Choosing the right welding power supply can be challenging for beginners and professionals. With various welding techniques and machines available, the wrong selection may lead to poor weld quality, increased downtime, and inefficiency. The solution lies in understanding the specific requirements, such as the material to be welded, duty cycle, and power source compatibility. By carefully evaluating these factors, you can select a welding power supply that maximizes productivity and delivers superior welding results, ensuring optimal performance in every welding task.
What Is Welding Power Supply
A welding power supply provides the electrical energy to create and maintain the welding arc. It converts electrical power into a usable form, allowing the welder to control the heat and intensity of the welding process. There are various types of power supplies, such as alternating current (AC) and direct current (DC), each suited for different welding techniques and materials. The choice of power supply significantly impacts the quality and efficiency of the weld, making it essential to select the appropriate one for each task.
Electrical Concepts in Welding
Understanding key electrical concepts is essential for effective welding. Here are some important concepts to consider:
- Current (AC/DC): Welding uses either alternating current (AC) or direct current (DC). AC reverses direction periodically, while DC flows in one direction, offering more stability.
- Voltage: Voltage is the force that drives the current through the welding circuit. Higher voltage can produce a stronger arc, impacting weld quality.
- Polarity: In DC welding, polarity affects heat distribution. Positive polarity generates more heat at the workpiece, while negative polarity directs heat towards the electrode.
- Duty Cycle: This is how long a welder can operate within ten minutes before cooling down. A higher duty cycle means more continuous welding.
- Amperage Range: The range of current available for welding. Higher amperage is used for thicker materials, while lower amperage is for thinner metals.
- Open Circuit Voltage is when the welding machine is on, but no arc is created. Higher open circuit voltage can help initiate the arc more easily, especially in difficult conditions.
Welding Power Supply Types
Different types of welding power supplies offer distinct advantages depending on the type of welding and specific job requirements. Understanding the characteristics of each type is essential to selecting the right tool for your welding tasks. Below is a detailed explanation of four common types of welding power supplies: transformer-based, inverter-based, engine-driven, and hybrid.
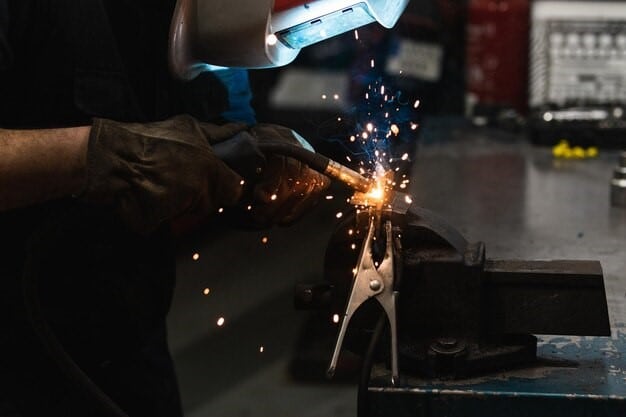
Transformer-Based Power Supplies
Transformer-based power supplies are one of the oldest and most reliable forms of welding equipment. They convert high-voltage, low-current electrical energy into a usable form for welding by reducing voltage and increasing current. These machines are known for their durability and ability to handle heavy-duty tasks, making them ideal for industrial settings. Transformer-based systems work primarily with alternating current (AC), which is suitable for large-scale projects and thick materials like structural steel welding.
Pros
- They can handle high currents, making them suitable for thick materials and heavy-duty welding tasks.
- Durable and reliable, designed to last for years in tough environments.
- Easy to maintain due to their simplistic design.
Cons
- Large and heavy, which limits portability, making them impractical for on-site or mobile work.
- Less energy-efficient compared to modern power supplies, leading to higher operational costs.
Inverter-Based Power Supplies
Inverter-based power supplies are a newer technology that uses electronic components to convert power. Unlike transformer-based systems, inverter welders are lightweight and highly efficient, providing more control over welding parameters. They can convert alternating current (AC) and direct current (DC), offering more versatility in welding applications. Their small size and portability make them popular for mobile welding tasks or workshops with limited space.
Pros
- They are lightweight and portable, making them suitable for workshops and fieldwork.
- Energy-efficient, reducing power consumption and operational costs.
- Provides precise control over welding parameters, leading to better weld quality.
Cons
- Higher upfront cost due to advanced technology.
- More complex design, making maintenance and repairs more expensive.
Engine-Driven Power Supplies
Engine-driven power supplies are independent units powered by internal combustion engines, perfect for remote or off-grid welding operations. These machines do not rely on an external power source, which allows welders to work in locations where electrical power is unavailable. They are widely used in construction, pipeline welding, and other outdoor applications where mobility and independence from grid power are critical.
Pros
- Independent of electrical power, making them ideal for remote or off-grid projects.
- Versatile and can be used for a variety of outdoor applications.
- Provides consistent power output for long-duration tasks.
Cons
- Requires a steady fuel supply, increasing operational costs.
- Heavier and bulkier than inverter-based welders, limiting mobility.
Hybrid Power Supplies
Hybrid power supplies combine features of both engine-driven and inverter-based systems, offering flexibility for diverse welding applications. These machines can switch between engine-driven power and electricity from the grid, providing portability and adaptability. This makes them ideal for welders who frequently work in different environments, such as construction sites and workshops.
Pros
- Offers flexibility by allowing switching between engine-driven and grid power.
- Suitable for diverse welding tasks, including both AC and DC welding.
- Portable, allowing welders to move between job sites easily.
Cons
- Higher cost due to its advanced, multifunctional design.
- More complex maintenance requirements lead to increased repair costs.
Comparison of Welding Power Supply Types
Power Supply Type | Description | Pros | Cons |
Transformer-Based | Converts high-voltage, low-current electrical energy into usable welding power | Handles high currents for thick materials; Durable and long-lasting; Simple maintenance; Suitable for heavy-duty tasks | Heavy and not portable; Less energy-efficient |
Inverter-Based | Uses advanced electronic components for efficient power conversion | Lightweight and portable; Energy-efficient; Precise control; Versatile for various applications | Higher initial cost; Complex maintenance |
Engine-Driven | Powered by an internal combustion engine, ideal for remote locations | Independent from external power sources; Great for outdoor use; Consistent power output | Requires fuel; Heavier than inverter systems |
Hybrid Power Supply | Combines engine-driven and inverter technology for flexibility | Flexible for different welding tasks; Works with multiple power sources; Portable and adaptable | Expensive; Complicated maintenance |
Choosing the Right Welding Power Supply
Selecting the right welding power supply involves considering several important factors. The input power is crucial in determining whether your equipment can operate effectively with the available electricity.
Input Power
Input power is a critical factor in selecting a welding power supply. It depends on the electrical setup available where you will be working. Industrial environments may provide high-voltage outlets, whereas home workshops typically offer lower voltage. Ensuring that the power supply matches the available power is crucial to prevent damage and ensure efficiency.
Material Thickness
The thickness of the material being welded determines the amount of current required. Thicker materials need more amperage for deep penetration, while thinner materials require less to avoid overheating and burn-through.
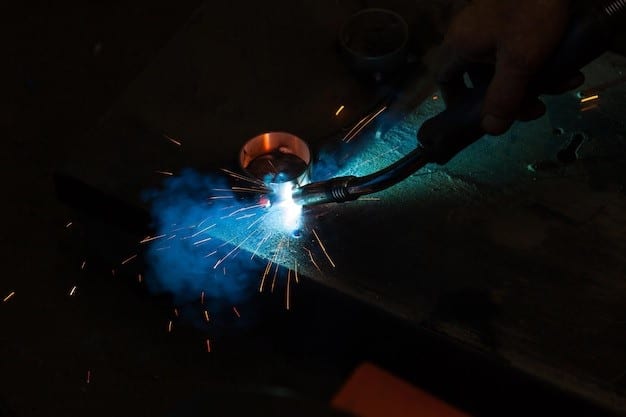
Duty Cycle
The duty cycle refers to the time the welder can operate within a 10-minute before needing to cool down. Choosing a machine with a higher duty cycle is necessary for projects requiring continuous welding to avoid downtime and maintain productivity.
Cost vs. Performance
Balancing cost with performance is vital. While high-end models offer advanced features, they can be expensive. Assessing your welding needs and budget is essential to find a power supply that offers the best performance without overspending. Selecting a power supply with the right features for your work will ensure good value and long-term efficiency.
Key Factors for Choosing a Welding Power Supply
Factor | Description | Recommendation |
Input Power | Voltage compatibility with available power sources | Choose based on your workshop’s voltage; industrial settings need higher input power. |
Material Thickness | Determines the amperage required for welding different thicknesses of metal | Thicker materials need high amperage (choose transformer or hybrid systems). |
Duty Cycle | The time a welder can operate continuously before needing to cool down | High duty cycle is recommended for long continuous welding tasks. |
Cost vs. Performance | Balancing budget with performance and features | For frequent, professional use, invest in inverter or hybrid systems. |
Welding Techniques and Power Supply Types
Stick Welding
Stick welding, also known as Shielded Metal Arc Welding (SMAW), is a versatile technique commonly used in construction and repair work. It utilizes a consumable electrode covered in flux to create the weld. This method can be performed in various conditions, including outdoors and on dirty surfaces, making it highly adaptable.
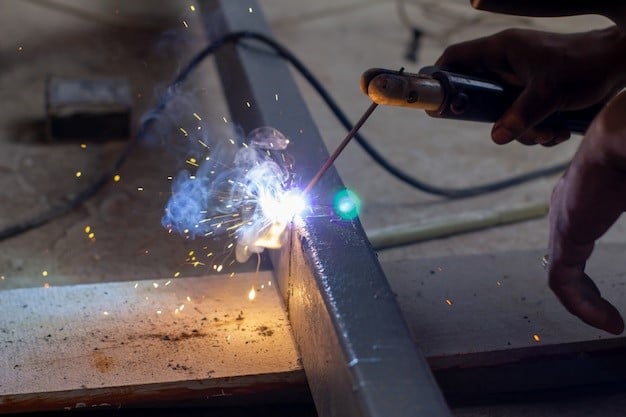
MIG Welding
Metal Inert Gas (MIG) welding is also known as Gas Metal Arc Welding (GMAW). The MIG welder uses a continuous MIG welding wire fed through the welding gun. It produces clean welds and is ideal for thin metals. MIG welding is user-friendly, making it a popular choice for beginners and large-scale production.
TIG Welding
Tungsten Inert Gas (TIG) welding, called Gas Tungsten Arc Welding (GTAW), is a precision welding technique. The TIG welder uses a non-consumable tungsten electrode and requires greater skill but produces high-quality welds, particularly for stainless steel and aluminum.
Flux-Cored Arc Welding (FCAW)
FCAW is similar to MIG welding but uses a flux-cored wire instead of solid wire. This technique is preferred for outdoor or industrial settings due to its higher deposition rate and ability to handle thicker materials. It is ideal for large-scale projects requiring faster welding speeds.
Final Thoughts
Choosing the right welding power supply and welding equipment supplier is crucial for ensuring successful welding outcomes, whether you’re working on small repairs or large industrial projects. You can select a power supply that matches your needs by understanding input power, material thickness, and duty cycle. Additionally, knowing the pros and cons of each power supply type helps you make informed decisions. Ultimately, the right choice will improve efficiency, reduce downtime, and ensure high-quality welds, contributing to overall productivity and performance in any welding task.
FAQs
What type of welding power supply is best for beginners?
Inverter-based power supplies are generally recommended for beginners due to their lightweight design, energy efficiency, and ease of use.
What power supply is needed for welding thick materials?
Transformer-based power supplies are ideal for welding thicker materials, providing high current and deep penetration.
How do I determine the duty cycle for my welding machine?
The duty cycle is often indicated on the welder and refers to how long you can weld in 10 minutes before cooling is needed.
Can I use the same power supply for multiple welding techniques?
Yes, hybrid or inverter-based power supplies can support multiple techniques such as MIG, TIG, and Stick welding, offering versatility for various projects.