What is arc welding? Arc welding is the backbone of modern fabrication, fusing metals with an electric arc hotter than the sun’s surface—over 6,500°F (3,593°C). It’s how we build everything from the steel skeletons of skyscrapers to the titanium seams of spacecraft.
Arc Welding Explained
At its heart, what is arc welding?
It’s a process where an electric current jumps between an electrode and a metal workpiece, igniting an arc—a plasma channel glowing at 11,732°F (6,500°C).
This intense heat melts the metal’s surface (typically 2,500-3,000°F or 1,371-1,649°C for steel), while a filler material, often from the electrode, flows into the molten pool. As it cools, the mix solidifies into a joint stronger than the base metal—sometimes exceeding 60,000 psi tensile strength for steel welds.
The current comes in two ways: alternating (AC) or direct (DC).
AC oscillates 60 times per second, breaking through oxide layers on aluminum (melting point 1,221°F/660°C) with its 50% positive/negative cycle, and costs less—about $0.02 per kWh less than DC in U.S. industrial rates.
DC, flowing one way, delivers a steady arc, perfect for thin steel (e.g., 1 mm) or stainless (e.g., 2,750°F/1,510°C melting point), reducing spatter by 20% compared to AC (AWS data).
Shielding keeps the weld clean.
Inert gases like argon (99.9% pure, 15-20 cubic feet/hour flow) or helium block oxygen and nitrogen, which can weaken joints by up to 30% through oxidation.
Flux—a powdery coating or wire core—melts into slag, shielding the pool and adding alloys like manganese for toughness (up to 1.5% in steel welds).
Arc Welding: A Brief History
Arc welding’s roots trace back to 1887, when a Russian inventor patented carbon arc welding—using carbon rods to fuse metals with a crude 200-amp arc.
By 1904, metal electrodes replaced carbon, and in 1910, coated rods with flux debuted, cutting weld defects by 40% (early AWS records). The 1930s saw gas-shielded methods emerge—argon and helium boosted weld purity, doubling joint strength for steel from 30,000 to 60,000 psi.
World War II turbocharged its rise. Over 2,700 Liberty ships—each with 500,000 welds—rolled out between 1941 and 1945, shaving construction time from 230 days to 39 days per vessel.
By the 1980s, automation crept in, and in 2025, robots weld 40% of U.S. industrial joints, saving $2.5 billion annually in labor. From a spark in 1887 to AI-driven welds today, arc welding’s legacy is forged in steel and innovation.
Different Types of Arc Welding Processes
Arc welding splits into specialized processes, each tailored to specific metals and jobs.
Shielded Metal Arc Welding (SMAW)
SMAW uses a consumable electrode (e.g., E6011, 1/8-inch) coated in flux arcs at 80-150 amps, melting into a pool shielded by slag. Often, this process needs a stick welder.
- Best For: Steel (1-20 mm), construction beams, pipelines—handles rusty surfaces with 10% defect tolerance.
- Pros: Portable (20-lb setups), $50/day cost, works in wind up to 20 mph.
- Cons: Slow (100 inches/hour), slag removal adds 10 minutes per foot.
Gas Metal Arc Welding (GMAW/MIG)
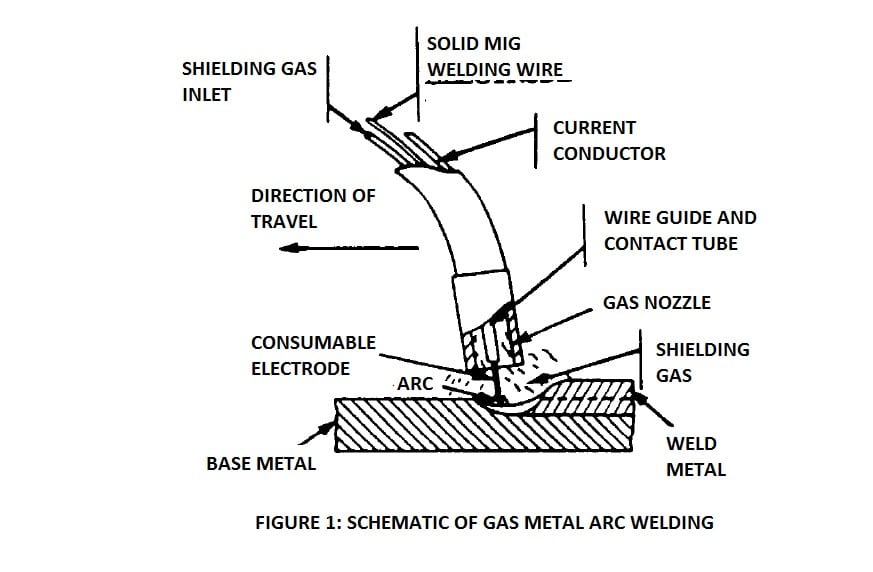
A MIG welding machine is in this use. A 0.035-inch wire feeds at 200-400 amps through a gun, shielded by gas (75% argon/25% CO2, 20 CFH).
- Best For: Automotive steel (2-10 mm), factory lines—welds 400 inches/minute.
- Pros: Fast, semi-automated, 15% less training time than TIG.
- Cons: Gas cylinders (40 lbs) limit mobility; 10% spatter on dirty metal.
Gas Tungsten Arc Welding (GTAW/TIG)
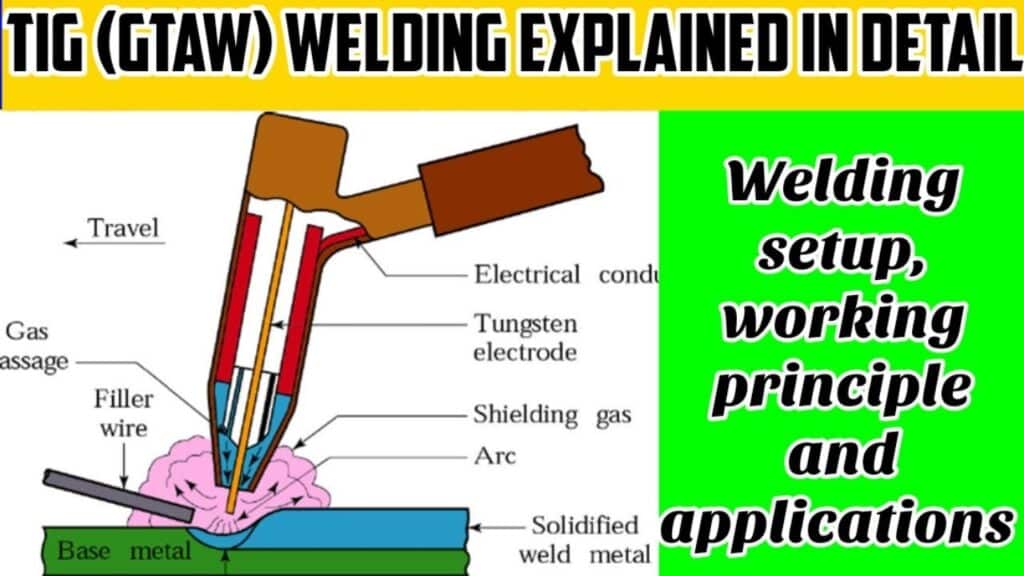
A TIG welding machine is the perfect choice. A non-consumable tungsten electrode (2% thoriated, 1/16-inch) arcs at 50-150 amps with argon (15 CFH); filler rod added manually.
- Best For: Aluminum (0.5-4 mm), aerospace titanium—99% parent metal strength.
- Pros: Clean, precise (0.1 mm tolerance), oxide-breaking AC mode.
- Cons: Slow (50 inches/hour), 20% higher skill curve.
Submerged Arc Welding (SAW)
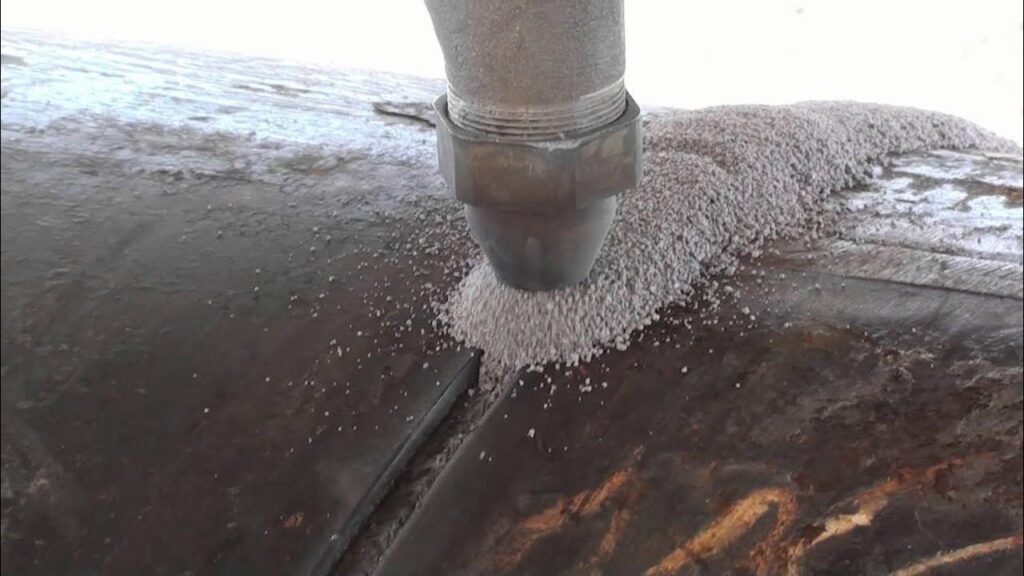
- How It Works: A 1/8-inch wire arcs at 300-600 amps under a flux blanket (silica-based, 10 lbs/hour), fully automated.
- Best For: Thick steel (25-100 mm), ship hulls, bridge girders—penetrates 50% deeper than MIG.
- Pros: High volume (1,000 lbs weld metal/day), 5% defect rate.
- Cons: 500-lb setups, indoor-only due to flux dust.
Plasma Arc Welding (PAW)
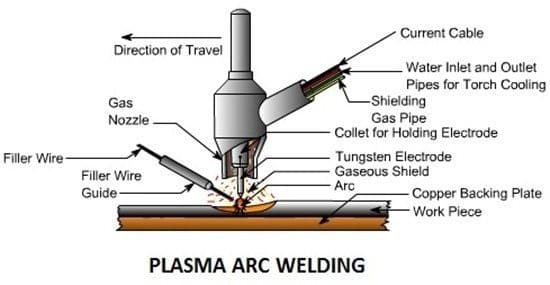
- How It Works: A tungsten electrode ionizes gas into a 15,000°C (27,032°F) plasma jet at 50-200 amps, argon-shielded.
- Best For: Titanium (1-6 mm), aerospace fittings—0.05 mm precision.
- Pros: Minimal heat-affected zone (50% smaller than TIG), 98% joint purity.
- Cons: $5,000+ equipment, 30% slower than MIG.
Flux-Cored Arc Welding (FCAW)

- How It Works: A 0.045-inch flux-filled wire arcs at 150-300 amps, optional gas (80% argon/20% CO2) for dual shielding.
- Best For: Outdoor steel (3-12 mm), construction cranes—wind-resistant up to 35 mph.
- Pros: 300 inches/hour, 15% stronger than SMAW on thick joints.
- Cons: 20% more fumes (0.8 mg/m³ zinc oxide), $1/lb wire cost.
Related article: Flux-Core Arc Welding: From Shipbuilding to Structural Steel.
How Arc Welding Works: Step-by-Step
Curious about how arc welding works hands-on? Check this:
- Setup: Pick an electrode—E6011 (steel, DC, 80-120 amps) or E7018 (low-hydrogen, 100-150 amps). Set voltage (20-30V) and polarity (DCEN for deep penetration).
- Arc Strike: Tap the electrode to the metal, pull back 1/8 inch—sparks fly as the 6,500°F arc ignites. Hold steady; a 1/16-inch gap burns the rod.
- Weld: Tilt 15-30° (drag for SMAW, push for MIG), feed filler at 1-2 inches/minute, and move 5-10 inches/minute to shape a 1/4-inch-wide pool. Watch for a blue arc hue—yellow means too much heat.
- Finish: Chip SMAW/FCAW slag with a hammer (5-10 lbs force), grind if smooth (60-grit wheel), and test with dye penetrant—cracks show pink under UV.
Applications and Industries Using Arc Welding
1. Automotive: GMAW welds 1.5 mm steel car frames at 400 inches/minute—15 million U.S. vehicles in 2024 relied on it (Bureau of Transportation).
2. Aerospace: GTAW joins titanium (3,034°F/1,668°C melting point) for jet turbines—e.g., a 2024 U.S. jet used 2,000 lbs of TIG-welded titanium, slashing weight by 20% (FAA data).
3. Construction: SMAW fuses 20 mm steel beams in skyscrapers—e.g., a 2025 NYC tower used 10,000 tons of welded steel for 110 floors.
4. Shipbuilding: SAW welds 50 mm hull plates—a single cargo ship averages 1,200 tons of steel, 80% arc-welded (U.S. Maritime, 2024).
5. Energy: FCAW builds offshore rigs—e.g., a Gulf platform in 2024 took 5,000 welds on 12 mm steel pipes.
Moreover, here are some trendy application of arc welding:
- Automation: Robots weld 40% of U.S. industrial joints—e.g., a Detroit plant in 2024 saved $1.2 million with 10 SAW bots.
- Sustainability: Argon recycling rose 20%—a 2025 shop cut gas costs from $500 to $400 monthly (AWS). Low-hydrogen rods (E7018) reduce emissions by 15%.
- AI: Smart sensors flag defects (e.g., 0.1 mm cracks) in real-time, slashing rework by 25%—a 2024 shipyard boosted efficiency 10% (industry report).
- Market Growth: The global welding sector hits $25 billion in 2025, with arc methods driving 60%—$15 billion.
Safety in Arc Welding
Arc welding’s power comes with risks—here’s how to stay safe:
- UV Radiation: The arc’s UV is 100 times sunlight’s intensity—OSHA mandates shade 10-13 helmets (blocks 99.9% UV) and full-coverage leather to prevent burns in 5 seconds of exposure.
- Fumes: Welding galvanized steel releases zinc oxide—5 mg/m³ in 10 minutes triggers “metal fume fever” (OSHA limit). Exhaust at 100 CFM or use an N95 respirator.
- Fire: Sparks hit 1,000°F (538°C), flying 35 feet—leather PPE resists 1,200°F flashes, and a 10-lb CO2 extinguisher stops flare-ups.
- Electricity: 20-100V arcs can shock—insulated gloves (1,000V rating) and dry boots cut risks by 90%.
Arc welding’s brilliance spans SMAW’s rugged roots to PAW’s aerospace finesse. It’s a $15 billion force—robots, AI, and eco-tweaks making it faster, cleaner, and stronger.
FAQs About Arc Welding
What’s the easiest arc welding process for beginners?
SMAW is a friendly choice for beginners. It’s $100 setups, no gas, and a 10% learning curve edge over TIG.
How hot does an arc weld get?
The arc peaks at 11,732°F (6,500°C), melting steel at 2,500°F (1,371°C) and titanium at 3,034°F (1,668°C).
Can arc welding be used on aluminum?
Yes, GTAW (TIG) with AC breaks its oxide layer (3,700°F/2,038°C melting point) for 98% pure joints.