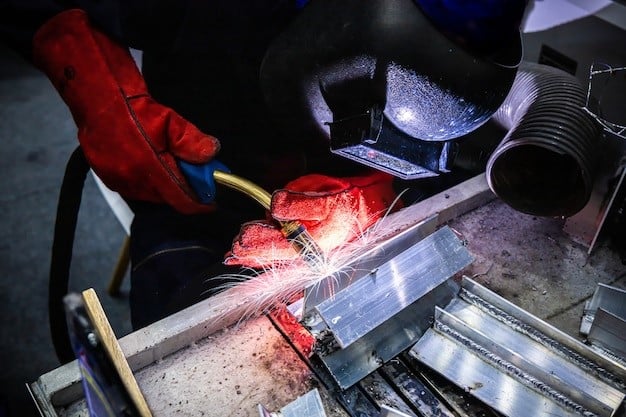
Technique selection based on metal characteristics and project requirements.
MIG Welding
MIG welding machines are best for welding steel (up to 10 mm) and aluminum (3-6 mm).
- Details: Uses a continuous wire feed at 200-400 amps, gas mix of 75% argon/25% CO2.
- Fact: Deposits 2-8 lbs of weld metal per hour—fastest common method.
- Tips: Use 0.035-inch wire for steel, 0.045-inch for aluminum; clean slag after each pass.
TIG Welding
TIG welding machines are best for weldingsteel (10 mm or less) and aluminum (3-6 mm).
When using TIG welding,work on continuous wire feed of 200-400 amps, gas blend of 75% argon/25% CO2. Uses 2-8 lbs of weld metal per hour—fastest most popular process.
Tips: Tungsten should be sharpened to 20° for thin metal; use foot pedal to manage heat.
Stick Welding
Began in 1888, stick welding is the oldest arc welding process still operational. A stick welding machine is best for welding steel (4-20 mm) and cast iron outdoors.
- Details: 6011 electrodes at 80-120 amps pierce rust; flux covers weld pool.
- Tips: Strike arc like a match; maintain 1/8-inch gap to avoid sticking.
Laser Welding
- Best For: Thin metals (0.1-1 mm), nickel alloys.
- Details: 2025 tech uses 1-10 kW fiber lasers, welds at 0.5-5 m/min speeds.
- Fact: Heat-affected zone is 50% smaller than TIG, reducing distortion.
- Tips: Requires clean surfaces; optimum for automated manufacturing lines.
Pre- and Post-Welding Best Practices
Weld quality starts before the arc and ends after it cools.
Pre-Weld Prep
- Cleaning: Wipe aluminum with acetone, stainless with a special brush (prevents cross-contamination).
- Joint Design: Use 60° V-groove for steel over 6 mm; lap joints for thin titanium.
- Heat Control: Preheat copper to 300°F (149°C) with a torch to reduce thermal shock.
Post-Weld Care
- Stress Relief: Heat steel to 1,100°F (593°C) for 1 hour per inch of thickness, then slow-cool.
- Inspection: Dye penetrant test shows cracks in aluminum (visible under UV light).
- Cooling: Quench copper in water from 1,000°F (538°C) to lock in conductivity.
Safety Considerations by Metal
Welding risks vary by metal types. For example, zinc oxide from galvanized steel exceeds OSHA’s 5 mg/m³ limit in 10 minutes without ventilation.
Magnesium burns at 5,600°F (3,093°C) and should not be fought with water—use dry sand.
To achieve safe welding process, welding helmets with shade 10-13 lenses protect 99.9% of UV; leather aprons resist 1,000°F sparks.
Conclusion
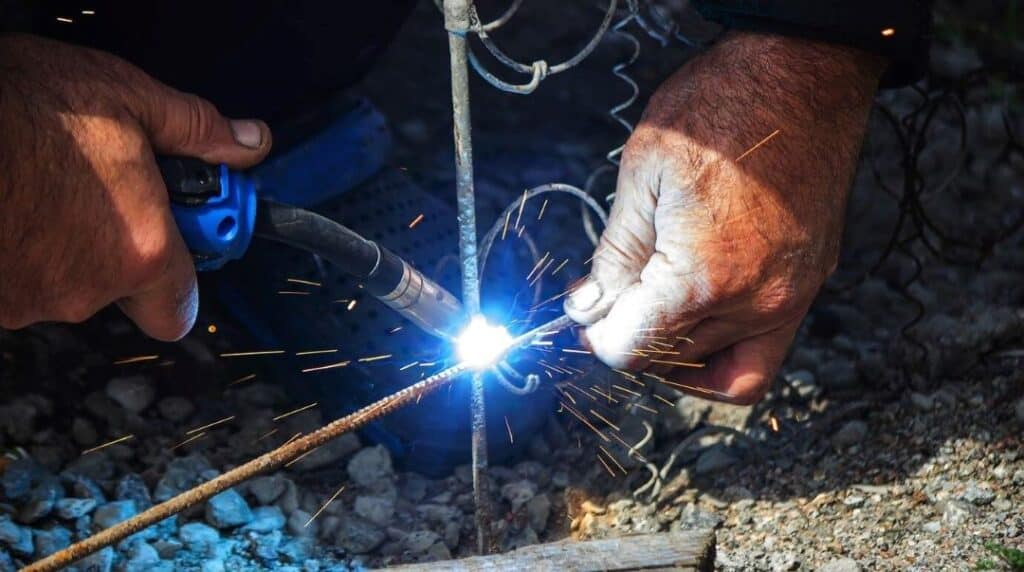
Welding metal is a fusion of science and artistry, from steel’s rugged strength to titanium’s aerospace precision. With good technique—whether MIG’s speed or laser’s fineness—and shrewd practices, the welds can hold up to toughest demands. Learn more with our or test your metal mettle below.
FAQs About Welding Metals
Which metal is easiest to weld for beginners?
Mild steel (0.2% carbon) is easiest to weld, especially with stick or MIG welding. It can tolerate some surface rust, does not require much heat control, and is cheap.
Can different metals be welded together?
Yes, but with special methods. For example, steel to stainless uses 309L filler, while aluminum to steel may use bimetallic transition strips and TIG welding.
Why do some metals crack after welding?
Cracking typically results from high carbon content, poor heat control, or lack of pre/post-heat treatment. Cast iron and high-carbon steel are especially susceptible to cracking.
Is aluminum harder to weld than steel?
Yes. Aluminum’s oxide coating, conductivity, and low melting point make it more difficult. TIG welding with AC polarity helps to break the oxide for a clean weld.
What’s the best welding method for stainless steel?
TIG welding produces the cleanest, most controlled outcome with stainless, especially thin gauges. It prevents distortion and corrosion resistance. Related article: Exploring Types of Stainless Steel Welding.
Why is titanium so hard to weld?
Titanium is not contaminated by oxygen at elevated temperatures. It requires full shielding in argon, including a tailing shield, and extremely clean surroundings.