MIG welding is an important process in several industries from aerospace to shipbuilding, being all the more important in aluminum works. Aluminum welding demands special consideration because of its unique characteristics and challenges. This article encompasses a full-fledged guide on mastering MIG welding aluminum.
Can One MIG Weld Aluminum?
MIG welding (metal inert gases) is a process of welding through continuous wire feed, and that wire serves as both the filler material and the electrode. This makes it easier to almost weld anything, including aluminum. Its many advantages in terms of speed and versatility allow MIG to be used in a production environment.
Aluminum makes welding different than steel for MIG welding. The faster heat dissipation from weld aluminum than steel from the welding puddle may not only dictate methods to hold the weld puddle but also creates problems such as burn-through and warpage in thin sections.
Conversely, these challenges provide opportunities to apply other techniques and tools while setting and adapting the MIG welding parameters to yield the best welds with minimal defects on aluminum.
MIG vs. TIG Welding: When to Use What?
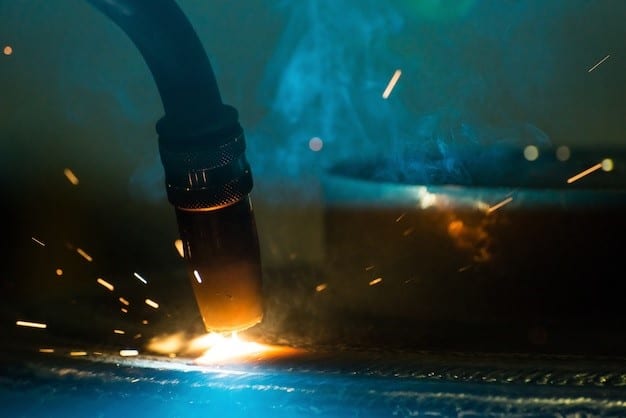
In general, both MIG and TIG welding are popular processes used in aluminum welding; however, each has its advantages and disadvantages, depending on the application. In knowing these differences, it is easier to make decisions as to when to go with MIG rather than TIG.
Pros of MIG Welding for Aluminum
Scope for Speed: MIG welding is an entirely speedy procedure if compared to TIG; hence, most suited for mass production or large-scale jobs. Welding can thus be completed quickly with be-in-welders intervention. Due to the automatic mode of the wire-feed and continuous feed operations, more speed is afforded by the process.
User-Friendly: Compared to TIG welding which requires advanced skills with precision, the MIG welding process offers fewer challenges to the welder. The automatic working of the wire feed provides the welder every chance for a consistent bead.
Post-Welding Clean-Up: MIG welding limits the amount of spatter produced. Thus, there is less cleaning after the weld.
Cons of MIG Welding for Aluminum
Lower Accuracy- More precision is demanded by TIG welding. Therefore, the application of MIG is arduous for applications requiring very fine welds in thin aluminum areas.
Heat Control- Aluminum is sensitive to heat; if too much heat is conducted during the weld, burning will occur. Therefore, controlling the heat during welding with MIG on aluminum is more difficult than TIG.
MIG Welding: When to Use?
MIG welding is best for projects requiring speed and productivity, like manufacturing and structural applications. For welding thicker aluminum, it’s most suitable to use MIG welding. If the position does not require extreme precision, MIG becomes the better option. There are further differences that pertain to applications; check out MIG vs TIG Welding: Understanding All the Fundamentals.
MIG Welding Aluminum: Essential Equipment
Welding aluminum requires the right equipment to ensure that the job is done efficiently and effectively. Below are the essential tools and components needed for MIG welding aluminum.
Right Aluminum MIG Welder
Not all MIG welders are suitable for aluminum; aluminum welding is slightly different. There are special considerations with aluminum, such as soft, low melting point material. Select a welder with high-quality wire feed mechanisms, adjustable voltage settings, and control over the shielding gas.
Typical MIG welding machines like YesWelder MIG-205DS Pro MIG welding machine have features tailored for aluminum welding, among them adjustable settings to suit aluminum-specific parameters.
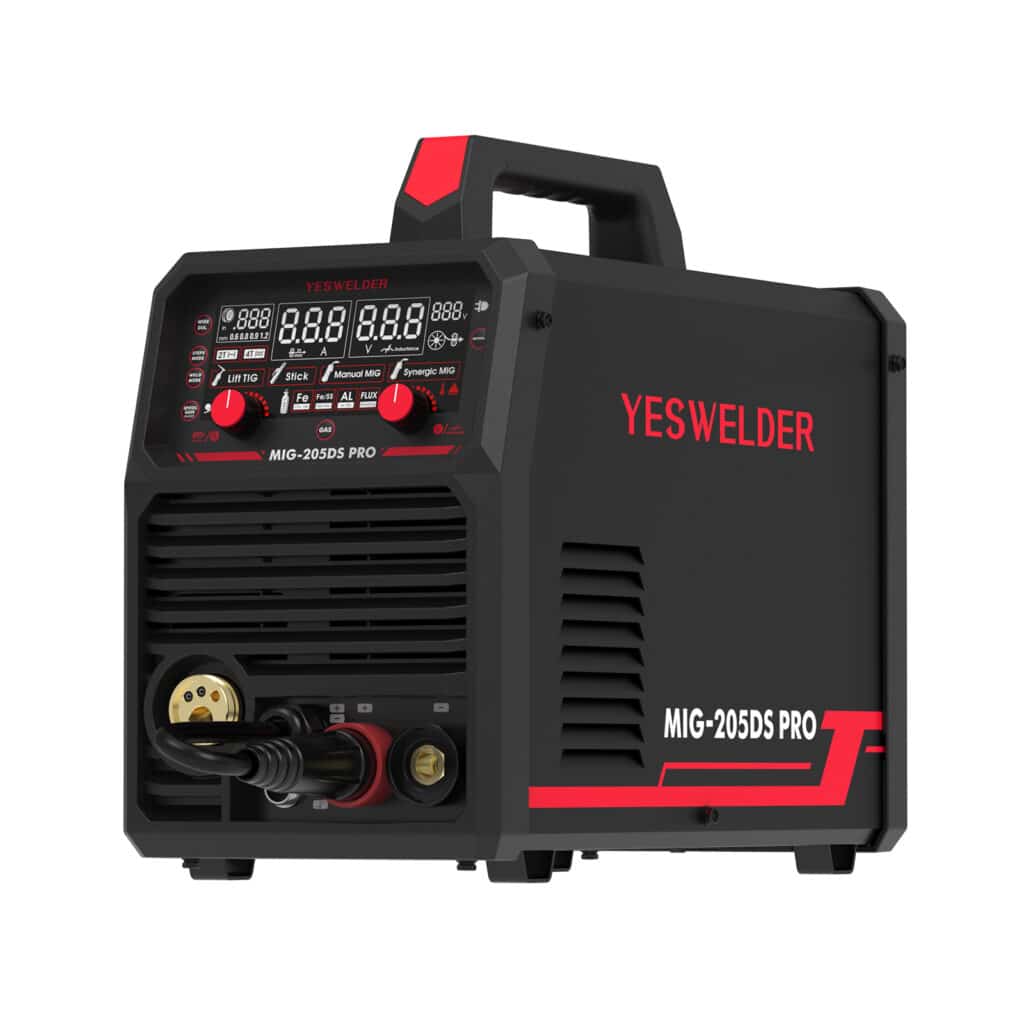
Cleaning Tools
Without welding, aluminum is covered with an oxide layer that needs to be removed. If this oxide layer is not removed properly, it leads to a bad weld due to contamination. It is possible to remove the oxide layer using a stainless steel wire brush or chemicals specifically designed to clean aluminum.
Filler Rod Selection
Selection of an appropriate filler rod for aluminum welding is critical. Typical filler rods used for aluminum welding include 4043 and 5356. While being more of a general-purpose filler rod, 4043 is also good for fluidity, whereas 5356 is preferred for high-strength applications, with some levels of stress on the welded joint.
Shielding Gas
Shielding gas in aluminum welding is required to protect the molten metal from being contaminated by atmospheric air. While shielding in steel welding requires a gas mixture, in aluminum welding only 100 percent argon gas is used as shielding. The flow rate of the shielding gas is also much higher than that in steel welding, between 35 and 50 CFM (17-25 L/min).
Setting Up the MIG Welder for Aluminum
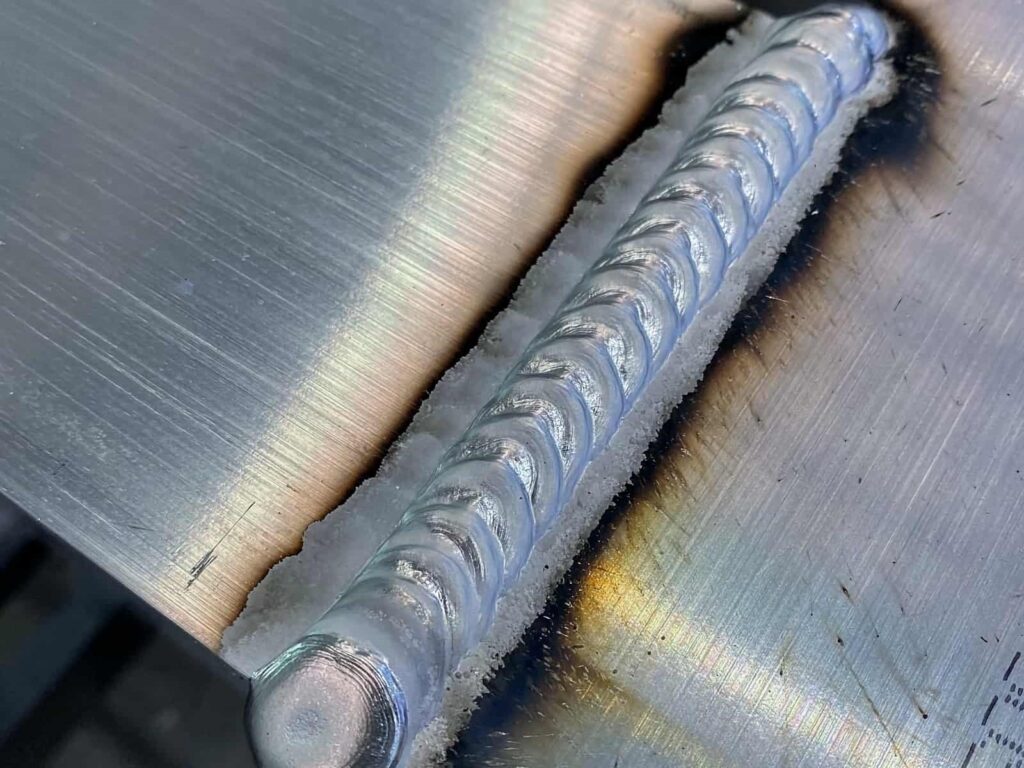
Source: How To MIG Weld Aluminum: Beginners Guide (with Chart)
Once you have acquired the right equipment, the next thing is to set up your MIG welder specifically for aluminum. Proper settings ensure a flawless run on the actual welding with good results.
Gas Flow Rate
Gas flow rate is one of the most important conditions in aluminum welding. A normal flow rate would be between 35 and 50. Make sure that the flow is enough to keep contaminants away from the weld but not so high as to cause turbulence that disrupts the gas shielding.
Voltage and Amperage Settings
Voltage and amperage for aluminum welding should always be set in relation to the thickness of the material being welded. Voltage and amperage should be started low and increased during the progression of the weld. Recommended voltage rates are normally situated between 17 to 22 volts, which depends on aluminum thickness-wider weld beads being produced for higher voltage settings.
Polarity Settings
The welder must be set to the right polarity when welding aluminum. DCEP (Direct Current Electrode Positive) polarity settings are set for aluminum welding, thus ensuring proper penetration and bead formation for aluminum.
Best MIG Welding Techniques for Aluminum
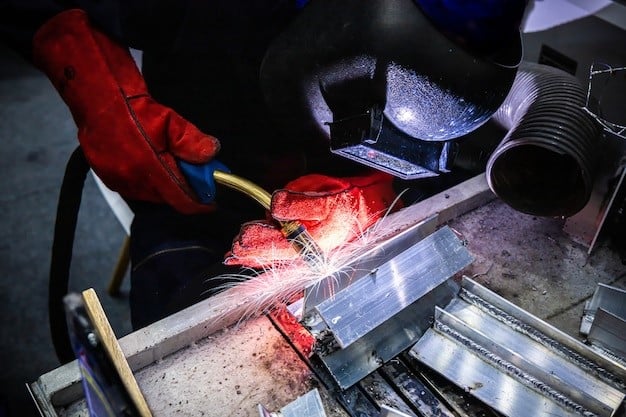
The importance of technique is equally paramount as is the right equipment when MIG welding aluminum. Given below are some critical techniques which will help to create a successful aluminum weld.
Travel Speed
Travel speed will influence heat input, appearance of the bead, and the overall quality of the weld. There must be a steady, constant speed to avoid undercutting or burning through the aluminum. Depending on the material thickness, slow travel speed is often preferred for thin materials in order to control heat input, while thick materials require faster travel speed.
Heat Input
Controlling heat input will ensure that burn-through is avoided, particularly in the case of thin aluminum. In MIG welding aluminum, heat control must be very precise. Too much heat leads to distortion and warping, while too little leads to poor fusion. Pulsed MIG helps with controlling heat input by alternating between peak and background current, maintaining a low average temperature over the weld pool.
Weave Patterns vs. Straight Passes
Whether or not to use weave patterns or straight passes depends on the joint type and the desired appearance. Weave patterns allow control over heat distribution and lend additional strength in large-gap or large-joint configurations, while cleaner and more uniform bead appearance is often preferred for straight passes.
Final Thoughts
Mastering MIG welding on aluminum connects the struggles of the aluminum material with the right equipment and a perfect technique. With varying settings, filler rod choice, and heat input management, strong, clean aluminum welds can be created. Fast and efficient for aluminum welding, MIG welding will serve you well whether you’ve got automotive parts, aerospace applications, or construction projects on your plate.
YesWelder Welding Machine Wholesale
If you want to buy good welding machines, YesWelder has such a purpose with which you can trust it as a supplier. It is reliable and economical in its supply of high-performance welding machines to wholesale buyers and distributors. Their machines are totally built to last on an aluminum welding and metal fabrication projects-highly demanding mechanism. YesWelder, with its large assortment and reasonable pricing, is the choice for business professional welding solutions.
FAQ
Can MIG welders be used for all types of aluminum?
Yes, MIG welders do an excellent job of welding most aluminum, given that you have the right equipment and settings and using the correct filler rod and shielding gas.
Why is shielding gas important in aluminum welding?
The shielding gas protects the molten metal from contamination, to keep the weld pool clean while providing the strength needed for the final weld. Argon is the most commonly used gas for shielding aluminum welding.
How to prevent burn-through when MIG welding aluminum?
Heat input is the key when preventing burn-through. Burn-through on thin aluminum can be avoided by adjusting voltage and amperage as well as travel speed and the use of one or two pulsed MIG welding.
Can regular MIG wire be used for aluminum?
No. Aluminum needs a specific type of MIG wire that is softer and more prone to kinking. Typically, aluminum wire and a spool gun are used for aluminum welding to maintain wire feed control.
What is the major benefit of pulsed MIG welding for aluminum?
Pulsed MIG welding helps control heat input by alternating between high peak current and low background current, thereby minimizing the risk of burn-through, warpage, and distortion; in addition, pulsed MIG can keep travel speeds quite high while still maintaining welding quality.