Choosing the right welding wire is critical for ensuring the quality and durability of welds. Many welders face poor weld strength, excessive spatter, and post-weld cleanup, which stem from improper wire selection. The solution lies in understanding the different types of welding wires and their specific applications.
By selecting the appropriate wire, welders can achieve better weld quality, reduce rework, and increase productivity. This guide aims to provide comprehensive information on commonly used welding wires in MIG welding and Flux-Cored Arc Welding (FCAW), helping welders make informed decisions.
MIG Welding Wires
These wires are essential for achieving strong, clean welds in various applications. MIG welding wire suppliers often provide different types and classifications based on material composition and intended use. Understanding the classifications helps select the right wire for specific welding tasks, ensuring optimal performance and weld quality.
Aluminum Welding Wire
Aluminum welding wires are used to weld aluminum and its alloys. Two common types are ER4043 and ER5356.
ER4043
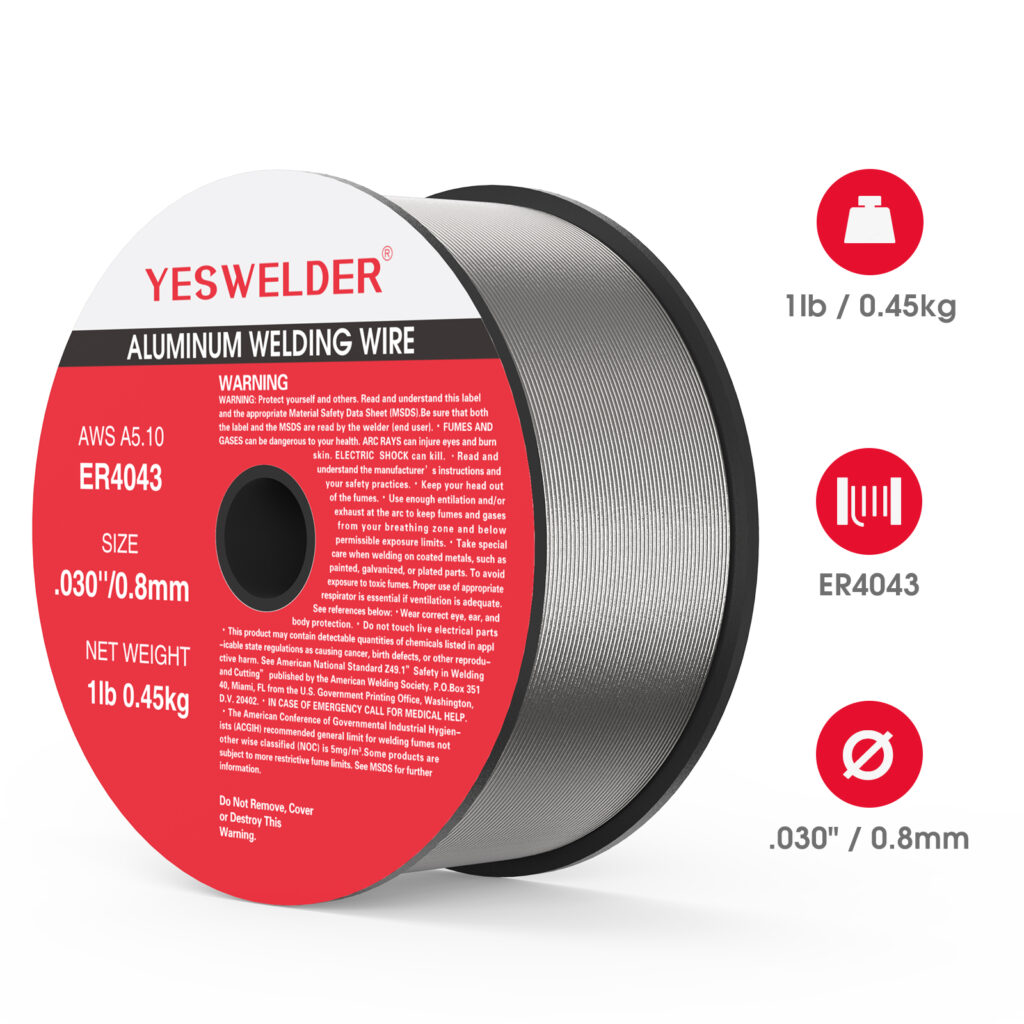
ER4043 is a popular choice for welding heat-treated aluminum alloys. Its high silicon content provides good wetting action, resulting in smooth, aesthetically pleasing welds. This wire is typically used in the automotive and aerospace industries and for welding cast aluminum parts. Its good fluidity makes it suitable for welding thin and thick aluminum sections.
ER5356
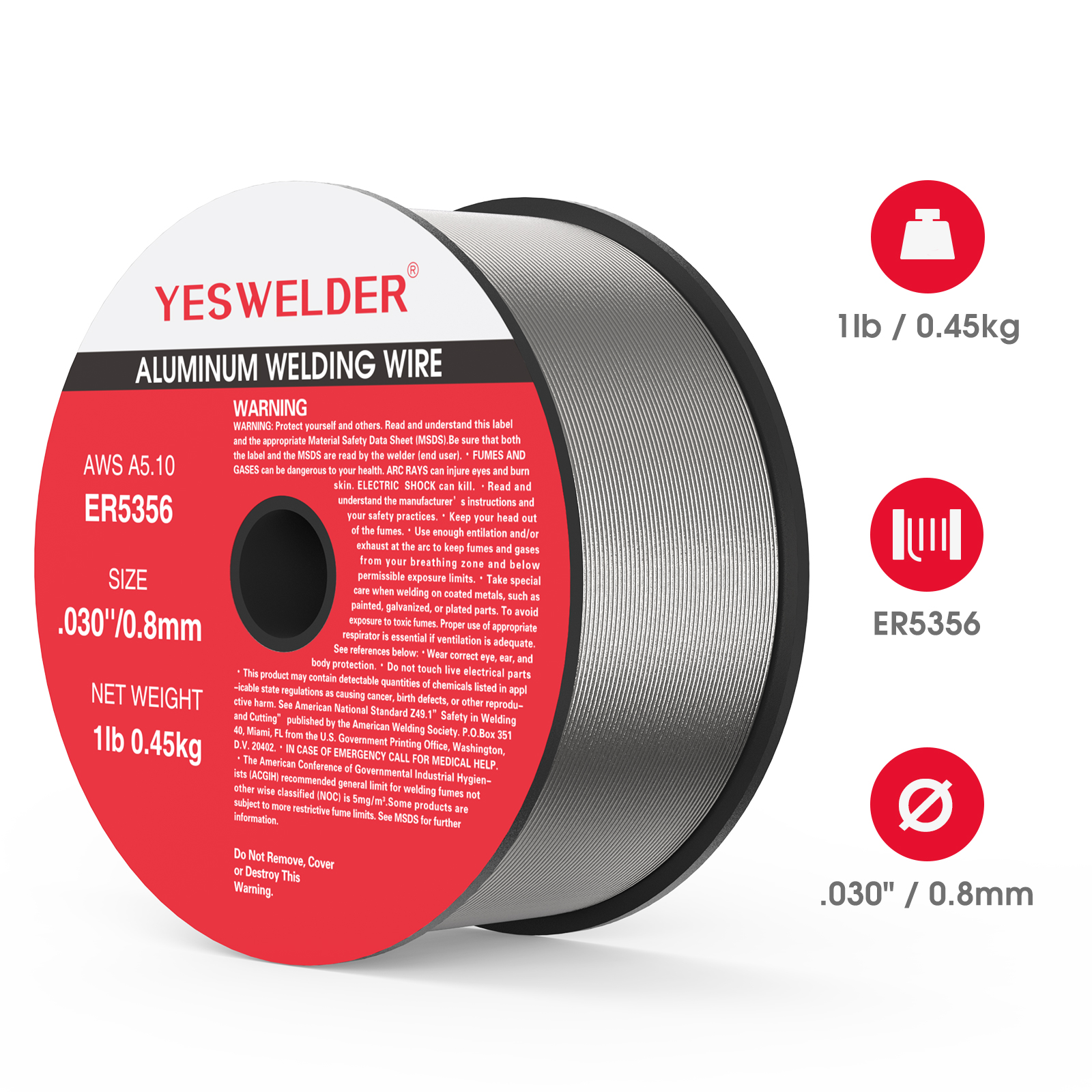
ER5356 is another widely used aluminum welding wire. It contains 5% magnesium, providing higher strength and better corrosion resistance than ER4043. This makes ER5356 ideal for marine applications and structures exposed to harsh environments. The wire is also used in welding bicycles, trucks, and pressure vessels. ER5356 is known for producing strong, durable welds and is compatible with a wide range of aluminum alloys.
Stainless Welding Wire
Stainless steel welding wires are used for welding different grades of stainless steel. They are chosen based on the specific alloy being welded and the required properties of the weld.
ER308/308L
ER308/308L is a widely used stainless welding wire designed for welding 304 and 304L grade stainless steels. The low carbon content of ER308L helps prevent carbide precipitation, which can cause intergranular corrosion. This wire provides good corrosion resistance and is commonly used in the food and beverage industry and chemical equipment.
ER309
ER309 is used for welding dissimilar metals, such as joining stainless steel to carbon steel. Its higher chromium and nickel content provides strength and increased resistance to oxidation, making it suitable for welding heat-resistant stainless steels and for applications exposed to high temperatures.
ER316
ER316 welding wire is used for welding 316-grade stainless steel. It contains molybdenum, which enhances corrosion resistance, particularly against chlorides and other industrial solvents. This wire is often used in marine environments, chemical plants, and other areas requiring strong corrosion resistance.
Welding Wire for Cast Iron
Welding cast iron requires special wires to handle the material’s brittleness and unique properties.
ERNi55
ERNi55 is a nickel-based welding wire used for welding cast iron. It provides excellent machinability and produces strong, crack-resistant welds. This wire is often used to repair cast iron components and to join cast iron to other materials.
ErNi-Fe-CI
ErNi-Fe-CI is another nickel-based wire specifically designed for cast iron. It offers good weldability and machinability, making it ideal for repairing cast iron parts and applications requiring high strength and toughness. This wire can also be used for welding cast iron to steel.
Welding Wire for Copper
Copper welding wires are used to weld copper and copper alloys. They are designed to handle copper’s unique properties, such as its high thermal conductivity and electrical properties.
ERCu
ERCu is a copper welding wire used primarily for welding deoxidized copper. It contains a small amount of phosphorus, which helps improve fluidity and reduce oxidation during welding. This wire is often used when electrical conductivity is crucial, such as in electrical components and conductive parts. ERCu provides excellent corrosion resistance and is suitable for welding copper pipes, tanks, and other copper structures.
ERSiCu
ERSiCu is another copper welding wire that contains silicon to enhance its weldability and mechanical properties. This wire is used for welding copper-silicon alloys and offers improved strength and fluidity. ERSiCu is commonly used in applications requiring high strength and good electrical conductivity. It is suitable for welding copper components in the automotive and construction industries, where durability and performance are essential.
Filler Wire for Nickel Alloys
Nickel alloy welding wires are designed for welding nickel and nickel-based alloys. These wires are used in applications that require high strength, corrosion resistance, and heat resistance.
ERNiCr-3 Nickel Alloy 82
ERNiCr-3 is a nickel-chromium welding wire for welding nickel alloys and dissimilar metals. It is known for its excellent resistance to high-temperature oxidation and corrosion. This wire is commonly used in the aerospace, power generation, and chemical processing industries. ERNiCr-3 provides strong, durable welds and is suitable for applications exposed to harsh environments.
ERNiCrMo-3
ERNiCrMo-3 is a nickel-chromium-molybdenum welding wire used for welding nickel alloys, particularly those containing molybdenum. This wire offers superior pitting and crevice corrosion resistance, making it excellent for use in aggressive chemical environments. It is commonly used in the petrochemical and marine industries, where resistance to seawater and other corrosive substances is critical.
Welding Wire for Low Alloy Steel
Low alloy steel welding wires are used for welding low alloy steels that require high strength and toughness.
ER100S-1
ER100S-1 is a low alloy steel welding wire used for welding high-strength steel. It provides excellent toughness and strength, making it suitable for bridge construction, pressure vessels, and structural steel fabrication applications. This wire offers good weldability and produces strong, impact-resistant welds.
ER80S-D2
ER80S-D2 is another low-alloy steel welding wire designed for welding medium—to high-strength steels. It contains small amounts of manganese and silicon, which improve deoxidation and weld pool fluidity. ER80S-D2 is commonly used in the construction and automotive industries, where strong, durable welds are required. This wire is suitable for welding various low-alloy steels, providing excellent mechanical properties and weld quality.
Flux-Cored Arc Welding Wires
Flux-Cored Arc Welding (FCAW) wires are designed for high-efficiency welding and are categorized into self-shielded and gas-shielded types. These wires offer higher deposition rates and improved productivity, making them suitable for various industrial applications.
Self-Shielded Flux-Cored Wires (FCAW-S)
Self-shielded flux-cored wires are popular due to their versatility and ease of use. They do not require external shielding gas, as the flux within the wire generates the necessary protection during welding. This makes them ideal for outdoor and field applications where wind or draft conditions could disrupt the shielding gas flow.
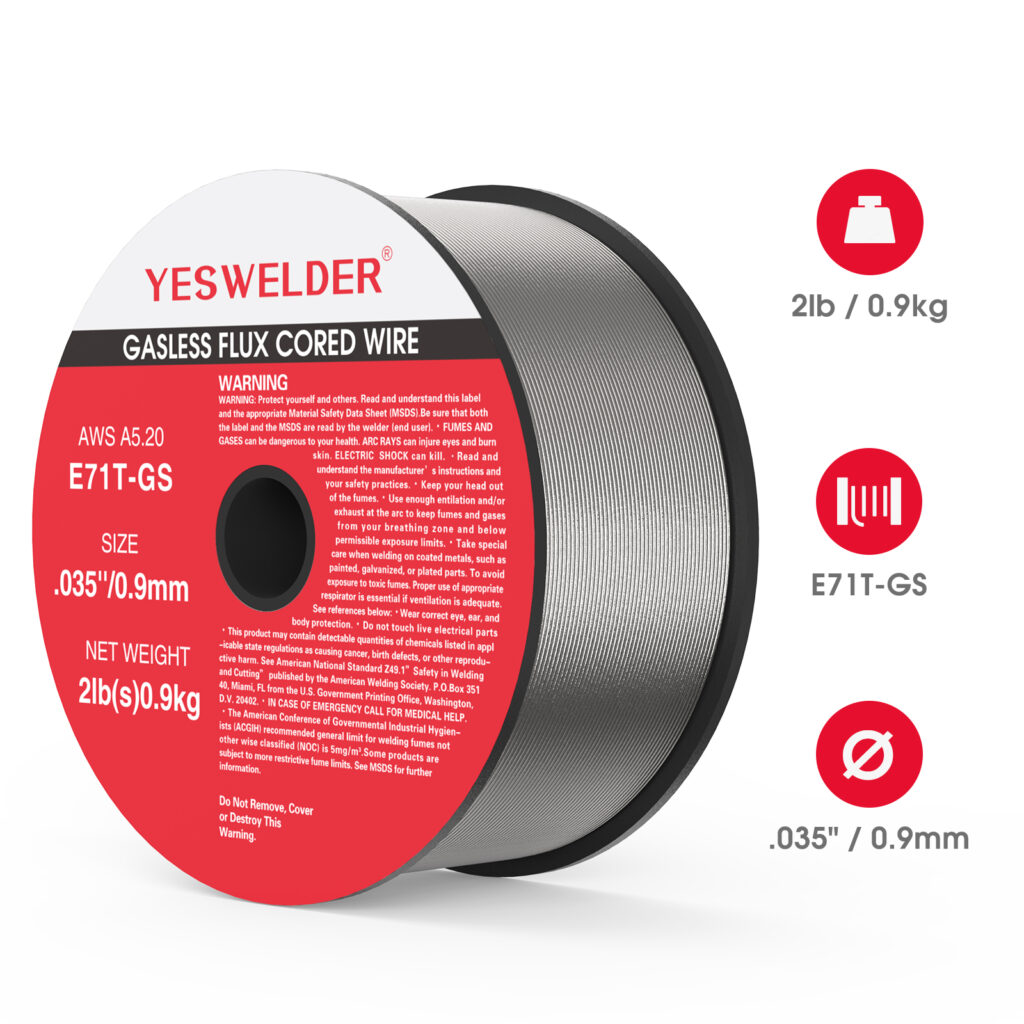
E71T-11
E71T-11 is a commonly used self-shielded flux-cored wire. It is suitable for all-position welding and provides good penetration and bead appearance. This wire is widely used in construction, repair, and maintenance applications. E71T-11 is known for producing clean welds with minimal spatter and slag. Its easy-to-use characteristics make it a favorite among welders working on mild steel and low alloy steels.
Gas-Shielded Flux-Cored Wires (FCAW-G)
Gas-shielded flux-cored wires need an external shielding gas, typically a mix of carbon dioxide and argon. These wires offer higher deposition rates and are used in applications requiring deep penetration and high-quality welds.
E71T-1
E71T-1 is a gas-shielded flux-cored wire for welding carbon and low alloy steels. It provides excellent mechanical properties and is suitable for all-position welding. This wire is often used in heavy fabrication, shipbuilding, and structural steel applications. E71T-1 offers good slag removal and produces smooth, clean welds with low spatter levels. Using shielding gas enhances the weld quality and reduces the risk of porosity.
Welding Wires and their Properties
Wire Type | Base Material | Properties | Welding Method |
ER4043 | Aluminum | High silicon content, good fluidity, smooth welds | MIG |
ER5356 | Aluminum | High strength, corrosion resistance, good for marine applications | MIG |
ER308/308L | Stainless Steel | Good corrosion resistance, prevents carbide precipitation | MIG |
ER309 | Stainless Steel | High strength, oxidation resistance, welds dissimilar metals | MIG |
ER316 | Stainless Steel | Enhanced corrosion resistance, good for marine environments | MIG |
ERNi55 | Cast Iron | Excellent machinability, strong and crack-resistant welds | MIG |
ErNi-Fe-CI | Cast Iron | Good weldability, high strength and toughness | MIG |
ERCu | Copper | Good electrical conductivity, corrosion resistance | MIG |
ERSiCu | Copper | Improved strength and fluidity, good electrical conductivity | MIG |
ERNiCr-3 | Nickel Alloys | High-temperature oxidation and corrosion resistance | MIG |
ERNiCrMo-3 | Nickel Alloys | Superior pitting and crevice corrosion resistance | MIG |
ER100S-1 | Low Alloy Steel | High strength and toughness, good weldability | MIG |
ER80S-D2 | Low Alloy Steel | Improved deoxidation and weld pool fluidity | MIG |
E71T-11 | Mild Steel | Good penetration and bead appearance, minimal spatter | FCAW-S |
E71T-1 | Carbon & Low Alloy Steel | Excellent mechanical properties, good slag removal | FCAW-G |
Tips for Choosing the Right Welding Wire
Selecting the appropriate welding wire is crucial for achieving high-quality welds. Two important factors are matching the base material and the welding method.
Match the Base Material
The 1st step in selecting the best welding wire is to match it with the welded base material. Different metals require specific welding wires to ensure proper bonding and strength. For instance, stainless steel welding wires should be used for stainless steel materials, while aluminum welding wires are necessary for aluminum workpieces. Matching the welding wire to the base material helps prevent issues such as cracking, poor adhesion, and corrosion, ensuring the integrity and durability of the weld.
Consider the Welding Method
The welding method also plays a significant role in selecting the right wire. Different welding methods, such as MIG, TIG, and FCAW, require specific wires designed to meet their unique requirements. For example, MIG welding commonly uses solid wires, while FCAW utilizes flux-cored wires. Additionally, consider whether the welding environment is indoor or outdoor, as some wires are better suited for outdoor use due to their self-shielding properties.
Final Thoughts
Selecting the right welding wire is crucial for ensuring weld quality and durability. It is essential to understand the properties of different wires and match them with the base material and welding method. YesWelder provides various types of welding wires and rods for different welding methods. Choosing the appropriate wire can achieve better weld results, increase efficiency, and reduce post-weld work.
FAQs
What is the most commonly used MIG welding wire?
The most commonly used MIG welding wire is ER70S-6, known for its versatility and excellent welding performance on mild steel.
What is the difference between self-shielded and gas-shielded flux-cored wires?
Self-shielded flux-cored wires do not require external shielding gas, making them ideal for outdoor use. Gas-shielded flux-cored wires require an external gas supply and are used for high-quality welds in controlled environments.
Which welding wire is best for aluminum?
ER4043 and ER5356 are the best choices for welding aluminum, with ER4043 providing good fluidity and ER5356 offering higher strength and corrosion resistance.
Can you use the same stainless steel and carbon steel welding wire?
Different welding wires are needed for stainless steel and carbon steel to ensure proper weld quality and prevent corrosion. ER308/308L is commonly used for stainless steel, while ER70S-6 is used for carbon steel.
What aspects should be considered when choosing a welding wire?
Key factors include matching the wire to the base material, the welding method, the required mechanical properties, and the specific application requirements.