Welding technology has advanced rapidly, addressing the challenge of meeting modern industry demands for precision, speed, and safety. Traditional welding methods often struggle to produce consistent results, especially in complex projects. This inconsistency can lead to inefficiencies, higher costs, and safety risks. However, these challenges are being overcome with innovations such as AI-driven welding, automation, and digitalization.
These new technologies enhance precision, reduce human error, and streamline workflows. The impact of these advancements extends across industries, from automotive to aerospace, creating opportunities for skilled welders while ensuring better quality and cost-effectiveness.
Recent Innovations in Welding Technology
Automated and Robotic Welding
Automation in welding has significantly improved the efficiency and accuracy of various tasks. Robotic systems are widely used in industries to handle repetitive welding jobs, reducing human error and increasing productivity. These robots can precisely perform complex welds, making them essential in sectors like automotive and aerospace.
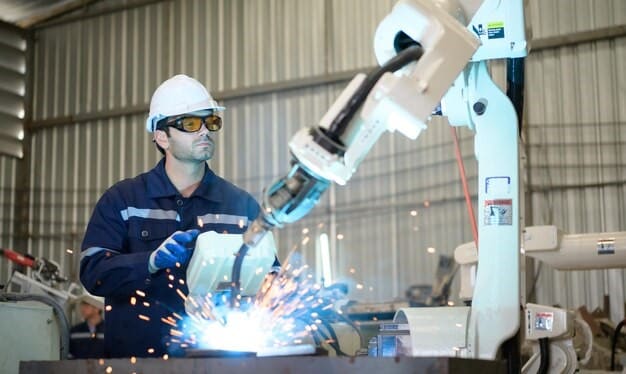
AI-Driven Welding
Artificial Intelligence (AI) has revolutionized welding by enhancing robotic systems with smart features. AI-driven welding machines can learn from data, adjust to varying conditions, and improve the quality of welds. This technology minimizes errors and allows more complex welding projects to be completed faster and more precisely.
Hybrid Welding
Hybrid welding combines different welding processes, such as laser and arc welding, to leverage the strengths of each method. This approach improves the speed of production and ensures stronger, higher-quality welds. Hybrid techniques are becoming more popular, particularly in industries where precision and strength are critical, such as shipbuilding and heavy machinery manufacturing. These innovations are transforming the welding industry, making processes faster, safer, and more reliable.
Advancements in Welding Equipment and Techniques
Smart Welding Machines
Smart welding machines have redefined the welding landscape by incorporating automation and digital control systems. Welding machine suppliers equip these machines with sensors and advanced control systems that adjust parameters in real time to ensure weld quality. They offer improved accuracy, reduce human error, and increase production speed, crucial for industries requiring high precision, like aerospace and automotive manufacturing.
Key Features
- Automated adjustments for temperature, current, and speed.
- Integrated monitoring systems for quality control.
- Increased efficiency through real-time feedback.
New Welding Consumables
Welding consumables such as tungsten welding electrodes, filler metals, and fluxes have also seen significant advancements. New materials are designed to improve weld strength, reduce waste, and enhance ease of use. These consumables are tailored for specific applications, ensuring a more precise and consistent outcome, especially in critical industries like shipbuilding and pipeline construction.
Improvements in Consumables
- Longer-lasting electrodes for higher productivity.
- Eco-friendly materials that reduce harmful emissions.
- Consumables are designed for specific materials like aluminum and stainless steel.
Advanced Welding Techniques
Technological advancements have brought forth innovative welding methods that cater to modern industry requirements for stronger and more reliable welds.
- Laser Welding: Utilizes concentrated light beams to create precise and clean welds. It is used in industries that require intricate detailing, such as electronics and medical equipment manufacturing. Laser welding offers high-speed operations with minimal heat distortion.
- Friction Stir Welding (FSW): This solid-state process joins materials by applying pressure and friction, producing defect-free welds without melting the base materials. It is widely used in the aerospace and automotive industries for aluminum structures.
- Cold Metal Transfer (CMT) Welding: This method reduces spatter and heat input by separating droplet transfer and wire movement. It is ideal for thin materials and applications where heat distortion, such as automotive and sheet metal welding, must be minimized.
Smart Welding
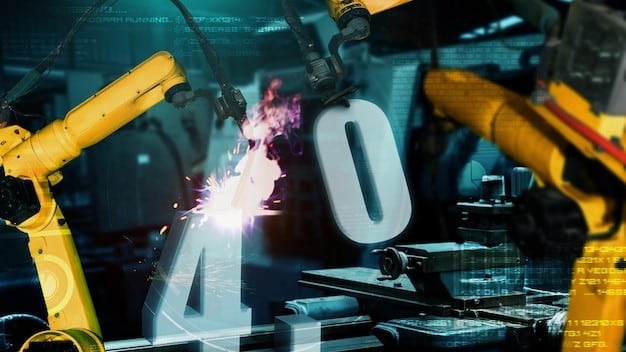
Smart welding is a significant advancement in the industry, integrating cutting-edge technology to enhance efficiency, precision, and safety. Industry 4.0, characterized by smart machines and interconnected systems, reshapes welding processes. With smart welding systems, real-time data is collected and analyzed to optimize parameters, improve weld quality, and reduce material waste. These technologies offer enhanced monitoring and automation, resulting in fewer defects and improved productivity.
Cobots, or collaborative robots, are another crucial innovation in smart welding. These robots work alongside human welders to perform repetitive or dangerous tasks. Cobots are designed to be user-friendly, flexible, and safe, making them ideal for small to medium-sized enterprises aiming to improve efficiency without sacrificing worker safety.
Benefits of Cobots in Welding
- Perform repetitive tasks, allowing humans to focus on complex welds.
- Enhanced safety by reducing direct exposure to welding hazards.
- Easy to integrate into existing welding processes.
Sustainable Welding
Sustainable welding focuses on reducing the environmental impact of welding processes while maintaining efficiency and quality. Green welding practices aim to minimize energy consumption, lower emissions, and reduce waste. These practices are essential for industries looking to reduce their carbon footprint and meet environmental regulations. One way to achieve this is by using energy-efficient welding equipment, which consumes less power while maintaining high performance.
Another approach to sustainable welding is adopting materials and methods that reduce harmful emissions. For instance, using welding consumables with lower fume emissions helps improve air quality in the workspace and reduces environmental pollution. Also, cold metal transfer (CMT) and laser welding generate less heat and spatter, decreasing energy use and waste.
Benefits of Green Welding
- Reduced energy consumption and operational costs.
- Lower emissions, contributing to cleaner air.
- Less material waste, promoting sustainability.
Ways to Implement Sustainable Welding
- Use energy-efficient welding machines.
- Select eco-friendly consumables with lower emissions.
- Implement advanced welding techniques that reduce waste.
Comparison of Advanced Welding Techniques
Technique | Key Features | Applications |
Laser Welding | Precise, minimal heat distortion | Electronics, medical equipment |
Friction Stir Welding | Strong, defect-free welds | Aerospace, automotive, shipbuilding |
Cold Metal Transfer | Low spatter, minimal heat input | Automotive, thin material welding |
Hybrid Welding | Combines laser and arc welding | Construction, heavy machinery manufacturing |
Welding Safety Advancements
Augmented Reality (AR) Welding Training
Augmented Reality (AR) is transforming welding training by creating virtual environments where welders can practice without the risks associated with real-world welding. These systems allow welders to hone their skills in a safe and controlled space, minimizing the likelihood of accidents during on-the-job training. AR training helps improve accuracy and technique, preparing welders for complex tasks without exposing them to physical dangers.
Welding PPE
Personal Protective Equipment (PPE) is crucial in welding safety. Advances in welding helmets, such as auto-darkening filters, protect welders’ eyes from harmful light emissions while maintaining visibility. Additionally, improvements in flame-resistant clothing, welding gloves, and boots offer better protection from heat, sparks, and molten metal, reducing the risk of burns and other injuries.
Fume Extraction Systems
Fume extraction systems are essential in modern welding environments. These systems efficiently capture and remove toxic fumes and particulates produced during welding, preventing workers from inhaling them. By improving air quality, fume extraction systems significantly reduce health risks such as respiratory issues and long-term exposure to harmful substances.
Applications and Challenges of New Welding Technology
Automotive Industry
The automotive industry has greatly benefited from advancements in welding technology. With the rise of electric vehicles and the need for lightweight materials, innovative welding methods such as laser welding and friction stir welding have become essential. These technologies allow for the precise joining of dissimilar materials like aluminum and steel, which is critical for creating fuel-efficient and safe vehicles. Robotic and automated welding systems are also widely used to ensure consistency and reduce production times.
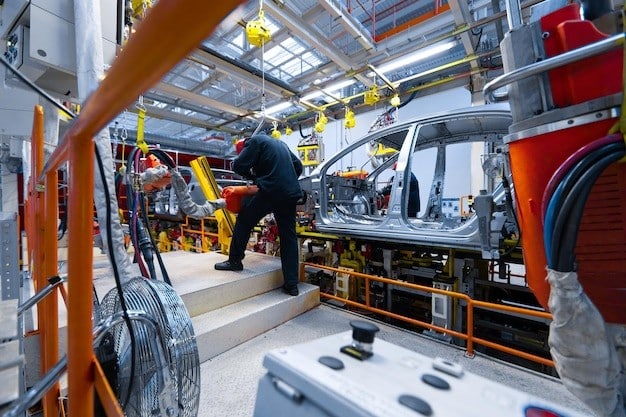
Aerospace Industry
In aerospace, precision and strength are paramount. Welding advancements, such as cold metal transfer (CMT) and hybrid welding, have made it possible to create lightweight yet durable components. These techniques help produce aircraft parts, ensuring structural integrity while reducing the aircraft’s weight. Laser welding is frequently used in assembling fuselages and critical engine parts due to its precision and minimal heat distortion.
Construction and Infrastructure
The construction industry relies on advanced welding technologies for building strong, resilient structures. Techniques like friction stir welding are used for creating bridges and high-rise buildings, while automation helps streamline large-scale construction projects. With the introduction of smart welding systems, welders can now monitor processes in real-time, improving safety and reducing the likelihood of structural failures.
Energy Sector
In the energy sector, welding innovations are crucial in constructing pipelines, wind turbines, and solar energy systems. These technologies ensure the efficient and reliable production of components that can withstand harsh environments, such as deep-sea oil rigs and renewable energy installations.
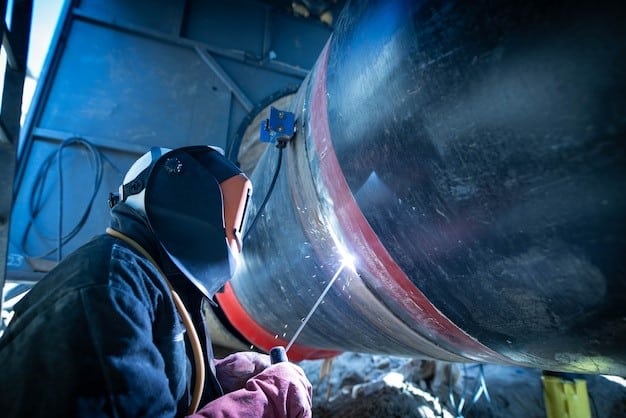
Comparison of Welding Applications Across Industries
Industry | Welding Technologies Used | Specific Applications |
Automotive | Robotic Welding, Laser Welding | Joining lightweight materials, assembly of electric vehicles |
Aerospace | Friction Stir Welding, Laser Welding | Manufacturing aircraft fuselage, engine components |
Construction | Hybrid Welding, Automation | Building structures, bridges, and high-rise buildings |
Energy (Oil, Gas, Renewables) | Cold Metal Transfer, Laser Welding | Pipeline construction, wind turbine assembly, solar systems |
Challenges in Implementing New Welding Technologies
Despite the numerous benefits, adopting new welding technologies poses several challenges:
- High Costs: Advanced welding systems and equipment are often expensive, making it difficult for smaller companies to adopt them.
- Skill Gaps: Introducing technologies like AI-driven welding requires specialized skills, leading to a shortage of skilled workers.
- Integration Issues: Implementing new systems into existing production lines can be complex and time-consuming.
- Maintenance: Advanced systems may require frequent maintenance and updates, increasing operational costs.
- Resistance to Change: Workers and companies may hesitate to adopt new methods, preferring traditional techniques over unfamiliar technology.
Future Trends in Welding Technology
Innovations drive the future of welding technology to enhance efficiency, precision, and sustainability. One significant trend is the increased adoption of artificial intelligence (AI) and machine learning. AI-powered welding machines are improving by learning from data, adapting to various conditions, and reducing errors. This makes welding faster and more accurate while minimizing material waste.
Another trend is the growing use of cobots (collaborative robots) in welding. Cobots work alongside human welders, improving efficiency while allowing for greater safety. These robots are becoming more user-friendly and affordable, making them ideal for small and medium-sized businesses.
Sustainability is also becoming a key focus, with the rise of green welding practices to reduce energy consumption and emissions. Techniques like laser welding and cold metal transfer (CMT) are refined to lower environmental impact while maintaining high-quality welds.
Lastly, integrating smart welding systems within the Industry 4.0 framework will continue to grow. These systems provide real-time data analysis, predictive maintenance, and process optimization, which are vital for industries requiring consistent high-performance welding.
FAQs
What are the key benefits of automated and robotic welding?
Automated and robotic welding enhances precision and speed, reduces human errors, and allows welders to focus on complex tasks. These technologies are commonly used in industries like automotive and aerospace for their reliability and efficiency.
How does AI-driven welding improve welding processes?
AI-driven welding adapts to real-time data, optimizing parameters and reducing errors. It speeds up the welding process while maintaining high-quality welds, especially in industries that require precision.
What is green welding, and why is it important?
Green welding focuses on reducing emissions and energy consumption through techniques like laser welding and cold metal transfer (CMT), promoting sustainability without compromising weld quality.
What are the challenges in adopting new welding technologies?
High costs, skill gaps, and integration difficulties are common challenges when adopting new welding technologies, especially for smaller businesses or traditional industries.