Welders face a common challenge when their machines overheat during prolonged use, reducing efficiency and increasing downtime. This overheating can damage the equipment and compromise the quality of welds. The solution to this issue lies in understanding and managing the welder’s duty cycle. By knowing the duty cycle, welders can operate their machines within safe limits, ensuring productivity and longevity. This article explains what is duty cycle in welding, how to calculate it, and its importance in choosing the right welding machine for various applications.
Duty Cycle Definition
The duty cycle is a crucial specification in welding that determines how long a machine can operate within a set time frame without overheating. It is typically expressed as a percentage over 10 minutes. For example, a welder with a 60% duty cycle can run for 6 minutes and then needs 4 minutes to cool down. This helps prevent equipment damage and ensures consistent weld quality. Knowing the duty cycle helps you choose the right machine and welding equipment supplier for their specific tasks and avoid excessive downtime due to overheating.
How Duty Cycle Is Calculated
Calculating the duty cycle of a welding machine is straightforward. It is the percentage of 10 minutes during which the machine can safely operate without overheating. For example, if a welder has a 30% duty cycle at 200 amps, it can weld for 3 minutes and then must cool down for 7 minutes. The higher the welding current, the shorter the operating time, as more heat is generated.
Manufacturers usually provide this rating for specific amperages, so matching the duty cycle to the welding task is essential. Understanding this calculation helps choose the right machine, ensuring the welder can perform efficiently without overheating or damaging the equipment.
Duty Cycle Ratings and Corresponding Cool-Down Times
Duty Cycle Percentage | Operating Time (in 10 minutes) | Cool-Down Time (in 10 minutes) |
20 | 2 minutes | 8 minutes |
40 | 4 minutes | 6 minutes |
60 | 6 minutes | 4 minutes |
80 | 8 minutes | 2 minutes |
100 | Continuous operation | No cool-down required |
Importance of Duty Cycle in Welding
Machine Performance
The duty cycle plays a critical role in maintaining the performance of a welding machine. Machines operating beyond their duty cycle can overheat, reducing efficiency and potential damage. By adhering to the duty cycle rating, welders can ensure that their machines run optimally, minimizing downtime for cooling and prolonging the equipment’s lifespan. This is especially important for high-amperage tasks that generate significant heat.
Welding Quality
Maintaining the duty cycle directly impacts the quality of welds. Overheating can cause inconsistent arcs and poor fusion, leading to weak or flawed welds. A machine running within its duty cycle ensures consistent temperature control, producing cleaner and more reliable welds. Adhering to the duty cycle helps maintain high welding quality standards, especially in industrial and high-precision applications.
Welding Safety
Safety is another crucial aspect tied to the duty cycle. Overheating a welding machine increases the risk of equipment failure and fire hazards. Exceeding the duty cycle can lead to power surges or unexpected shutdowns, creating dangerous conditions for the welder and the equipment. Operating within the duty cycle limits ensures a safe working environment and prevents accidents due to equipment malfunction.
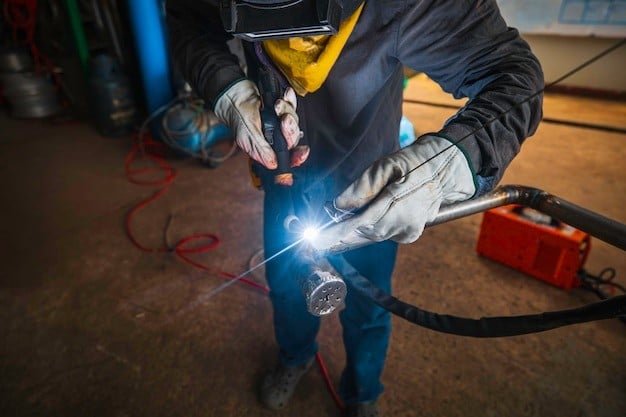
Cost Efficiency
Adhering to the duty cycle also enhances cost efficiency. Frequent overheating can lead to costly repairs or the need for replacement parts. By operating within the specified limits, welders reduce the chances of breakdowns, leading to fewer maintenance issues. In turn, this reduces operational costs and increases overall productivity.
Optimal Machine Selection
Understanding the duty cycle is essential when selecting the right welding machine for a job. Welders can match the duty cycle rating to the demands of their projects, ensuring they choose a machine capable of handling the required workload. This prevents overloading and optimizes machine performance for specific tasks.
Factors that Influence Duty Cycle
Welding Amperage
One of the primary factors affecting the duty cycle is the welding amperage. Higher amperage generates more heat, which reduces the duty cycle. Machines operating at higher currents need more frequent cool-down periods to avoid overheating. Low-amperage settings allow longer continuous welding times, while high-amperage welding must be done in shorter bursts.
Temperature
Ambient temperature also plays a significant role in determining the duty cycle. Welding machines overheat faster in hotter environments, reducing their effective duty cycle. Conversely, the machine can operate longer in cooler surroundings before reaching maximum heat capacity. Proper ventilation and cooling systems can help manage the machine’s temperature, extending the duty cycle.
Welding Methods
Different welding methods, such as MIG, TIG, and Stick, have varying duty cycle requirements. MIG welding, which often involves continuous welding, may require a machine with a higher-duty cycle to handle prolonged use. On the other hand, TIG welding, which is often more precise and done at lower currents, may not require as high a duty cycle.
Machine Maintenance
Regular maintenance is another factor that can influence a machine’s duty cycle. Clean machines with well-maintained parts tend to perform better and overheat less frequently. Dust, debris, and worn-out components can reduce airflow, causing the machine to overheat faster. Routine checks and part replacements can keep the machine running efficiently and extend the duty cycle.
Duty Cycle and Types of Welders
MIG Welding Machines
MIG (Metal Inert Gas) welding machines are designed for fast, continuous welding, which makes the duty cycle a crucial specification. MIG welding suppliers usually provide machines with higher duty cycles to handle long periods of operation, especially when welding thicker materials. For instance, a MIG welder with a 60% duty cycle at 200 amps can run for six minutes out of every ten before needing a cool-down period. Since MIG welding involves continuous feeding of the wire electrode, it generates more heat, requiring careful management of the duty cycle to prevent overheating. MIG welders often have cooling systems to maintain performance during extended use.
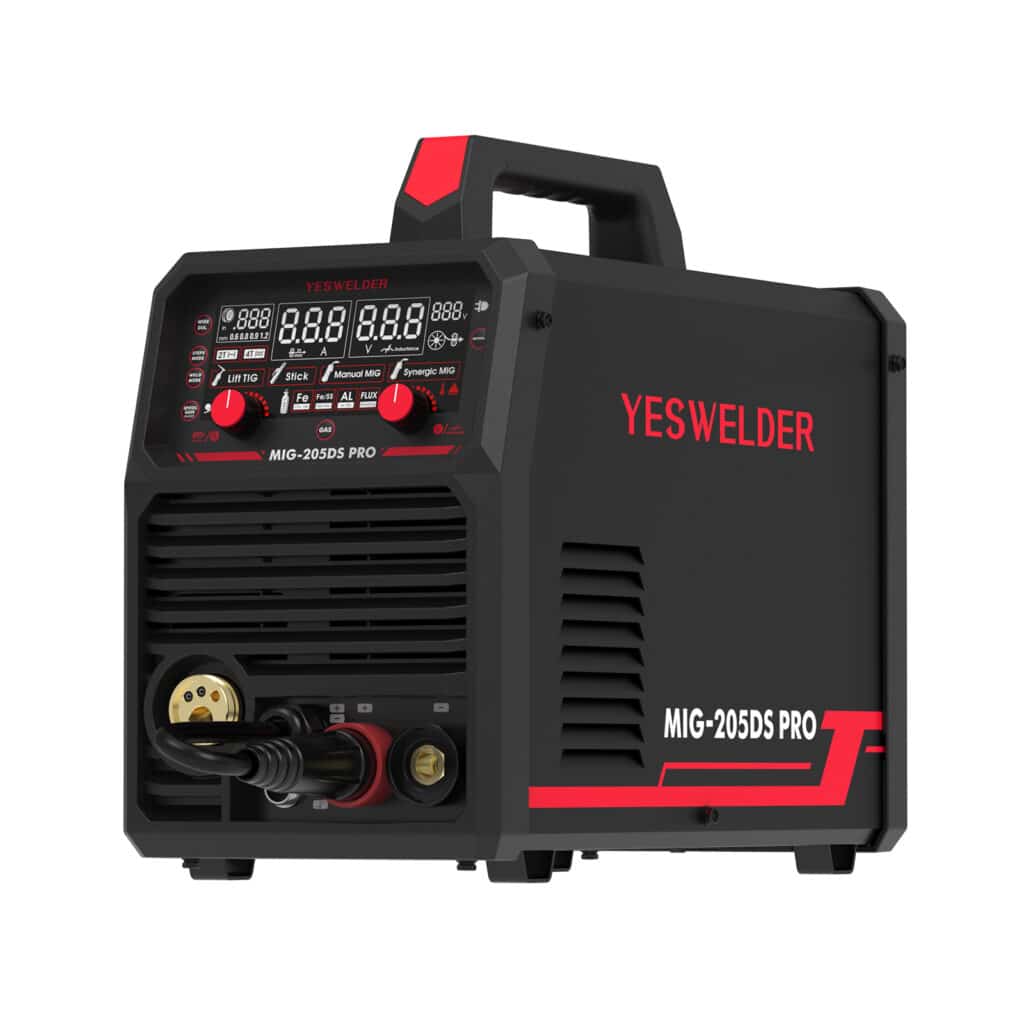
TIG Welding Machines
TIG (Tungsten Inert Gas) welding is known for precision and control and is typically done at lower amperages than MIG welding. As a result, TIG welder suppliers generally offer machines with longer duty cycles when operating at lower currents. For example, a TIG welder with a 40% duty cycle at 150 amps can run for four minutes in a ten-minute cycle before cooling down. However, TIG welding often involves more precise, intermittent welds rather than continuous operation, which allows the welder to avoid frequent overheating. The duty cycle becomes especially important in applications that require long welds, such as when working with stainless steel or aluminum.
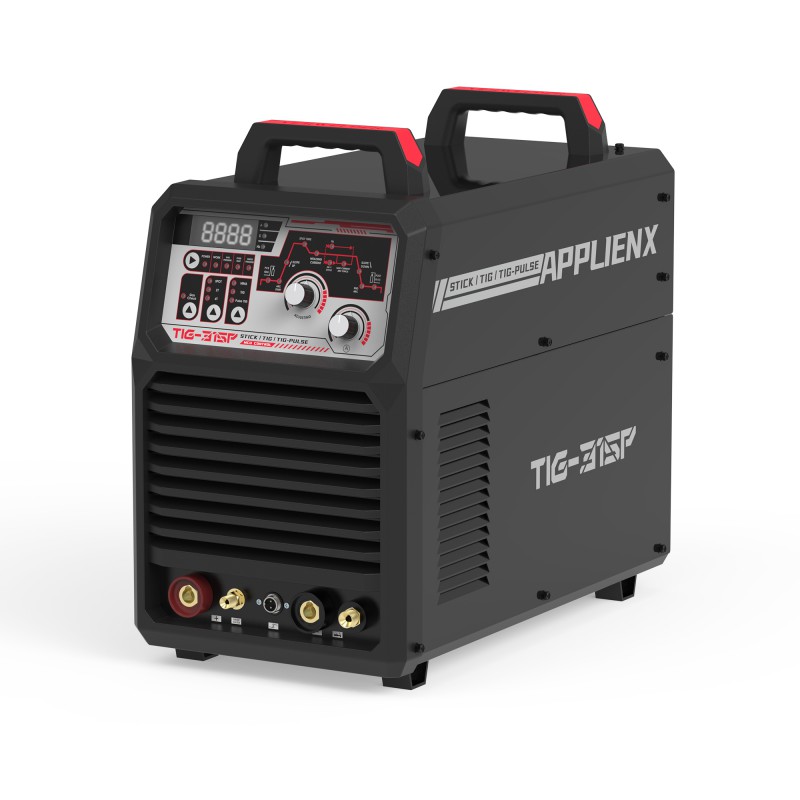
Stick Welding Machines
Stick welding, or Shielded Metal Arc Welding (SMAW), operates at higher amperages and generates more heat than TIG welding. Therefore, stick welding machines usually have lower duty cycles when used at maximum amperages. For example, a stick welder with a 30% duty cycle at 250 amps might require more frequent breaks to cool down. A stick welder supplier often has machines more rugged and used in outdoor or industrial environments where overheating can be a common concern. The machine’s duty cycle must be carefully considered, especially in heavy-duty applications like construction or pipeline welding, where long-lasting performance is essential.
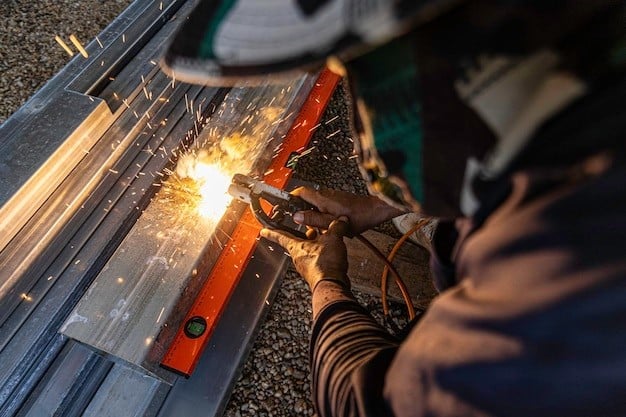
Welding Machine Types and Typical Duty Cycles
Welding Machine Type | Typical Duty Cycle Range | Common Applications |
MIG Welding Machines | 40%-80% | Fast, continuous welding tasks |
TIG Welding Machines | 60%-100% | Precision welding, fine materials |
Stick Welding Machines | 30%-60% | Outdoor, industrial welding |
How to Read Welding Machine Duty Cycle Ratings
- Check the Duty Cycle Percentage: The duty cycle is a percentage. For example, a 40% duty cycle means the welder can operate for 4 minutes out of a 10-minute cycle.
- Identify the Welding Amperage: Duty cycle ratings are typically linked to a specific amperage. Higher amperages usually result in shorter duty cycles because of increased heat generation.
- Look for Temperature Conditions: Duty cycles are often rated under standard conditions (typically 25°C). Operating in hotter environments may reduce the actual duty cycle.
- Understand the Time Frame: The rating period is generally a 10-minute cycle. The welder must cool down for the remainder of the time after reaching its duty cycle limit.
- Cooling Systems Matter: Machines with built-in cooling mechanisms might offer longer duty cycles, especially at higher amperages.
How to Choose a Welding Machine Based on Duty Cycle
Applications (Light, Medium, or Heavy Welding)
The duty cycle is essential when choosing a welding machine for specific applications. Light weldings, such as hobbyist or home use, require machines with lower-duty cycles, while heavy-duty industrial welding calls for higher-duty cycles to handle extended operations. Ensure the machine’s duty cycle matches the task’s required welding intensity.
Casual Use vs. Industrial Use
A machine with a lower duty cycle is sufficient for casual, intermittent use since it won’t be used continuously. However, machines with higher duty cycles are necessary in industrial environments where welding occurs regularly and for long periods to avoid overheating and equipment damage.
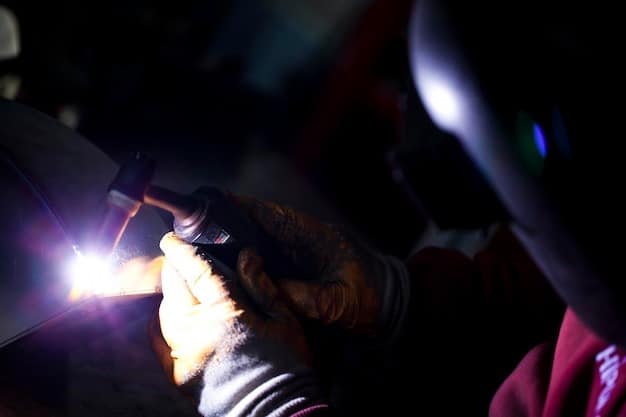
Continuous vs. Intermittent Welding
For continuous welding, such as in manufacturing or construction, select a machine with a higher duty cycle to maintain productivity. A lower-duty cycle machine will suffice if welding is more sporadic, as there will be enough cool-down time between tasks. Understanding the welding pattern ensures choosing the right equipment for optimal performance.
Safety Tips
Preventing Overheating
Always operate within the machine’s specified duty cycle to prevent overheating during welding. Exceeding the duty cycle can cause the machine to overheat, potentially leading to equipment damage or safety hazards. Ensure proper ventilation by working in a well-ventilated area and using cooling fans if necessary. Taking breaks between welding sessions also helps the machine cool down properly.
Routine Maintenance
Regular maintenance is essential for keeping your welding machine in good working order. Clean the machine frequently to remove dust and debris that can block ventilation and cause overheating. Inspect cables, connections, and components regularly for wear and damage. Replace worn-out parts to ensure optimal performance and safety. Proper maintenance not only extends the life of the equipment but also minimizes the risk of accidents due to faulty or deteriorated parts.
Final Thoughts
Understanding the duty cycle is essential for maintaining the performance and safety of welding machines. It helps welders avoid overheating, ensures consistent weld quality, and allows for better machine selection based on specific welding tasks. By operating within the machine’s duty cycle and practicing routine maintenance, welders can extend the life of their equipment while reducing downtime. Choosing the right machine with the appropriate duty cycle for casual or industrial use can lead to more efficient and safer welding operations. Always prioritize safety and proper machine care to achieve optimal results.
FAQs
What is the duty cycle in welding?
The duty cycle refers to the percentage of 10 minutes that a welding machine can operate without overheating. For example, a 40% duty cycle means the welder can run for 4 minutes, followed by a 6-minute cool-down.
Why is the duty cycle important in welding?
The duty cycle is critical for maintaining welding efficiency and safety, and exceeding it can lead to equipment overheating, damage, and reduced weld quality.
How do you calculate the duty cycle of a welding machine?
The duty cycle is calculated by the percentage of time the welder can run within a 10-minute cycle. For example, a 60% duty cycle at 200 amps means 6 minutes of operation and 4 minutes of rest.
Can welding machines overheat if the duty cycle is exceeded?
Yes, exceeding the duty cycle can cause the machine to overheat, resulting in equipment failure, damage, and unsafe working conditions. It is essential to adhere to the rated duty cycle.