Welding is critical in many industries, yet choosing the right method can be challenging. With various options available, how do you decide which is best for your specific needs? This dilemma often leaves professionals and hobbyists questioning whether to opt for MIG (Metal Inert Gas) or TIG (Tungsten Inert Gas) welding.
This comprehensive guide is designed to demystify MIG and TIG welding techniques, providing clear insights into their fundamentals, advantages, and limitations. By the end of this article, you will thoroughly understand which welding method best suits your projects, ensuring optimal results and efficiency.
Fundamentals of MIG vs TIG Welding
MIG and TIG welding may seem similar initially, but their procedures and applications differ significantly. Here’s a detailed look at how each method works and what differentiates them.
MIG Welding
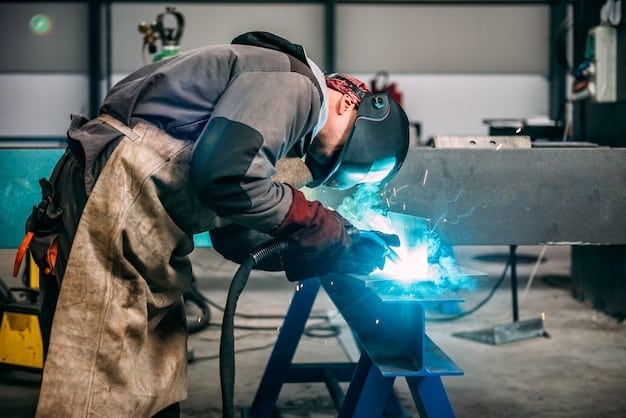
MIG welding (Metal Inert Gas welding) is widely used for its speed and ease of use. This method involves feeding a continuous wire electrode through a welding gun while releasing a shielding gas. The weld pool is often shielded by CO2 (100%) or a mix of argon and carbon dioxide to prevent contamination from the air as the wire electrode melts and fuses the base materials.
One of the standout characteristics of MIG welding is its versatility. It can be applied to a wide range of metals, including steel and stainless steel, making it a dependable choice for many projects. The process is straightforward, making it accessible to beginners.
MIG welding is highly efficient for large projects requiring long, continuous welds, such as automotive repair, construction, and heavy equipment manufacturing. The continuous wire feed and automated process allow for faster welding speeds and higher productivity, instilling confidence in its applicability to diverse projects.
TIG Welding
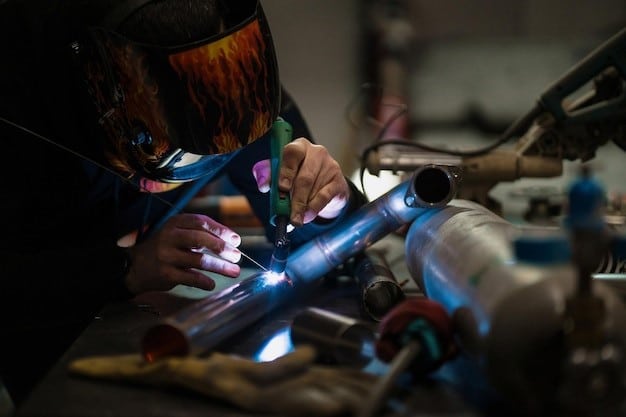
TIG welding, also known as Tungsten Inert Gas welding, is a technique that fuses metal using a non-consumable tungsten electrode. The TIG welder manually feeds a separate filler material into the weld pool while pure argon, an inert gas, shields the weld area from contamination. Due to its accuracy and control, TIG welding is ideal for precise and delicate work, providing reassurance about its suitability for such tasks.
A significant advantage of TIG welding is its ability to consistently produce high-quality, clean welds with minimal spatter. This makes it the preferred choice for critical appearance and precision applications, such as aerospace, piping, and artistic metalwork. The confidence in its performance is particularly high for projects where the appearance and integrity of the weld are critical.
MIG vs TIG Welding Comparison Table
Aspect | MIG Welding | TIG Welding |
Equipment and Setup | Continuous wire electrode, shielding gas (CO2(100%) or a mix of argon and CO2), DC power source | Non-consumable tungsten electrode, shielding gas (argon), AC/DC power source |
Applications | Automotive manufacturing, construction, heavy equipment production | Aerospace, medical devices, artistic metalwork |
Material Compatibility | Steel, bronze and stainless steel | Thin materials, aluminum, exotic metals (titanium, magnesium) |
Speed and Efficiency | High welding speeds, high productivity | Slower process, lower productivity |
Quality and Precision | Good quality welds, more spatter | High-quality, clean welds, minimal spatter |
Skills and Techniques | Easier to learn, accessible to beginners | Higher skill level required, extensive training needed |
Safety | Steel, bronze, and stainless steel | High-frequency current hazards, precise control needed |
Pros and Cons of TIG Weld vs MIG Weld
Before you decide which welding technique to choose, understanding the pros and cons of TIG and MIG welding is essential. This knowledge guides your selection process and enhances your welding skills overall.
MIG Welding
Pros
- High Welding Speed and Productivity
- Versatility Across Different Metals
- Ease of Use
- Consistent Weld Quality
- Efficiency in Long Welds
Cons
- More Spatter Production
- Not Ideal for Thin Materials
Detailed Analysis of Key Points
1. High Welding Speed and Productivity
The speed of MIG welding is a critical factor in high-volume production environments, such as automotive manufacturing. The continuous wire feed mechanism allows uninterrupted welding, minimizing downtime and increasing overall throughput. This efficiency is crucial for maintaining production schedules and reducing labor costs, making the MIG welding machine a preferred choice for large-scale industrial applications.
2. Versatility across Different Metals
MIG welding’s ability to work with various metals makes it an essential tool in diverse industries. For example, in construction, the ability to weld steel beams for structural support and bronze for decorative elements using the same equipment simplifies the process and reduces the need for multiple welding setups.
TIG Welding
Pros
- High-Quality Welds
- Suitable for Thin and Exotic Materials
- Greater Control and Precision
- Clean Welds with Minimal Spatter
- Flexibility in Filler Material Use
Cons
- Slower Process
- Requires Higher Skill Level
Detailed Analysis of Key Points
1. High-Quality Welds
The precision of TIG welding makes it indispensable in industries where weld quality is paramount. For example, in aerospace engineering, the integrity of each weld must meet stringent safety standards. TIG welding provides the control needed to create flawless joints that can withstand extreme conditions, ensuring the reliability of critical components.
2. Suitable for Thin and Exotic Materials
TIG welding’s ability to handle thin and exotic materials is a significant advantage in specialized fields. For instance, in the medical device industry, where titanium, magnesium, and other non-standard metals are often used due to their unique properties, TIG welding provides the precision required to create intricate, delicate welds without compromising the material’s properties.
MIG vs TIG Welding Comparison
Equipment and Setup
One of the primary differences between MIG and TIG welding is their equipment and setup. MIG welding uses a straight wire electrode provided through a welding gun and a protective gas to protect the weld pool from contaminants. This shielding gas is usually a mix of argon and carbon dioxide. The power source for MIG welding is a constant-voltage, direct-current (DC) machine, which keeps the arc stable and ensures consistent weld quality.
TIG welding generates the arc using a non-consumable tungsten electrode. As needed, the welder manually feeds a separate filler material into the weld pool. Pure argon is commonly used as the shielding gas, although helium or a mix of both can be used for specific applications. The power source for TIG welding can be alternating current (AC) or direct current (DC), depending on the material being welded. AC is often used for aluminum and magnesium, while DC is preferred for steel and other metals.
MIG vs. TIG Welding Applications
MIG and TIG welding are utilized in various applications, each suited to different project requirements. MIG welding is highly efficient for large-scale projects that demand high welding speeds, such as automotive manufacturing, construction, and heavy equipment production. The process’s speed and ease of use make it ideal for tasks that require long, continuous welds.
TIG welding is chosen for applications where precision and weld quality are paramount. It is extensively used in aerospace, medical device manufacturing, and artistic metalwork. TIG welding’s ability to produce clean, high-quality welds with minimal spatter makes it the preferred choice for projects where the appearance and integrity of the weld are critical.
Material Compatibility
The compatibility of welding methods with various materials is a significant factor in their selection. MIG welding is adaptable and can be used on various metals, including steel, stainless steel, cast iron, and bronze. This versatility makes it a go-to method for industries with different metals.
While versatile, TIG welding excels in thin materials like aluminum, copper, and nickel alloys and strange metals such as titanium and magnesium. The precise control over the welding process allows for detailed and delicate work without risking damage to the materials. This makes TIG welding indispensable in fields requiring meticulous attention to material properties and weld quality.
Speed and Efficiency
Speed and efficiency are critical considerations in industrial welding applications. MIG welding is known for its rapid welding speeds, making it highly efficient for large-scale production. The continuous wire feed mechanism ensures a steady supply of filler material, reducing downtime and increasing productivity. This makes MIG welding an excellent choice for projects with tight deadlines and high output demands.
TIG welding is slower due to the manual feeding of filler material and the need for greater precision. While this results in higher-quality welds, it also means that TIG welding is less suited for high-volume production. The slower pace of TIG welding is a trade-off for its superior control and quality, making it more appropriate for specialized projects where these factors are more critical than speed.
Quality and Precision
TIG welding is unmatched in weld quality and precision. The method allows for precise control over the heat and the welding process, resulting in clean, high-quality welds with minimal spatter. This is particularly important in aerospace and medical devices, where weld integrity is crucial.
While producing good-quality welds, MIG welding cannot match the precision of TIG welding. The process is more automated, and while this increases speed, it can also result in more spatter and less control over the weld pool. However, for many applications, especially those involving thicker materials, MIG welding provides adequate quality and is far more efficient in speed and productivity.
Skills and Techniques
The skill level required for MIG and TIG welding varies significantly. MIG welding is generally more comfortable to learn and use, making it accessible to beginners and requiring less training. The automated nature of the process and the continuous wire feed system simplify the welding technique, allowing even novice welders to achieve consistent results relatively quickly.
TIG welding demands advanced skills due to the necessity of manually controlling the filler material and the tungsten electrode.TIG welding demands advanced skills due to the necessity of manually controlling the filler material and the tungsten electrode. To achieve high-quality results, the welder must have a steady hand and a good understanding of the welding process. This higher skill requirement means TIG welding often requires extensive training and practice.
Safety
Safety is a crucial aspect of any welding process, and both MIG and TIG welding have specific safety considerations. MIG welding involves shielding gases and a continuous wire feed, which can create hazards such as exposure to fumes and burns from the high heat generated by the welding process. Proper ventilation, protective clothing, and safety equipment are essential to mitigate these risks.
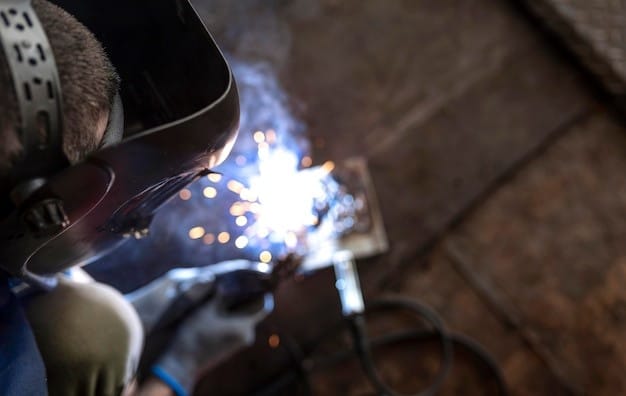
TIG welding also poses safety challenges, mainly due to the use of high-frequency current and the need for precise control of the welding arc. This process usually requires using both hands to manage the welding torch and filler rod, ensuring the weld’s precision and the operator’s safety. The dual-hand operation required for TIG welding, holding the torch in one hand and the filler rod in the other, demands a higher level of skill and coordination. Welders must wear appropriate protective gear, including gloves, helmets, and eye protection, to guard against burns and eye damage. Additionally, TIG welding’s slower pace and the need for manual control increase the risk of fatigue, so it usually needs to use both hands during the welding process.
Costs of MIG and TIG Welding
It’s essential to note that the initial investment and operating costs for MIG and TIG welding can vary. MIG welding equipment tends to be more affordable and less complex, which makes it a more cost-effective option for many businesses. The continuous wire feed and shielding gas setup are relatively straightforward and cost-effective, with shielding gas prices typically ranging from about $20 to $150 per cylinder.
TIG welding equipment, on the other hand, can be more expensive due to the need for high-quality tungsten electrodes and more sophisticated power sources. Additionally, the process is slower, which can increase labor costs over time. The shielding gas for TIG welding can also be more expensive, typically ranging from $30 to $200 per cylinder. However, for applications where weld quality and precision are paramount, the higher costs of TIG welding can be justified by its superior results.
Choosing the right welding type for your project
Selecting between MIG and TIG welding involves assessing technical aspects to determine the best fit for your project.
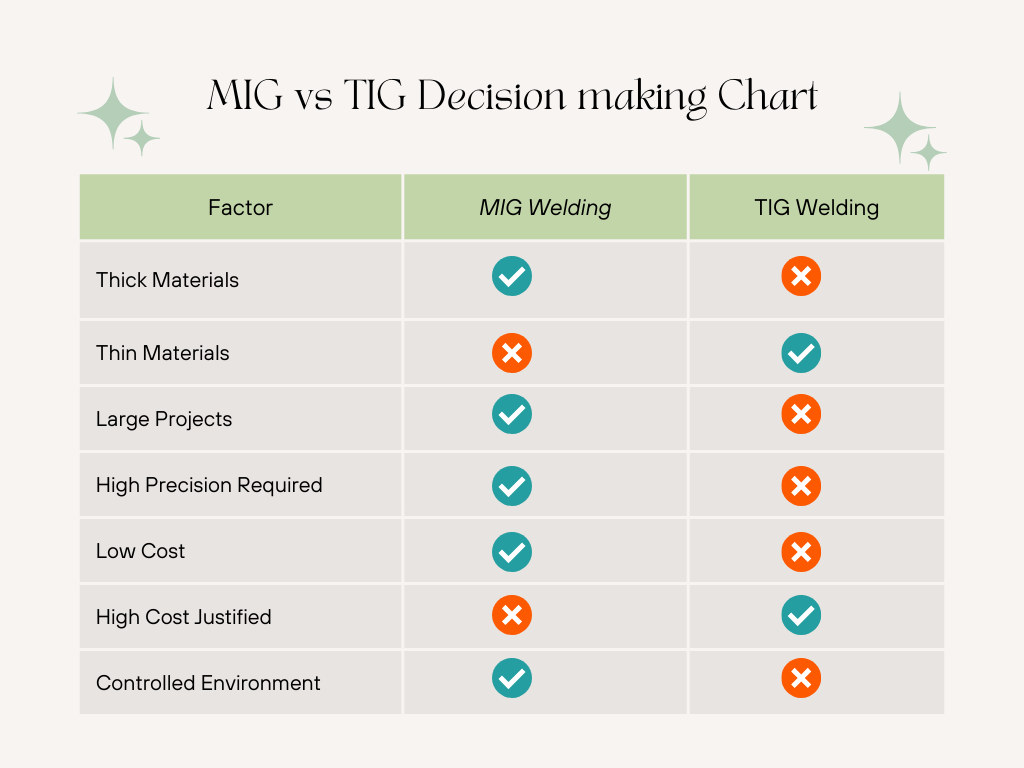
Material Type and Thickness
Due to its deep penetration capabilities, MIG welding is optimal for welding thicker materials. It works effectively on metals like steel, bronze, and stainless steel. TIG welding is competently suited for thin materials like aluminum and exotic metals. It provides precise heat control to prevent warping and achieve clean welds.
Industry Requirements
Industry-specific demands heavily influence the choice of welding method. MIG welding is preferred in industries requiring fast, large-scale production, such as automotive and construction. TIG welding is chosen in fields where precision and high-quality welds are critical, such as aerospace and medical device manufacturing.
Project Size and Welding Speed
MIG welding’s high welding speed and continuous wire feed are advantageous for large projects needing quick completion. TIG welding, though slower, is ideal for projects requiring meticulous detail and superior weld quality, such as artistic metalwork or custom fabrication.
Project Expense
Operational costs differ between the two methods. MIG welding costs less due to faster welding speeds, less labor intensity, and the use of less expensive shielding gases. With its specialized equipment, slower process, and costly shielding gas, TIG welding can be more expensive, but it provides exceptional weld quality crucial for certain applications.
Welding Positions
The versatility of MIG welding allows it to perform well in various positions, including flat, horizontal, vertical, and overhead. TIG welding requires more skill for out-of-position welds, necessitating careful consideration of the welding position when selecting the method.
Welding Environment
Environmental conditions play a crucial role in welding method selection. External factors affect MIG welding less, and it can be used effectively outdoors or in less controlled environments. TIG welding, requiring precise control, is best suited for indoor settings where environmental conditions can be regulated to maintain weld quality.
Multi-Functional Welders for Diverse Applications
Selecting the right welder for your needs is essential for achieving quality results and efficiency. Here are recommendations for Yeswelder MIG and TIG welders suitable for various applications, including industrial use.
Best MIG Welder for Versatile Applications: YesWelder MIG-205DS
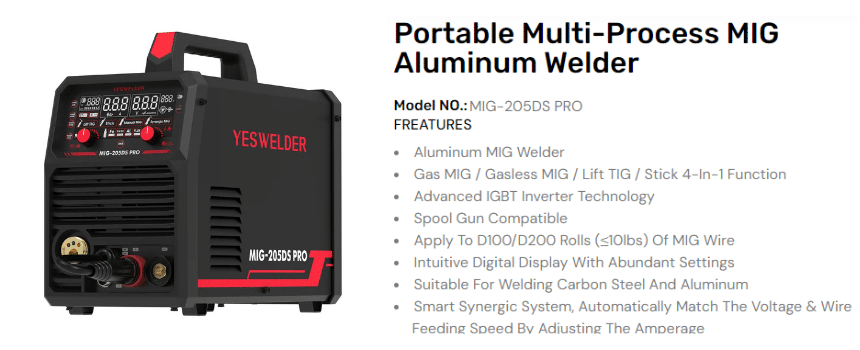
The YesWelder MIG-205DS is a multi-process welder that supports MIG, flux core, and stick welding. Its synergic control mode simplifies setup and automatically changes the voltage and wire speed to ensure consistent weld quality. It is well-suited for various applications involving mild steel, bronze, and stainless steel.
Top MIG Welder for Industrial Use: YesWelder NBM-500
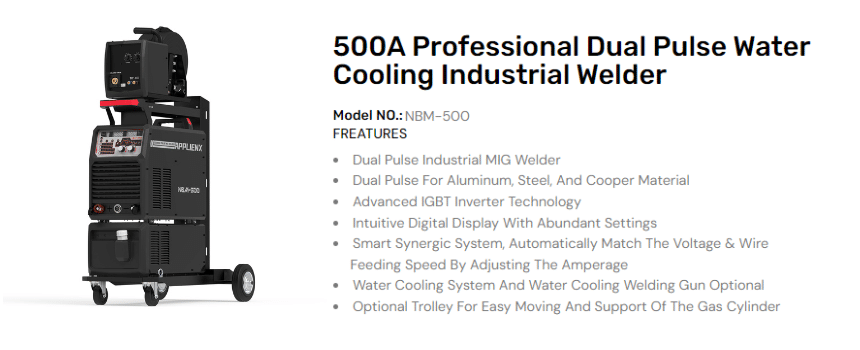
Designed for industrial applications, the YesWelder NBM-500 offers robust performance with advanced features such as pulse MIG and synergic control, enabling precise and high-quality welds. Its durable construction and high-duty cycle make it suitable for continuous operation in demanding environments like shipbuilding and structural steel fabrication.
Top TIG Welder for Industrial Precision: YesWelder TIG-315P
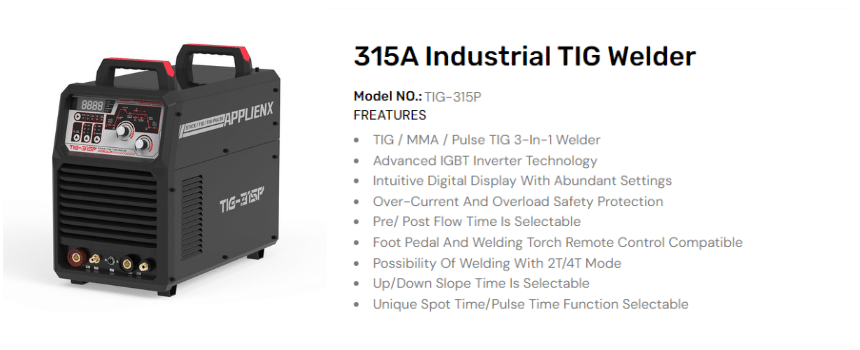
The YesWelder TIG-315P is tailored for industrial-grade TIG welding and supports AC and DC operations. Its pulse welding capabilities allow superior control over heat input, making it perfect for high-precision tasks in aerospace and heavy equipment manufacturing. The advanced cooling system ensures reliable performance during extended welding sessions.
Conclusion
Selecting the appropriate welding method is crucial for achieving the desired results. MIG welding is ideal for large-scale projects requiring speed and versatility, while TIG welding excels in precision and high-quality work. The YesWelder MIG-205DS and YWT-200DC are excellent for versatile and detailed tasks. The YesWelder NBM-500 and TIG-315P offer robust performance and precision for industrial applications. Understanding the strengths of each welding method and matching them to your project needs ensures optimal outcomes and efficiency in your welding endeavors.
FAQs
What are the fundamental differences between MIG and TIG welding?
MIG welding involves a continuous wire feed and is better suited for thicker materials and high-volume projects. On the other hand, TIG welding utilizes a non-consumable tungsten electrode, providing precision and high-quality welds for thin and exotic materials.
Which industries typically use MIG welding?
Due to its speed and versatility, MIG welding is commonly used in automotive, construction, and heavy equipment manufacturing.
Why is TIG welding preferred for aerospace applications?
TIG welding provides superior control and precision, producing high-quality welds with minimal spatter, which is crucial for the aerospace industry’s stringent safety and performance standards.
How does the YesWelder MIG-205DS enhance welding efficiency?
The YesWelder MIG-205DS features synergic control, which automatically adjusts the voltage and wire feed speed, ensuring consistent weld quality and simplifying welding.
What makes the YesWelder TIG-315P suitable for industrial use?
The YesWelder TIG-315P supports AC and DC welding, includes pulse welding capabilities for precise heat control, and has an advanced cooling system, making it ideal for high-precision industrial applications. It operates within a welding current range of 20-315 amps and has a duty cycle of 60% at 40℃ over a 10-minute period.